In modern industry, hundreds of millions of horizontal process pumps move fluids. The larger of these, typically pumps in ranges above 500 kilowatts (kW), incorporate sliding bearings. Except for a relatively small number of pumps with product lubrication or with exotic and expensive bearings, horizontal process pump bearings need oil lubrication. Part 1 of this series dealt extensively with lubrication. Part 2 discusses lubrication matters but focuses on bearings and surprising findings on allowable bearing temperatures. Figure 1 illustrates the extended temperature ranges available from modern synthetic lubricants. Properly formulated synthetic lubricants allow continuous operation at 400 degrees F (205 C). Although no rolling element bearings in process pumps are ever exposed to this temperature, it would be correct to point to the information conveyed by Figure 1. It supports the findings that premium synthetic formulations can be used with every bearing style or configuration found in process pumps.
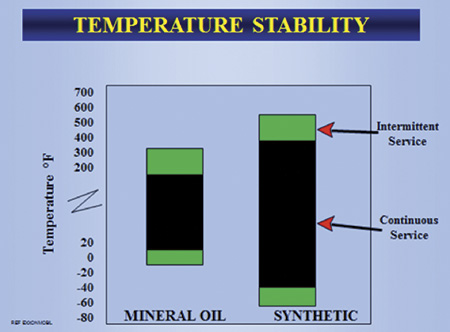
Bearing Styles & Configurations
Process pumps incorporate a radial bearing and a thrust bearing. A radial bearing is usually located near the mechanical seal, and the thrust bearing is fitted close to the drive end. Fluid pressures acting on impellers cause a net axial force on the shaft system, or axial thrust. In operation, thrust acts in one direction, which would make the two tandem-mounted bearings in Figure 2(a) suitable for thrust acting from right to left. If the bearings are precision-ground, they will share the load and each will carry 50 percent. If they are not precision ground, the configuration will create issues.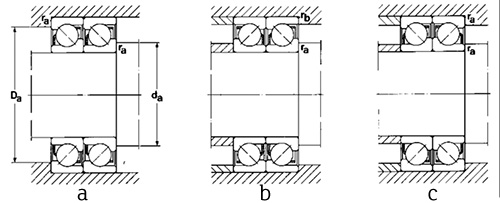
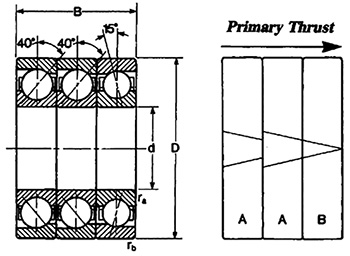
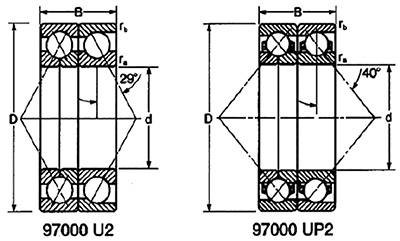
Bearing Temperature Limits
Among the many references linking bearing health and life expectancy, both in the plant and the field, Figure 4 stands out because of its general applicability. The illustration pertains to the thermal range of a typical rolling element bearing. Bearing metal temperature is often higher (10 to 25 C) than the oil temperature in the bearing within an oil circulation system. In non-circulating systems, bearing metal temperature is more likely 5 to 10 C higher. The green zone in Figure 4 represents the optimum zone for bearing and lubrication temperature. Operating in the yellow zone will reduce lubricant and bearing life. If bearing temperatures are in the red zone, expect both the bearing and a mineral oil lubricant to be severely compromised. Pump bearing housing temperatures around 160 F are normal. This temperature is near the center of the green zone. Yet, bearing housing temperatures of 190 F are allowable and will likely occur in process pumps if an unnecessarily high oil viscosity is selected. Bearing manufacturer MRC states that its brand of rolling element bearings will run in continuous duty at a temperature of 121 C. Therefore, operating at 190 C, while perhaps wasteful if the oil is unnecessarily viscous, is permissible. However, be sure to add a personnel protection guard.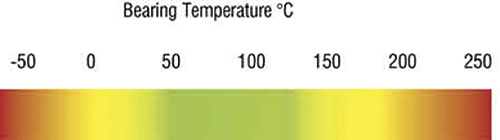
Optimized Application
Lube application methods include grease, oil flooding, and oil rings or slinger discs used to bring lubricant from an oil sump into the bearing elements. Thousands of plant-wide oil mist systems have been in highly successful use since the early 1960s. As of 2015, an estimated 135,000 pumps and 26,000 electric motors are lubricated by oil mist. Only jet oil application is ranked higher than oil mist (see Figure 5). Jet oil lubrication applies the filtered lubricant precisely where needed and dispenses with constant level lubricators.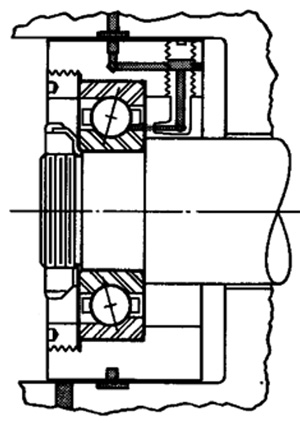