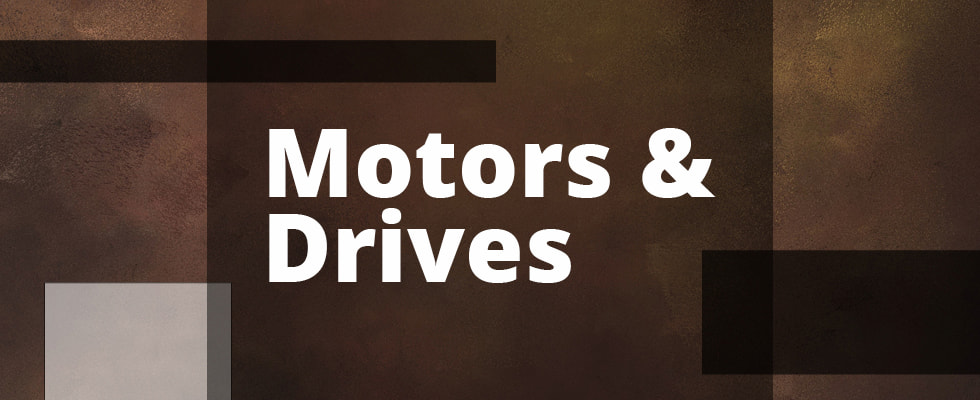
When it comes to selecting the large motors that run compressors in low-density polyethylene (LDPE) and air separation plants, user considerations include financial investment, environmental impact and long-term reliability. In short, users are looking for the lowest total cost of ownership (TCO).
Big money rides on the success of compressor operations in LDPE and air separation plants. This includes the sales value of the gases and chemicals; the cost of the energy to run them; and the price paid for operational reliability, maintenance and downtime.
End users understand that downtime costs should be avoided. Let’s look at an average LDPE plant making 250,000 tons of LDPE per year. If the plant runs annually at 8,000 hours and the product sales price is $1,500 per ton, this gives an LDPE production value of about $47,000 per hour. So, over 24 hours, that is $1.1 million. For a 400,000 ton plant, the value jumps to $1.8 million per day.
Electrical energy and carbon dioxide (CO2) emissions also have a major impact on TCO. Electricity costs are the largest component in a TCO calculation for motors on LDPE and air separation lines. The estimated savings from this improvement amounts to $500,000 in electrical energy over the 20-year lifetime for each motor. Savings like this can significantly impact profits, but the environmental benefits are also substantial, saving an estimated 86 tons of CO2 greenhouse gases over 20 years.
Reliability Is Priority
Operators of LDPE and air separation plants typically want processes to run nonstop and for several years. Achieving the best availability and reliability hinges on tailoring an effective maintenance program. When maintenance work is done, it must be executed with the highest efficiency. To achieve this, users need modern maintenance practices and advanced design.
A common choice is reciprocating compressors powered by fixed-speed synchronous motors. In addition to these big-ticket hardware items, LDPE plant builders also seek the assurance that modern engineering tools like 3D modeling, finite element method (FEM) analysis and advanced accessories are part of the solution.
The “Build-Own-Operate” model is commonly used in the air separation business. Customers not only see the initial investment cost but also, and more importantly, the ongoing operating, electricity, availability, downtime and maintenance costs. All these components make up the TCO for a given plant and equipment solutions should be tailored to actively minimize many of these. Compressor motors typically last a long time while running with high electrical energy efficiency and supported by tailored maintenance routines.
Unplanned downtime is a killer when it comes to TCO. Critical maintenance questions must be fully explored before making any purchase decision. Equipment is expected (unrealistically) to run 100 percent of the time.
This is unrealistic, but necessary precautions can be taken to reduce maintenance time and unplanned stops to an absolute minimum.
The first step is to work with suppliers that have progressive maintenance programs, allowing for advanced planning and ensuring full support at all times. Predictive maintenance practices are now becoming more powerful and can have a positive impact on TCO.
Considering Grids & Power
Motors do not operate in isolation but are run by a grid. Large motors can have an effect on the connecting network, which can cause disturbances that directly or indirectly impact on TCO. The challenge here is to build a large motor that has a low starting current, thereby avoiding an undue impact on the grid and reducing the need for expensive, complex switchgear.
With a synchronous motor, as opposed to an induction motor, you can control the rotor current at all times. A programmable logic controller (PLC) or automatic voltage regulator (AVR) solution can be used to configure the function and include relays and protection devices. The result is high flexibility to suit the specific starting method and inrush current needed.
Direct-on-line (DOL) starting is typically the preferred method for LDPE compressor motors due to the simple design and low cost. For higher power motors, the starting event may need more precise control. In this case, there are numerous possible solutions. For the biggest hyper-sized compressor motors, users may want to use a variable speed drive (VSD) or an auto-transformer starting method.
All in all, taking the time to fully analyze starting strategies can enable users to choose what is most effective, and this will pay off nicely in terms of fewer disturbances and lower TCO.
The power factor is closely related to the impact a motor can have on an electric grid and should be included in any TCO calculation. A synchronous motor makes it possible to control the reactive power using a design that compensates for the power factor required on the supply grid. If power factor control or reactive power compensation is needed, then a synchronous motor can be used instead of an induction motor.
The power factor for a synchronous motor is normally in the range of 1.0 to 0.8-leading. When it is leading, the motor produces reactive power to the grid. Sometimes there is a fee for reactive power that the customer needs to pay, although this may be handled with capacitor banks.
Design That Meets the Plant’s Needs
Today’s trend toward higher power and loads is motivated by the direct TCO benefits they provide: bigger motors can run bigger compressors. The higher-powered units mean that plants can get the same output from fewer compressor trains, providing savings in engineering time, space and capital investment costs.
Cooling is another key area to consider. The right cooler can bring TCO benefits by getting the highest output, reliability, uptime and efficiencies.
No calculation of TCO would be complete without taking into account the issue of safety. LDPE and air separation processes involve potentially explosive chemical atmospheres where risks must be managed and minimized.
Failure to comply with safety regulations and standards can be costly to users’ TCO in terms of equipment damage and injury to people, lost production and fines by authorities.
Many variables must be considered when choosing motors for larger compressor operations: purchase price, energy and operating costs per unit of production, and downtime and maintenance expenses. Users should systematically analyze all cost factors over the projected lifetime of the plant and reach an accurate TCO estimate.