The high density of rotating equipment used in refineries means that effective asset management of pumps, turbines, compressors, motors and generators can play a vital role in maintaining plant uptime and achieving overall equipment effectiveness targets. Diligence in this area can also ensure high safety levels and profitability. Because every refinery operates with steadily aging equipment, these facilities, including petrochemical refineries, must execute the most cost-effective maintenance programs possible to improve asset performance and reliability. Daily production costs within refineries can escalate quickly, so keeping production equipment and components running at optimum performance levels is crucial for delivering a positive bottom line.
Understanding the Costs
Rotating components within any production process will eventually wear and require service or replacement. The type of maintenance program that is used can mean the difference between a good investment and unnecessary expenditures.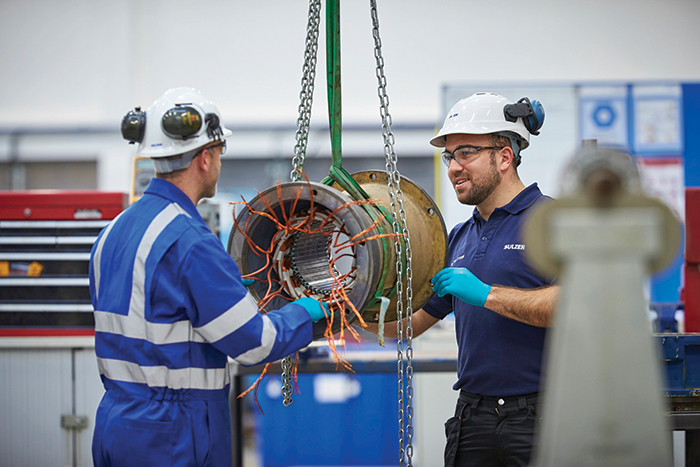
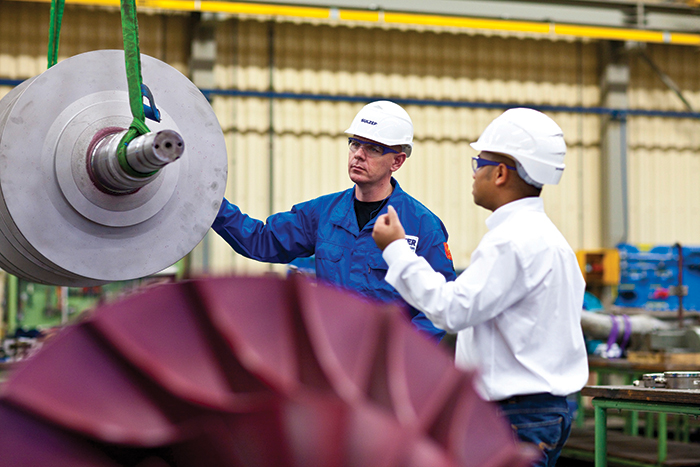
Reactive & Preventive Maintenance
Historically, many refineries have employed a reactive maintenance policy by which assets are replaced or repaired on a fix-as-fail basis. This method may deliver some cost savings in the short term, unless a more serious failure occurs. Reactive maintenance relies on the skills of the on-site maintenance team and the availability of spare parts. If either of these factors fails to meet expectations, substantial losses may result because of lost production. The purpose of preventive maintenance is to use all available information and techniques to identify assets that require service intervention and schedule the work to be completed as a preventive measure. In this way, the work can be scheduled to cause minimal disruption, and countermeasures can be used to reduce or even avoid lost production costs.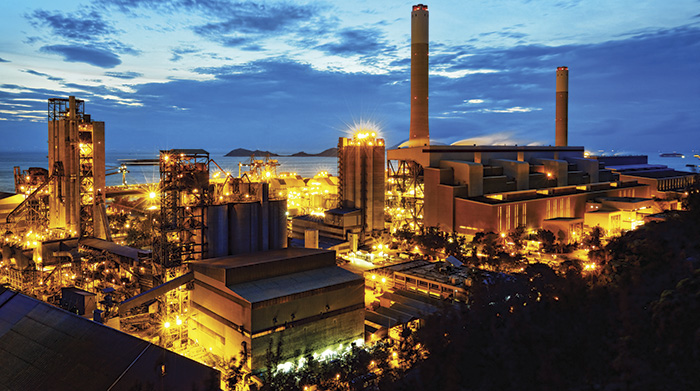