The performance and service life of a centrifugal pump is affected by factors ranging from the system’s design and critical components to the many operating conditions encountered in an application. But regardless of how closely a pump may appear to conform to application requirements at the outset, unanticipated problems can eventually develop and equipment downtime may follow. In these cases, operators should consider whether upgrades to components—rather than a simple fix—make sense. Appropriate upgrades to existing pumps can enhance reliability and improve productivity. Rolling bearings represent one example of how next-generation design, engineering and materials can optimize pumps in service. In general, bearings for rotating machinery support shaft loads, reduce friction with rolling elements, and provide shaft location and system rigidity. For centrifugal pumps, bearings support hydraulic loads imposed on the impeller and shaft, as well as loads created by couplings and drive systems. Bearings also keep shaft axial and radial deflections within acceptable limits for a pump’s impeller and shaft seal.
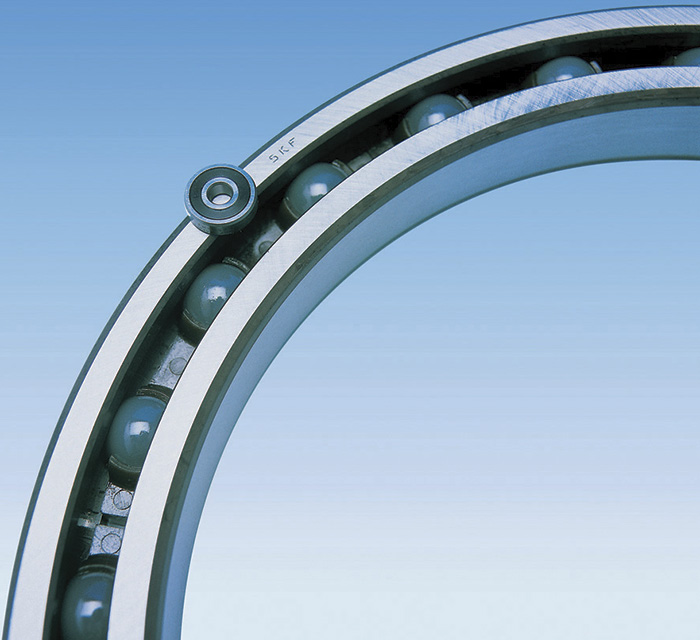
- the use of ceramic material for rolling elements and super-tough steel for bearing rings
- specialized wear-resistant coatings
- dissimilar opposing contact angles for rolling elements to withstand potential damage resulting from minimal axial loads
- optimized energy-efficient bearing designs
Making Material Changes
Bearings in especially tough pump applications, such as oil and gas and hydrocarbon process industries, typically must accommodate contaminated and corrosive environments, inadequate lubrication conditions, high and low loads, and high or cryogenic temperatures. At the same time, they must provide a high degree of service, availability and safety. These demands can test the limits of conventional all-steel bearings. As an upgrade, hybrid bearings that integrate rolling elements made of bearing-grade silicon nitride can substantially improve reliability and robustness. Such bearings are dimensionally interchangeable with similarly sized all-steel bearings, eliminating the need to reconfigure or otherwise alter pump equipment. An engineered ceramic material, bearing-grade silicon nitride offers a uniform and clean microstructure that is extremely hard and 40 percent less dense than bearing steel. As a result, rolling elements weigh less and exhibit lower inertia, which reduces stress on a bearing’s cage during rapid starts and stops and significantly lowers friction at high speeds. Lower friction translates to cooler running and longer lubricant service life. In addition, silicon nitride demonstrates a higher modulus of elasticity than steel, which promotes increased bearing stiffness and longer bearing service life in contaminated environments. The lower thermal expansion for silicon nitride rolling elements allows for more accurate preload control and less likelihood of excessive preloading when temperature gradients exist within the bearings. As an alternative to compensate for extreme conditions, hybrid bearings are available with high-performance stainless steel rings instead of rings made from conventional steel to promote superior corrosion resistance and to compensate for high temperatures. Hybrid bearings also can improve bearing reliability and service life in other ways. For example, smearing may result in bearings that face insufficient or improper lubrication conditions, high speeds and light loads, and/or sudden starts and stops. Smearing is surface damage to a bearing that results from sliding between the all-steel rolling elements and rings. Smearing will not occur between silicon nitride and steel, enabling hybrid bearings to last longer in applications that have severe dynamic or improper lubrication conditions.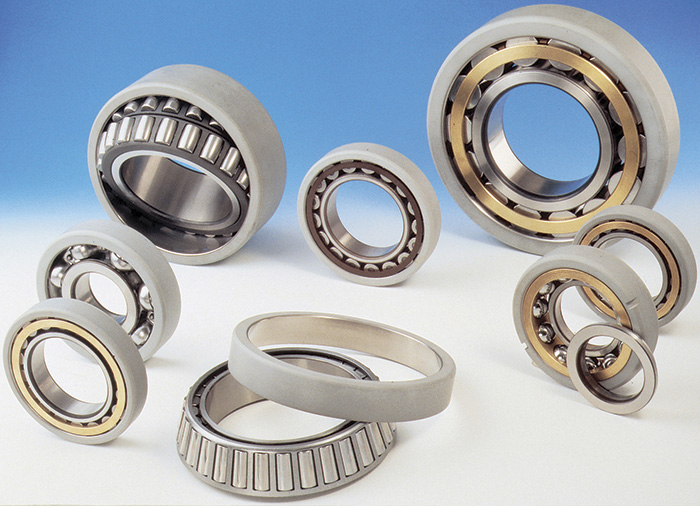