Q. How can we determine the proper size for the intake sump to accommodate several vertical turbine pumps taking input from a river? A. The basic design requirements include adequate depth of flow to limit velocities in the pump bays, reduction of the potential formulation of surface vortices and adequate pump bay width to limit the maximum pump approach velocities. The pump bay width should be narrow and long enough to channel uniform flow toward the pumps. The minimum submergence (S) required to prevent strong air core vortices is based in part on the Froude number—a dimensionless flow parameter with consistent units—defined as:\ FD = V/(gD)0.5 Where: FD = Froude number (dimensionless) V = Velocity at suction inlet equals the flow per unit area, based on D D = Outside diameter of bell or pipe inlet g = Gravitational acceleration The minimum S with units consistent with the outside diameter of the bell or pipe inlet can be calculated using the formula: S = D(1+2.3FD) Bell velocity varies among pump types and manufacturers. However, variations in bell inlet velocity are secondary in maintaining acceleration of flow and converging streamlines into the pump bell. The effectiveness of the recommended pump bay dimensions depends on the characteristics of the flow approaching the structure and the geometry of hydraulic boundaries in the immediate vicinity of the structure. See ANSI/HI 9.8 Intake Design for Rotodynamic Pumps for a basic recommended layout of rectangular sumps. Q. What types of pump losses can be expected with the increase of liquid viscosity in a rotodynamic pump? A. When the viscosity of the pumped liquid increases, the Reynolds number decreases, causing friction factors in the hydraulic passages of the pump to increase just like flow through a pipe. Two examples of losses that can be anticipated are mechanical and hydraulic losses. Mechanical losses are essentially independent of the viscosity of the liquid being pumped. Hydraulic losses—similar to pipe friction losses—occur at the inlet, in the impeller, in the volute or diffuser, and in the discharge of a pump. In basic rotodynamic pump theory, the useful head is the difference of the impeller theoretical head minus the hydraulic losses. Viscosity does not generally influence the flow deflection or slip factor of the impeller. As a result, the theoretical head is not affected. Head reduction due to viscous flow is primarily a function of the hydraulic viscous flow losses. These hydraulic losses consist of friction losses, which are a function of the Reynolds number (pump size, rotor speed and viscosity effects), surface roughness of the hydraulic passageways, and mixing losses caused by the exchange of flow momentum due to non-uniform velocity distributions. Such non-uniformities or mixing losses are caused by the action of work transfer from the blades, decelerations of the liquid, angle of incidence between liquid flow and blades, and local flow separations. For more information on the influence of a liquid's properties in a pump, see ANSI/HI 9.6.7 Effects of Liquid Viscosity on Rotodynamic Pumps. Q. What key factors affect the design life and reliability of pumping equipment? A. For pumping equipment to perform a long-term task, the design must be suitable for the intended task. The equipment assembly also must be operated and maintained within the design and operating duty condition limits. Most reliability shortfalls are caused by operation outside the design limits or abnormal operating conditions.
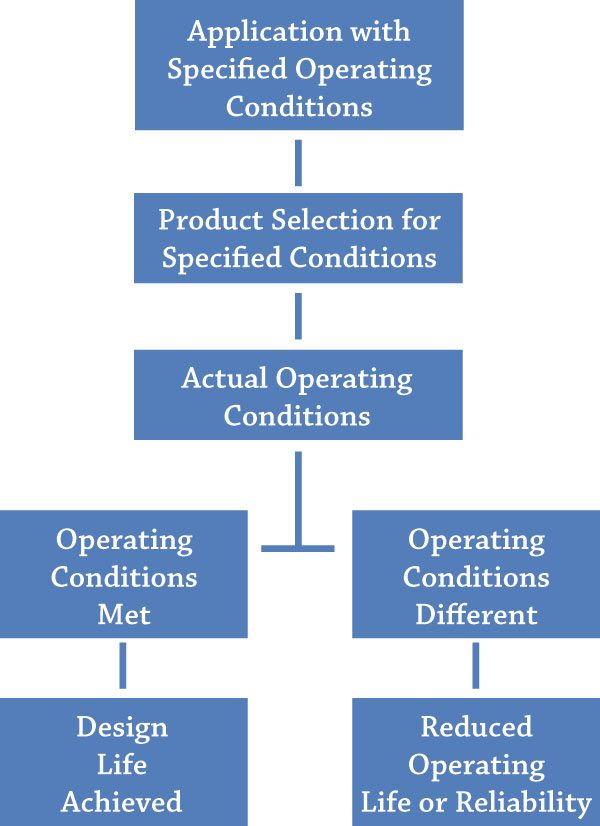