End users must understand the conditions that lead to early bearing failure to choose the best technology for their needs.
08/02/2016
All pump system operators and maintenance personnel must be aware of any side effects that can result from ongoing efforts to improve the energy performance of pump systems. Negative effects can be associated with modern variable frequency drive (VFD) systems, particularly with regard to the motor’s bearing supports. To be clear, this is not about discouraging the continued proliferation of these highly effective methods; rather, it is important to understand the conditions that lead to early bearing failure.
VFD Systems & Bearing Voltages
Many pump operators have achieved significant energy savings by varying the pump speed to match the demands of the attendant system. Although there are many ways to achieve this objective, the most common is the use of electrical control or VFD systems.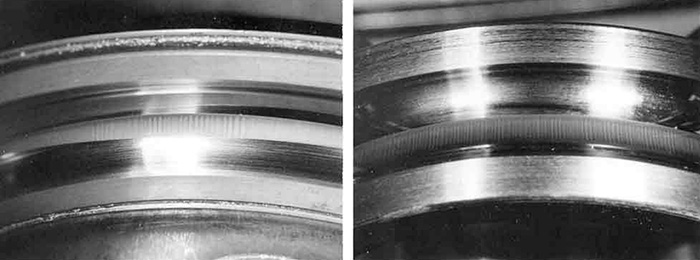
Bearing Deterioration
First, a quick primer on basic bearing design, which will focus on ball bearings because they represent the most common type of bearing used in motor applications: Under load, the points of contact between the balls and races will create a pressure ellipse because of the elastic nature of the materials selected. The exact shape of the ellipse depends on several factors, including the following:- the direction and magnitude of the bearing load
- the number and distribution of the load on the bearing’s rolling elements
- the geometric relationship between the race and the rolling element
- the modulus of elasticity of the bearing materials
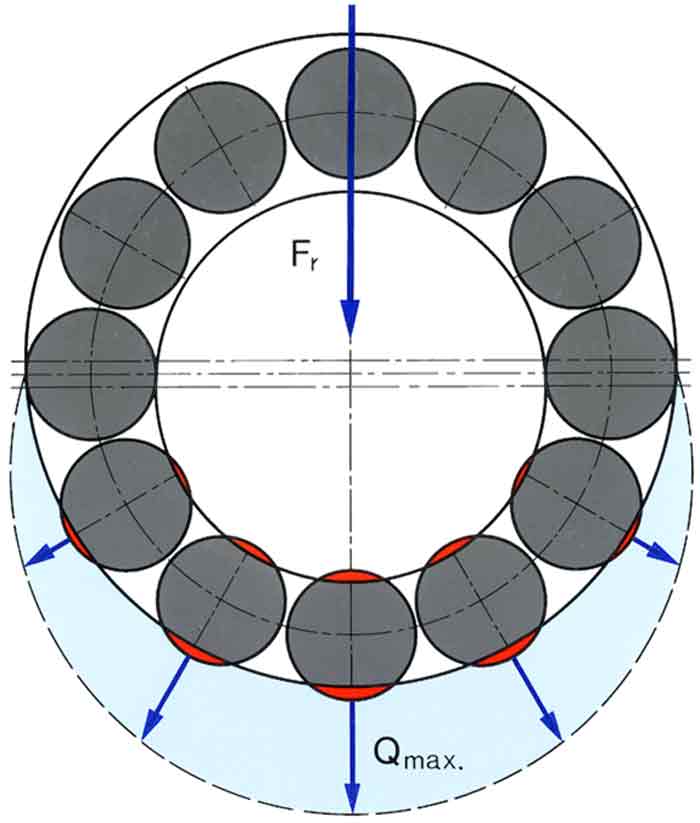
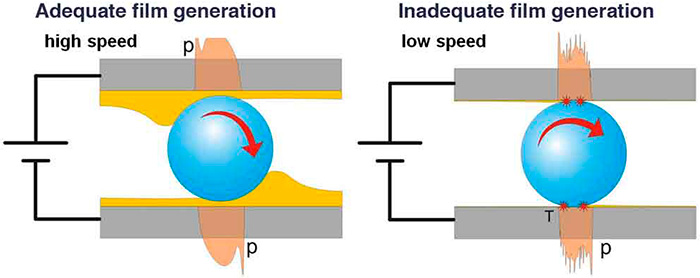
Avoiding Bearing Damage
According to some estimates, 10 to 20 percent of VFD installations will develop premature bearing failure. Evidence suggests that the probability of failure increases over time. As contamination levels rise or the lubricant’s basic lubricating characteristics degenerate, the odds grow in favor of damage. With a relatively large amount of variability related to possible bearing damage, many end users may choose to take relatively inexpensive steps to reduce their exposure and improve machine uptime. Choosing between the most economical and the most effective bearing protection usually depends on the timing of this decision. An existing pump installation may call for a different solution than what a new or reworked motor installation may require. To understand the best solution, consider the following options.Insulated Bearings
Many bearing manufacturers provide bearings with insulating capabilities that, broadly speaking, can take two basic forms: an insulating coating applied to bearing components or non-conducting rolling elements that replace the metal rolling elements. Insulating coatings—usually aluminum-oxide-based—can be applied to either the bearing’s bore, its outside diameter (OD) or both of these surfaces. The most common coating surface is the outer race’s OD because the outer ring tends to have a loose fit in the housing, which minimizes the potential for damage during installation. Coating thickness and insulating value will vary by bearing manufacturer, so when specifying bearings with insulated coatings, it is important to investigate these differences. Coating thickness, which typically ranges from 100 to 200 micrometers (μm), is a good indicator of the protection level. Perhaps a better indicator of insulating value is the disrupted voltage that the coating is capable of providing. Because a coating’s effectiveness depends on time and moisture, higher disruptive voltage values should be considered. Bearings using non-conducting rolling elements are typically known as hybrid bearings. This method of preventing damage provides a more effective barrier than coatings and practically eliminates any possibility of EA. The non-conductive rolling elements used in hybrid bearings are normally silicon-nitride balls, although other ceramic materials are also employed. Initially limited by the high cost of ceramics to only a few highly engineered applications, hybrid bearings are now more readily available because of more economical ceramic balls. The higher modulus and lower density of the ceramic materials used in hybrid bearings give them additional advantages: The material’s stiffness reduces rolling friction while its light weight reduces the balls’ angular momentum losses. This configuration reduces energy consumption in the bearing by up to 20 percent.Rotor Grounding Methods
Another common method of protection is to provide a low-resistance grounding path for the rotor. This eliminates any electrical potential and, consequently, any potential for arcing. The basic requirement is that a rotating connection makes contact with the rotating rotor, conducting any electrical charge into a properly grounded motor base. This rotating connection can take various forms, including shaft grounding rings, spring-loaded brushes, annular brushes or rotating couplings. A particularly promising method of protection under development involves establishing an electrical path through the bearing itself. This is accomplished by using a conductive material in the same general region as the seal. Unlike the non-conductive seal, this solution would allow current to pass without damaging the bearing’s rolling surfaces. A cutaway of this concept is shown in Figure 3.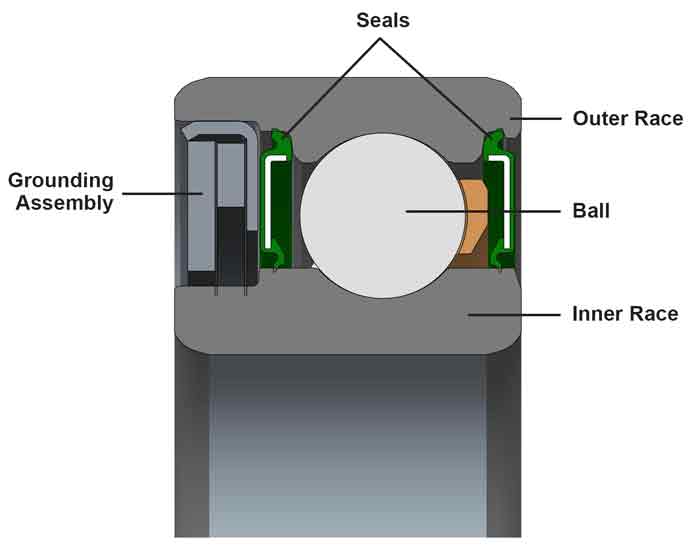
Conductive Bearing Methods
While VFD systems are an effective tool for improving pump system efficiencies, they create conditions in the controlled motor that can cause electrical arcing inside the bearing. This can lead to premature equipment failure. There are several methods to protect the bearing from damage, and the best solution depends on the individual installation. As a general rule, considering the inherent energy savings offered by hybrid materials, a hybrid bearing can provide the lowest-cost solution for new or rebuilt applications. For existing installations, on the other hand, grounding devices offer a compelling cost-effective method of protection. Considering the high cost of unscheduled motor bearing failure, providing some form of protection is always a sound investment. References- D. Busse, J Erdman, R. Kerkman, D. Schlegel, and G. Skibinski, “Characteristics of Shaft Voltage and Bearing Currents,” IEEE Industry Applications Magazine, Vol. 3, No. 6, pp.21-32 Nov.-Dec. 1997
- A. Willwerth, Electro Static Technology-ITW 31 Winterbrook Road, Mechanic Falls, ME 04256
- R. Toney, EIS, Motion Industries, 7111 North Loop E. Houston, TX
- C. Rechlin, Mercotec Inc. USA, 6195 Corte del Cedro #100 Carlsbad, CA 92011
- Wayne C. Turner & Steve Doty, Energy Management Handbook, 6th Edition