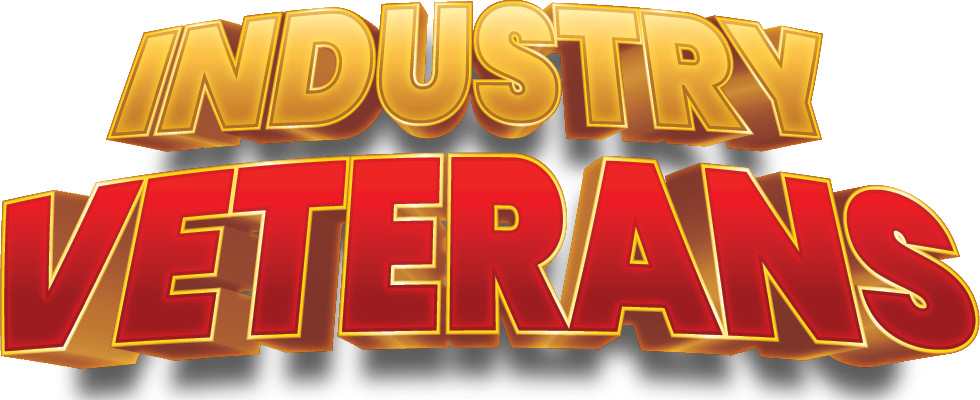
“Believe that you can achieve anything if you put your mind to it. Don’t expect any special treatment; everyone has a job to do. Be curious about the things which are not specifically in your control. This will help you learn and gain a greater understanding of the environment around you.” Kathryn Poke, 45, received this advice from her first manager when she began her career in the industry and has the track record to prove she learned from it.
Poke started her career as an apprentice maintenance electrician at Tenmat and worked her way up to maintenance electrician during her four years with the company. From there, she moved over to the Armstrong Fluid Technology family, where she has had a remarkable almost 24-year journey. She began as an internal service engineer, and from there, she has worked her way up from design engineer, product marketing engineer, product manager, new product development project manager and engineering director to her current role as general manager for Europe, the Middle East and Africa (EMEA) for RMI Pressure Systems.
When asked what the hardest part about her job has been, Poke said, “Being a female in a male-dominated world has been very challenging at times. The industry has made massive strides in being more inclusive and with encouraging females to be part of STEM activities.” She is also a council member of the Association of British Mining Equipment Companies and has advocated for advancements in STEM education, an effort to inspire the next generation, especially young women, to pursue careers in engineering.
Outside of work, Poke has two sons who keep her very busy between football, rugby and showjumping.
How have things changed over the course of your career, in terms of technology and/or regulations?
When I started, variable speed technology was just being introduced. The Ecodesign Directive has driven the industry to be
more energy efficient conscious over the past 10 years, really driving change in motor efficiency and centrifugal pump hydraulic efficiency.
What do you think younger engineers or operators need to learn to be prepared to take on these roles as others retire?
Some roles need you to have the foundation and understanding before progressing. They will need to be prepared to be hands on to get the best understanding of their trade and the industry before trying to climb the ladder. The hands-on trades are as important as the back office roles.
What has working in the industry meant to you?
Being an engineer, it’s been fascinating to see how technology has enabled the pump design to evolve, which has also allowed the system design to be enhanced. Being part of legislative changes has helped me to appreciate how much energy was being wasted by poor pump and system design and gives a small sense of achievement that we are making a real difference.
What kind of training helped you the most over your career?
Internal training is always very helpful. The experience which is found within the business is invaluable for helping bring newer employees up to speed with products and the industry.
What, in your opinion, are the biggest challenges that the industry is facing?
Young engineers coming into the industry is a big challenge. There seems to be a lack of interest of people wanting to take on manual roles and this is a concern as we will run out of electricians, plumbers, pipe fitters, welders and service engineers.
What has been the best part about your job?
I have been very lucky to meet many people from within the industry and most have been willing to share their knowledge and support.