In my last article, “Understanding Available Technology Is Necessary for Successful Vibration Monitoring” (Pumps & Systems, July 2016, read it here), I might have left you hanging. Yes, there is a cost benefit to starting with an analog-based vibration monitoring program, but what do you lose when a digital device has the potential to do more? A digital vibration analyzer that provides visual indication of both time domain (alternating-current [AC] signal) and frequency domain (spectrum of contributing frequencies) is a valuable tool for any facility. If you have a technician who can actually use the device to its full capability, then you have a winning combination. Without an analyzer or a competent technician, troubleshooting vibration problems can be difficult. The sales team often insists that you need the best, most advanced spectrum analyzer to monitor and troubleshoot—but is that true? Based on experience, I know that if I go into a facility with no knowledge of previous work and collect simple analog low-frequency vibration data (filter out root mean square [RMS] value), I typically find 15 to 20 percent of similar equipment types on the high side of an established normal vibration level. Of that 15 to 20 percent, up to 5 percent of that equipment has serious issues. If I were to supplement the low-frequency data collected with a round of high-frequency data, I would typically find less than 5 percent of similar equipment types with indications of potential bearing issues. The more serious vibration issues—those that result in shutdown—are usually caused by design misapplication or installation errors. These issues are hard to troubleshoot and even harder to repair. Once identified, however, they generally require a one-time fix.
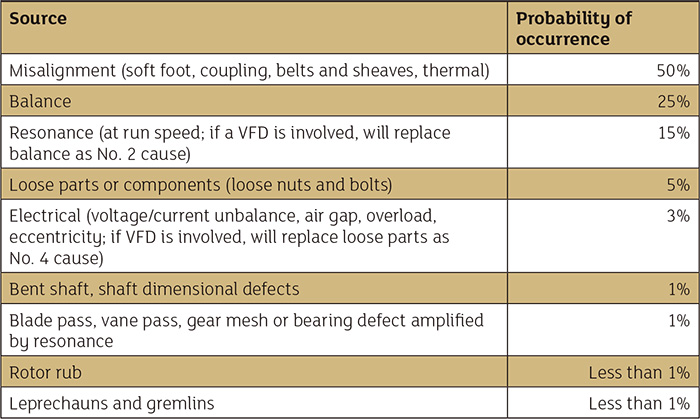
Real-World Troubleshooting
To apply the above statistics, consider the following example. If I had 60 small-frame (American National Standards Institute [ANSI] frame) pumps, all between 60 and 100 horsepower (hp), and 20 percent exhibit higher than normal values (alarm status), then I have 12 pumps on my watch list. Five percent of those pumps, or one pump, would exhibit vibration readings that would warrant a shutdown status. Plus, I would have two additional pumps that indicate a potential bearing issue. Of the two pumps with potential bearing issues, one or both pumps likely would be in the group of 12 watch-list pumps. For this discussion, we will assume that there are two additional pumps that need attention. That means I have one pump out of 60 that requires immediate attention and 13 that should be placed on a watch list. Of the 13, two have a bearing issue and 11 have another issue. Do I need to spend money on a spectrum analyzer to troubleshoot my one shutdown pump? Probably not. Between the cost of the analyzer and the training to use it, I could buy and install a new pump, maybe even two. Keep in mind that the vibration issue on my one shutdown pump is probably a one-time fix.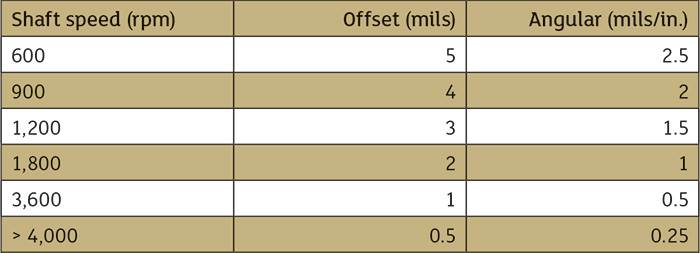