End users must consider many variables to choose the better solution.
Power Electronics
10/25/2016
An overlap between 460 and 4,000 volts exists where multiple types of motors and starters are readily available. The question, though, is which one is better? Like most engineering questions, not only does the cost need to be considered, but also the differences in each operating voltage in the context of the application.
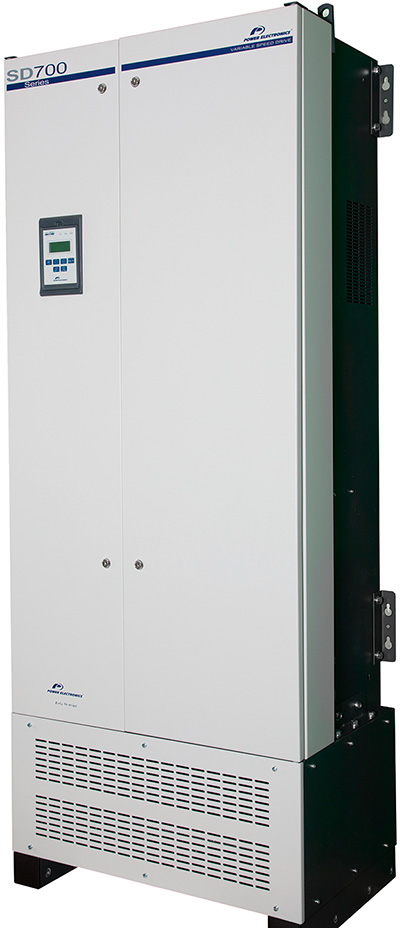
Choosing a Starter
The motor starting amps of 600 percent or more and the ability to supply those amps influence the choice of a starter. A 460-volt motor takes about nine times the current of a 4kV motor for the same rating. For reference, a 500-hp LV motor would be rated for 580 amps versus 70 amps at 4kV. Understanding what the utility will allow or what the grid can support should be part of the evaluation for determining the starting method. There are three basic means of starting: across the line, also known as direct on line (DOL); soft starting or reduced-voltage starting; and variable frequency drives (VFDs) for starting only or continuous operation. An LV mechanical starter, even for a 500-hp motor, is not practical because of cost. Few power grids can handle the inrush of more than 3,500 amps without significant voltage drop. The common option for LV above even 100 hp is a soft starter. The current can be reduced to 250 to 450 percent of the motor full-load amperes (FLA) depending on the motor loading at starting. LV VFDs are available even at 2,000 hp or larger. They are made by taking the largest single-stage VFD from a vendor, typically around 500 hp, and putting two together to achieve 1,000 hp or three to reach 1,500 hp. With each added block, the price goes up. As a result, the soft starter, which may only be 30 to 50 percent of the VFD cost, can look attractive. The reduced cost of VFDs in recent years and their ability to improve process efficiency have made them a more common choice. Even when not required, VFDs are often requested because of the familiarity with the technology; their reduced cost and flexibility make them easy to apply.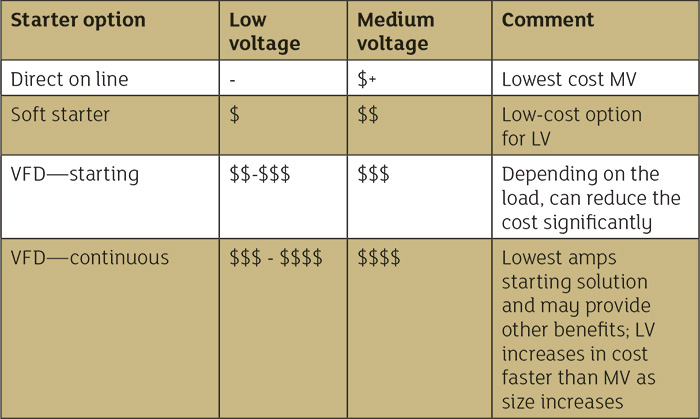
Other Considerations
There are differences in the equipment beyond horsepower and voltage that end users should consider. Most LV drives are not Institute of Electrical and Electronics Engineers (IEEE) 519 compliant as standard, common on MV VFDs. Most utilities require IEEE 519 compliance in some form. The MV VFDs can include short-circuit protection and a disconnect for a relatively low cost. For the LV VFD, it must be added to the switchgear or a custom package. Larger-horsepower installations may come with the expectation of a longer operating life in excess of 20 years, so specifications may need adjustment. All induction motors are reliable, but an MV motor with formed coils that has been vacuum pressure impregnated statistically is more reliable than an LV random-wound motor winding that has been dipped and baked. If reliability is important for the application, an LV motor spec will call out IEEE 841, which is similar to American Petroleum Institute (API) 547 for MV. LV motors cannot meet the higher API 541 specification—this is why critical service motors will be MV even at 250 hp.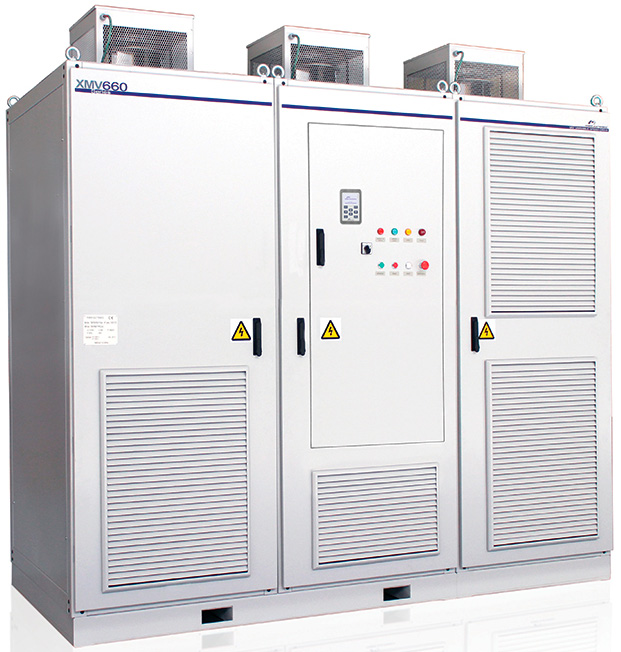
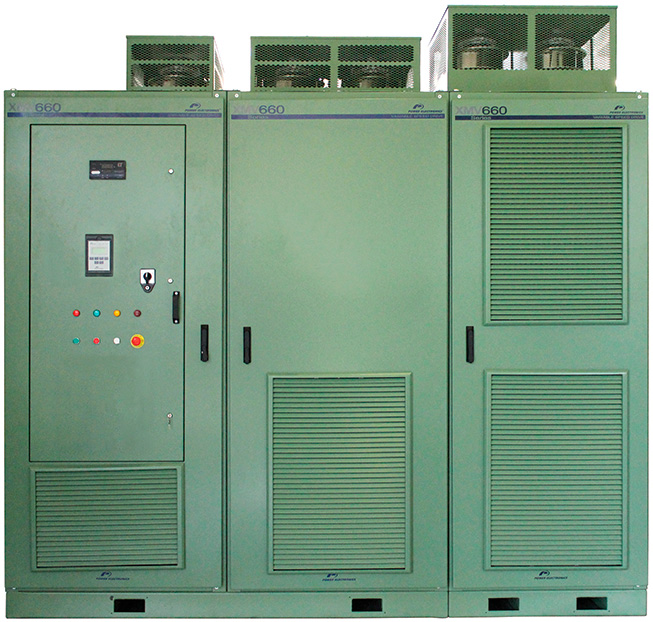
To read more Motors & Drives articles, go here.