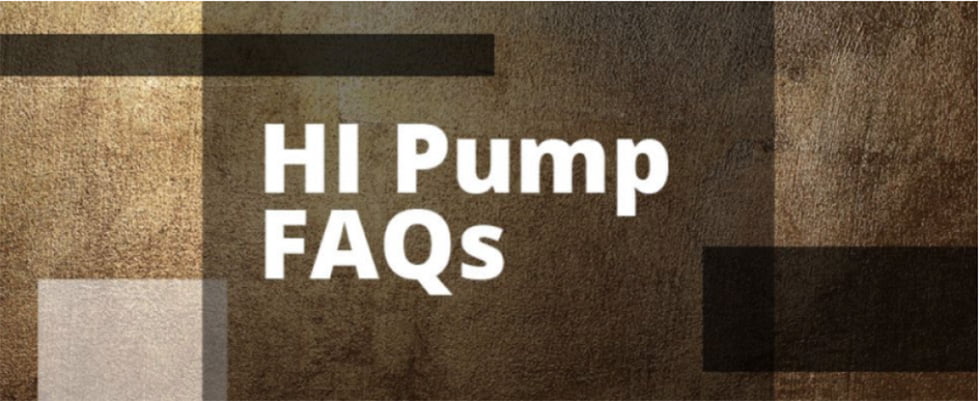
How do I identify pump faults using vibration monitoring?
Rotating machinery like pumps will vibrate at certain frequencies that are related to the physical design. When looking at the vibration, the level and frequency can indicate the health and condition of the rotating components of a pump. Vibration monitoring can be implemented by taking consistent measurements of vibration signals to detect changes in the health and condition of the rotating components.
The simplest way to detect and gauge a problem is using an overall vibration measurement. Overall vibration means that it includes all the frequencies at which vibration is occurring that are within the analyzer’s set range, and the analyst is simply trending and comparing similarly gathered data. If the overall vibration exceeds a certain level or increases by a set amount, it could indicate a problem that needs to be evaluated in more detail.
However, the overall vibration measurement typically provides little information about the cause of the vibration. To determine the cause of the vibration, more detailed analysis is required. Some types of faults that vibration monitoring can detect are:
- imbalance of rotating elements
- misalignment of rotating elements
- rubbing
- equipment support system (soft foot, looseness, grouting, etc.)
- resonance
- bearing problems (journal and rolling element bearings)
- gear tooth damage
- cavitation
- eccentric or broken rotor bars
- drive belt and coupling problems
Some analyses that can be conducted to identify the cause of the vibration are as follows:
- time waveform, frequency spectral and phase analysis
- continuous monitoring while monitoring other system conditions
- operating deflection shapes (ODS)
- experimental modal analysis (EMA)
- finite element analysis (FEA)
- other advance and proprietary methods may also be used
A majority of the faults can be identified with a combination of bullet points one and two, but bullet points three through five may be required to solve the vibration issue if it is related to resonance or inadequate support.
As an example, imbalance of rotating elements is a common excitation. Image 3 illustrates the typical frequency spectrum and phase for an overhung pump with imbalance.
There will be elevated vibration at the operating speed (1X), and the axial phase readings should be similar. In practice, there will be other complicating factors, and it will not be as clear as shown in Image 3.
For example, there could be structural looseness that is allowing the structure to move more freely in one direction, or there could be some resonance that is amplifying the vibration consistent with the mode shape of a natural frequency. In this case, the excitation may be imbalance (that is within acceptable levels), but the resulting 1X vibration is high due to these other conditions. If this is the case, the spectral and phase analysis may not be sufficient to determine the cause, and the use of ODS, EMA or FEA may be needed.
For more information on determining the cause of pump vibration, refer to HI’s training on Troubleshooting Rotodynamic Pump Vibration at training.pumps.org.