Measurements aid in recognizing and remedying adverse operating conditions, including cavitation and safety issues.
AW-Lake Company
08/22/2019
Pump system designs keep evolving, offering greater accuracy and reliability for users. While design specifications improve, different conditions can negatively affect operation. Parts still wear and unintentional conditions can cause pumps to perform incorrectly or fail. Downtime associated with pump repairs, replacement and/or adjustments is expensive. In many applications, pumps must keep functioning to ensure accurate system operation. Performance and preventive maintenance indicators are becoming more critical to ensure production keeps running without interruption and at peak performance.
Performance in a Closed-Loop System
To help pumps run optimally, the addition of an in-line flow meter provides diagnostics information that provide insights into pump operations. As a passive device, a flow meter is the truest indicator of the actual flow in a pump system. Its basic function is verifying actual flow versus required flow based on pump revolutions per minute (rpm). If the supply tank to the pump is running low on material, a pump will still run, trying to push out material as it does not know the tank is running empty. Adding a flow meter provides direct feedback on how much fluid is coming from the pump and immediately indicates when a supply system runs low on material. For example, in a two-component system like a truck bed liner spraying polyurethane coatings, running out of one component can require scrapping or refinishing completed products, resulting in unexpected costs related to material, rework time and scrapped goods. A high-accuracy gear meter installed in each pipeline can monitor the flow rate of components as part of a closed-loop feedback control system.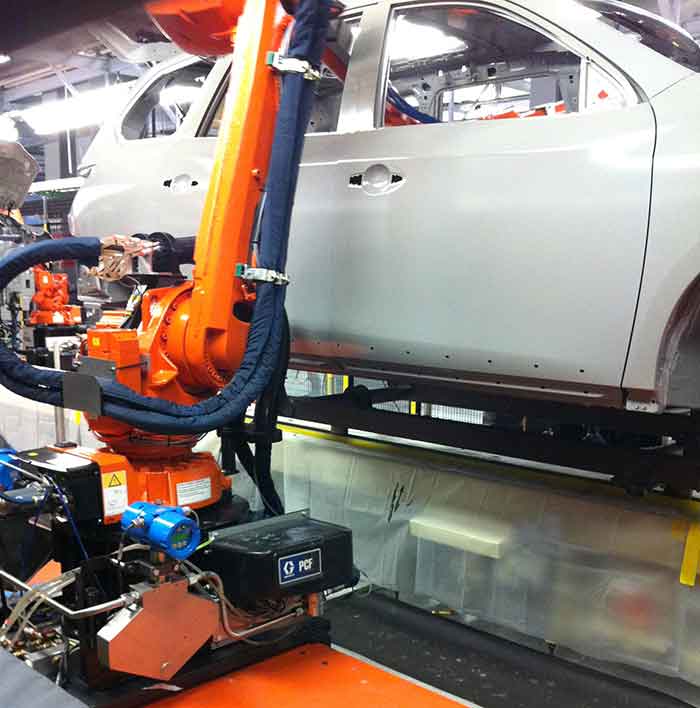
Avoiding Pump Cavitation
In all applications, the liquid supply to the pump must have sufficient pressure to deliver fluid to the pump at all rates to avoid pump cavitation at higher pump speeds. It is the expectation of any system that as pump speed increases, so does the output flow rate. However, if the pump inlet supply pressure is not sufficient, a vacuum can develop and cavitation can occur. Pump cavitation not only causes downstream production problems from lower than required flow rates, but can also damage pumps. The combination can result in scrapped production and a damaged pump, requiring replacement and expensive downtime. Installing a Coriolis flow meter on the pump outlet monitors the flow rate versus the pump speed to help determine if the supply pressure to the pump is sufficient to keep up with increasing output demand as pump speed increases. Feedback on these parameters provides the ability to both improve the system and catch problems such as drop-in supply tank pressure. In addition, when pump cavitation begins, air bubbles often are introduced into the outlet stream. Initially, bubbles may be too small to cause obvious flow rate changes that other flow meters could detect. When used to monitor the fluid density, a Coriolis flow meter can quickly detect the start of pump cavitation as air bubbles change the fluid density. With an early warning of pump cavitation, operators can stop the pump and correct the problem, avoiding pump damage and downstream production problems.Monitoring System Health & Safety
When installed, a flow meter can monitor general system operation and health. In timed dosing applications where a fixed volume container is filled with a liquid, the amount of dispensed liquid relies on a constant flow rate over a timed dispense cycle. The rate is usually set via a precision valve or orifice at the system outlet. Over time, the orifice diameter or valve stem can wear and cause an increase in flow rate. An undetermined increase in flow rate results in putting more than required material in the container or, even worse, overfilling a container that causes spills. By installing a high-resolution gear flow meter, changes in flow rates continuously are monitored over time. Operators can correct any flow deviations during scheduled maintenance. In many applications, flow meters help ensure the safety of a pump system. By comparing actual system flow rate output with the requested pump delivery, operators can determine the presence of system leaks. Systems in remote locations or those not visually monitored regularly may develop pipe or seal leaks that could go undetected for hours or days. By monitoring the fluid flow, especially when no flow should be present, output from the flow meter could serve as a warning for an operator to shut down the system and look for the leak. In applications where measured liquid is hazardous, early indication of a leak could avoid a critical situation. Sudden leaks or bursts in pipes and seals in high-volume and high-velocity systems could cause serious injury to nearby operators. Through the quick response time of gear or Coriolis flow meters monitoring both a sudden flow increase and the rate of change, a system can automatically shut off the supply pump and energize a safety valve that either shuts off the line from the outlet of the pump or diverts the flow back to the supply tank. Automating such safety functions versus an operator manually shutting down the system can sometimes mean the difference between life or death, especially in a system with high-horsepower pumps.Benefits of Coriolis Mass Meters
- “All-in-one” instrument: direct measurement of mass flow, density and temperature, calculated measurement of volumetric flow
- No moving parts: low maintenance, lower accuracy drift over time
- Easy to install: no straight run of pipe required and multiple mounting options available
- Mechanical design resists external interference (i.e., vibration)
- High-resolution output up to 10,000 Hertz (Hz)