In today’s industrial world, going small can result in big savings. Hydraulic systems, for example, are getting smaller as part of a larger effort to improve fuel economy in industries across the board. The logic behind this is that a physically smaller hydraulic system weighs less, and that translates into greater fuel economy. However, such a size reduction is not accomplished without risks. First, flow rates are increased relative to oil volumes as a result of less oil use. Issues related to oil residence, such as very short oil residence times because of the compact nature of the smaller systems, can lead to situations in which oil remains at elevated temperatures for extended periods of time. The reduced residence times also mean that the oil has insufficient time to cool to an ideal level. In some cases, temperatures as high as 266 F have been measured. This kind of heat can result in a high amount of oxidative and thermal stress on hydraulic oil. Another undesirable effect from reduced residence times in the reservoir is that contaminants—such as foam, water and wear debris—are unable to settle. Instead, the contaminants remain suspended in the thermally stressed oil, causing it to break down and form varnish, a tacky substance. Varnish can cause poor hydraulic valve response, which occurs because of sludge and varnish buildup. Varnish can also result in an increased need to replace blocked filters. When varnish forms, it creates a chain reaction within the hydraulic system, ultimately causing erratic operation, increased wear on valves and pumps, shorter oil life because of increased oxidation, less fuel efficiency and increased downtime.
What Is Varnish?
When polymerized oil oxidation products and decomposition byproducts are produced as a result of thermal breakdown, varnish forms. Varnish is identified by its sticky brown appearance. It typically forms on pump housings, reservoirs and filters, and valve spools and bodies (see Image 1).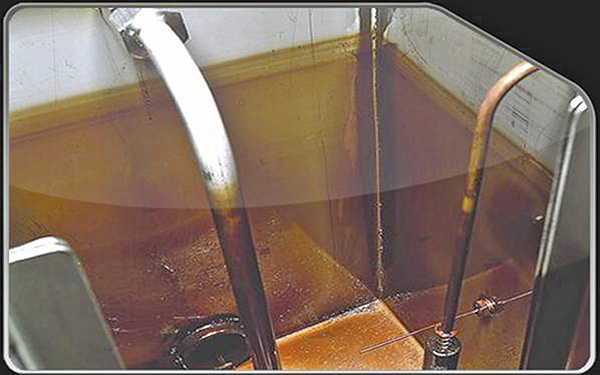
Why Is Varnish Bad?
Generally speaking, most operators realize that varnish has formed when the hydraulic actuator begins to operate erratically. The cylinder will appear to stick, but it is actually the spool in the valve body that is not operating freely. If operators are unaware of the cause of this sticking, they may inadvertently cause more equipment damage by calling for more flow than is needed. Varnish increases friction, which negates any power savings that were gained by the smaller systems. Such friction also generates wear. Since varnish tends to attract and hold onto wear metals, friction and wear are increased. This wear can occur in the valves, the cylinders or the pump.Cleaning Existing Varnish
Until recently, operators and maintenance professionals only had two key prevention techniques to rely on to prevent/limit varnish formation:- Use a higher-quality oil with improved base stocks and increased levels of additives
- Implement a high-end filtration system
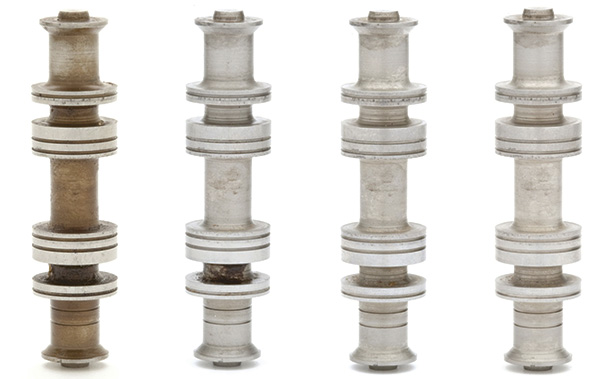
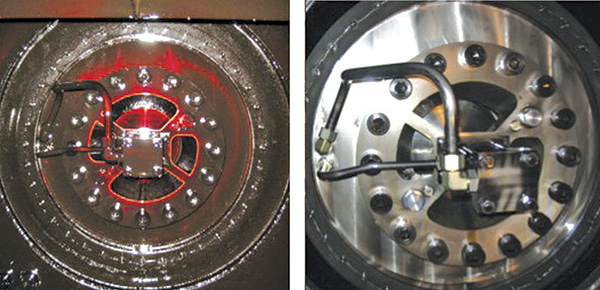
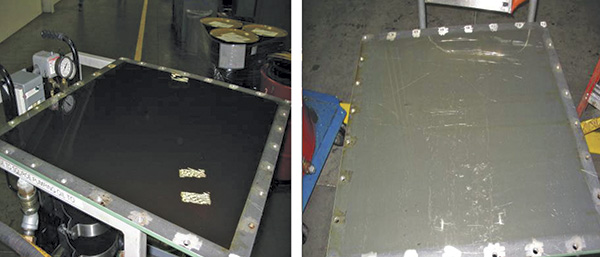
Preventing Future Buildup
The oil manufacturing company also engineered a hydraulic fluid containing its patented, fully formulated, anti-wear additive system, specifically designed to prevent varnish formation. The additive works by dispersing and suspending varnish precursors and varnish as they materialize, allowing a hydraulic system’s filter to remove the deposits. To prove the effectiveness of this hydraulic fluid, a partner company submitted the oil manufacturer’s additive technology to the same vane pump test for an extended 1,000-hour interval in a pre-cleaned system. Conventional hydraulic oils began to show tenacious varnish at 500 hours, with varnish observed in both zinc and ashless oils. Comparisons between the performance of standard fluid technology and the oil manufacturer’s additive technology can be seen in Image 5.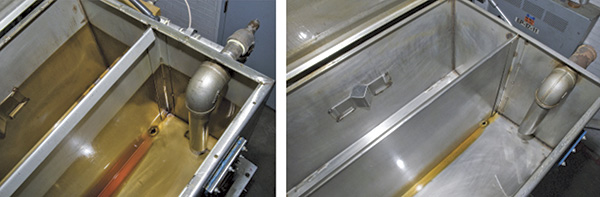
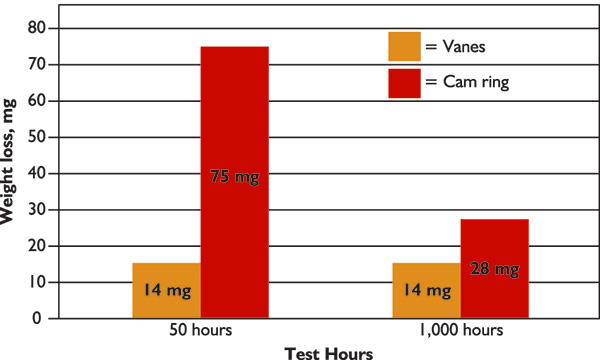