More and more, OEMs and operators of pumps used in diverse industries such as oil and gas, water treatment, and food and beverage employ advanced digitalization technologies to optimize pumping systems operation and maintenance. Among those technologies are digital twins—virtual 3D proxies of their physical counterparts—applied with sophisticated analytics and artificial intelligence (AI)-enabled machine learning. Together, they can enable a concept called “smart pumping” with many operational advantages and benefits. Smart pumping, for example, can enable OEMs to enhance their offerings’ features and capabilities, especially remote condition monitoring, diagnostics and serviceability, while operators can realize savings in downtime and energy use. The results in real time point to operational anomalies that can be investigated and mitigated or remedied before costly disruptions occur. And, with more proactive—even predictive—maintenance models, operators can extend component and system life cycles, lowering total cost of ownership (TCO) for decades of use. TCO can dwarf initial capital investments of complex pumping systems, such as those moving fluid through long-distance pipelines. Digital twins evolved from 2D and 3D computer-aided design (CAD) and computer-aided engineering (CAE) software applications. In effect, these application outputs become inputs to even more sophisticated software running on workstations. Digital twins can be viewed with granularity from all angles, even operated in digital form under specific conditions to study rotary and reciprocating motions. Digital twins can also be shared from a common engineering repository across different engineering disciplines, with modifications documented and traceable to a particular team or individual. They can also be used for virtual commissioning and personnel training, even before a pumping asset gets built. Image 1 shows how tech-enabled smart pumping can support the life cycle management of what could be an entire pumping facility, whether inside a single plant or across a distributed pipeline system spanning hundreds or thousands of miles. Engineers, operators, maintenance technicians and OEMs with the proper access privileges can examine virtually any detail of its constituent facilities—pump stations, for example—or any of their components, such as compressor trains and supporting infrastructure. The digital twin can investigate and test optimization scenarios to troubleshoot operational issues as they occur and, most importantly, mitigate or remediate them before costly disruptions.
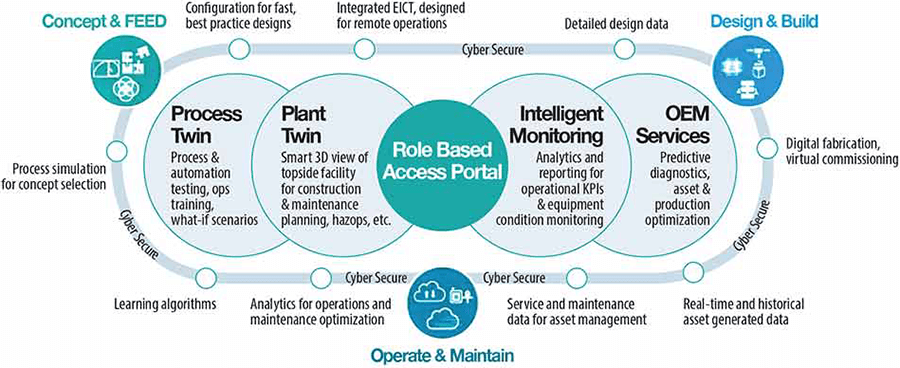
1. Process Twin
Digital process twins can keep a pumping system’s commissioning time and costs to a minimum, then continue to deliver value during its entire life cycle. Engineers can conduct dynamic process simulations over a wide range of the system’s features and capabilities before its manufacture or construction, rather than making changes afterward. Simulations can include testing simple input/output (I/O) or signal of a pumping system’s controls to ensure its logic and functionality works properly. They can also be used to optimize a pumping system’s process and to train personnel via virtual commissioning in parallel with manufacture or construction to save weeks or months of time.2. Plant Twin
Digital plant twins can use 3D engineering data—especially as-built documentation—throughout a pump or pumping system’s life to provide a virtual-reality viewer for 3D models of them. Engineers can test the instrumentation control and safety system (ICSS) in advance of manufacture, in the case of single pumps, or with larger pumping systems, ahead of construction, commissioning and startup. Also, engineers can use a digital plant twin to switch between 2D drawings and 3D representations via a centralized engineering data repository—a single source of truth—which can enhance cross-discipline collaboration, save time and reduce errors and miscommunications.3. Intelligent Monitoring
Intelligent monitoring of pumping systems is enabled through web-based analytics and visualization capabilities that can include:- physics- and rule-based analytics of pump performance key performance indicators (KPIs)
- control loop and alarm system performance
- AI-driven machine learning for monitoring and optimizing the performance of pumping system components, such as compressors, turbines and drives
- daily, weekly and yearly maintenance and operational KPIs
- maintenance alerts