A flame retardant manufacturer incorporated frequency converters to control its cooling water pumps.
02/16/2016
German company ICL-IP Bitterfeld GmbH has been producing phosphorus-based flame retardant since 1997. Its plant in Bitterfeld-Wolfen employs about 80 people. Many of the steps in the production process—from the phosphorus and chlorine starting materials to the final products (phosphate ester)—involve exothermic reactions. Much of the released heat is led away in water-cooled heat exchangers. A centralized cooling tower runs almost continuously—about 8,250 hours per year—to provide the required cooling water. Water temperature varies seasonally from 19 to 25 degrees C. The flow rate can be as high as 1,100 cubic meters per hour (m3/h), resulting in a cooling capacity of up to 6 megawatts (MW).
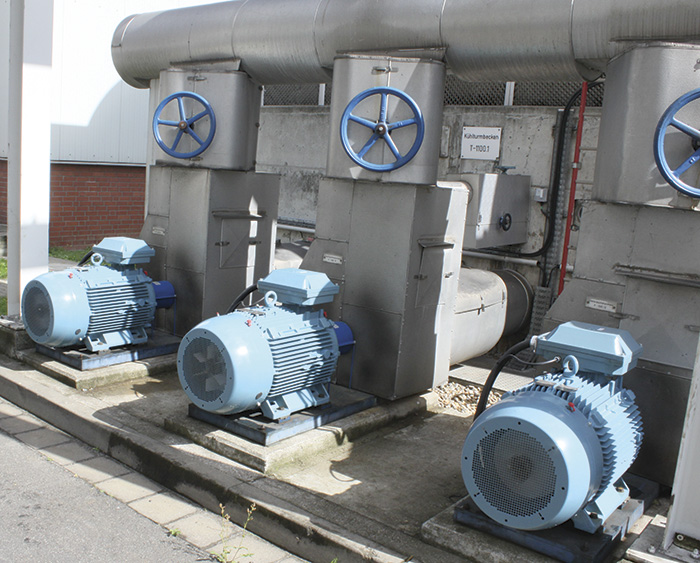
Energy Efficiency a Core Concern
A 2014 company-wide program to improve energy efficiency systematically identified additional weak points in how energy is used. For the cooling water pumps, new motors and speed control with frequency converters produced significant savings. With this foundation, Production Manager Dr. Jücrgen K. Seifert developed a technical concept for controlling the three pumps in a way that adapts to the cooling water's continually changing needs while eliminating the inefficient method of using throttle flaps. Before implementation, multiple simulations indicated a high potential for savings with a projected return on investment (ROI) of two years.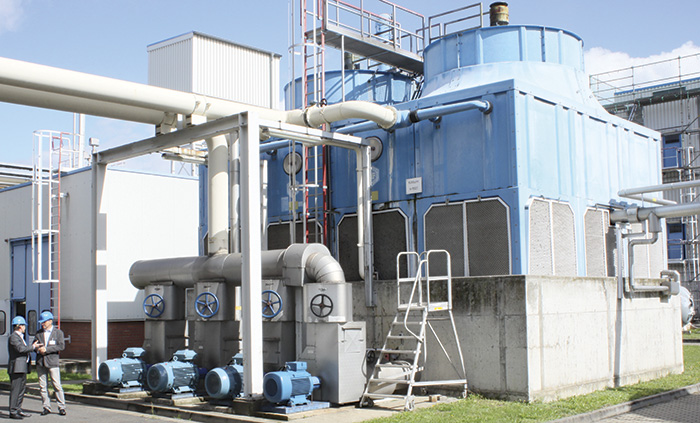
Frequency Converters Replace Manual Intervention
In the past, the pumps ran at a constant 1,450 liters per minute (l/min). They were regulated with throttle flaps located at the pump outlet on the discharge side. This configuration brought the pumps into the performance curve range where the drive motors were not overloaded (counterpressure at the consumer side is only about 3.5 bar at full hydraulic load). While this type of control can destroy energy, it is usually unavoidable in situations that consist of a fixed-speed pump and a system with low counterpressure. In this case, the throttle flaps helped hold the pressure at a constant 4.8 bar at the pump outlet, regardless of the actual need for coolant. This achieved a constant power consumption at the motors of 68 to 75 kW, at which point each pump was expected to stabilize near its rated capacity of 360 m3/h. As an initial energy-saving measure after the analysis, one or two pumps were switched off during partial-load operations, such as when consumers (heat exchangers) were turned off. But this approach is difficult because the remaining pumps must be monitored continuously to make sure they do not become overloaded. If loads suddenly change, engineers must be prepared to undertake rapid manual interventions. Frequency converters help solve this problem by replacing manual, inconsistent on/off control with a continuous, intelligent adaptation of pump speeds to the actual need for cooling water. As a result, manual interventions are no longer needed. The pumps are synchronized and run continuously in their optimal range, and pump discharge pressure remains constant. The cascade feature automatically switches pumps on and off as requirements change on the consumer side.Smooth Switch
The facility completed the practical execution of the upgrade in close contact with the pump supplier. The manufacturer has long developed intelligent controllers for cooling water pumps in systems where the need for cooling water frequently changes, whether due to fluctuating cooling water temperature or because of varying loads imposed by the process. Because of this experience, the manufacturer was able to quickly provide a suitable solution for the plant. "Only rarely have I experienced such a smooth project execution," Dr. Seifert said about the experience at the plant. "They immediately understood our concept and executed it with precision."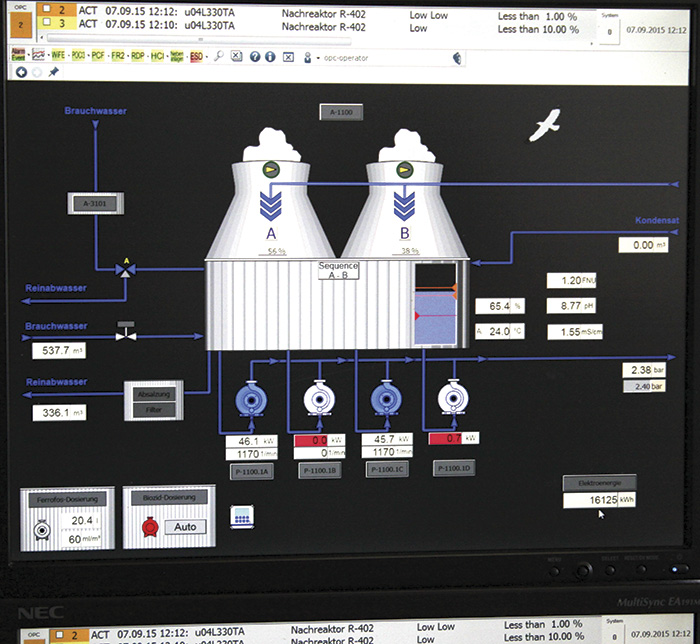
Potential for Savings
In many cases, energy consumption in such systems plays only a secondary role and is often neglected. Even at the Bitterfeld plant, energy costs make up a comparatively small proportion of overall production costs. But the new controller reduced power requirements for cooling by 50 to 60 percent, or about 1,000 megawatt-hours (MWh) yearly. The investment paid for itself within one year, faster than predicted by the simulations. Even when all three pumps are running under full load, energy requirements drop from 75 to 37 kW per pump. The energy required to run the cooling tower now accounts for a much smaller proportion of the total energy consumption of the plant. All of the money that is saved flows directly into operating results. The Bitterfeld plant demonstrates the potential for savings that can be found in industrial systems with oversized pumps that were dimensioned and installed years ago with excess reserves. In this case, the energy savings totaled more than 80 percent. As prices for frequency converters drop and the technology becomes more accessible, the use of intelligent controllers makes more sense even for higher-output systems. The question of "How reliable are the electronics, and what happens if a frequency converter fails?" is less of an issue. The technology is mature, and, because of optimized control, two of the three pumps at the Bitterfeld plant can cover a large portion of the plant's needs if a frequency converter were to fail.CASE STUDY AT A GLANCE
Challenge- Significantly reduce energy costs
- Convert the entire cooling system within one week
- Flexible pump speed with constant discharge pressure to all consumers
- Elimination of valves; no change to cooling reliability at full load, even if one pump fails
- Use frequency converters to control the pumps for precise adaptation of capacities to current need for coolant
- Optimization of impellers in the centrifugal pumps
- Energy savings of more than 80 percent
- Several thousand euros saved after just one month
- Savings in operation of the cooling tower
- Efficiency of all pumps increased to 85.3 percent