Contemporary pump engineering principles help achieve optimum efficiencies while cooling a city using renewable energy sources.
10/22/2013
In Masdar City—a celebrated, centrally planned community in Abu Dhabi, UAE—temperatures recently reached a record of more than 51 C. The city is being built by the Abu Dhabi Future Energy Company with additional funding from the Abu Dhabi government. A long-term, truly sustainable view of capital investment is clear. At the moment, 100 percent of the electrical demand is provided by photovoltaic power generation. As the city population grows and demand for energy increases, it is expected that the existing 10-megawatt (MW) solar installation will provide 20 percent of the city’s electricity, with the remaining 80 percent coming from alternate sustainable sources.
Sustainable Investments
City planners began the project by focusing on minimizing the total energy requirements through passive means, carefully managing the orientation and form of buildings for maximum efficiency (see Image 1). As a secondary step, planners looked for advanced solutions in building performance optimization and other active controls.
Sensorless Demand-Based Control
A pump company’s design-envelope technology plant’s packages and controls use the Equal Marginal Performance Principle (EMPP) established several years ago as a way to realize efficiency improvements of 25 to 50 percent more than equivalent conventional set-point methods for operating HVAC systems.1 The EMPP states that the energy performance of any system that operates with multiple modulating components is optimized when the marginal system output, per unit energy input, is the same for all individual components in the system. The embedded control technology manages equipment according to optimized, system-wide power relationships, rather than meeting intermediate temperature or pressure set-points. Design envelope technology also offers sensorless demand-based control, which reduces the costs for equipment purchase, installation and commissioning. On the more than 30 pumps in the university buildings at Masdar City, no external sensors are installed. The cooling systems rely on prefabricated, integrated pump stations called design envelope intelligent fluid management systems (IFMS). IFMS stations consist of a number of precisely matched, vertical in-line pumps with integrated controls, plus an intelligent pump control unit. The control unit calculates the head and flow requirements in real time, enabling pump speed adjustments based on the immediate demand for cooling.Efficiency Envelope
Design envelope technology provides very high efficiency levels across a wide design/performance range, regardless of the operating point. This ensures that pumping systems consume as little energy as possible. It also allows installations to exceed American Society of Heating, Refrigerating and Air-Conditioning Engineers (ASHRAE) 90.1 guidelines for 2010, mandating 70 percent energy savings at 50 percent of peak load, with resulting carbon emissions well below the current legal requirements.2 It lets owners buy a small car rather than a big truck, while enjoying both the performance of the truck and the energy and cost advantages of the small car.A Wide Range of High Efficiency Operation
The choice of intelligent, integrated pump stations also optimizes energy efficient pumping capabilities over a wide operational range. This allows building designers to future proof HVAC systems by designing in the flexibility to accommodate additional cooling load. This operating flexibility, combined with high efficiency across the performance range, can also reduce iterations of pump selection, control risk, and protect capital and operating budgets. Changes to specifications are common during the planning phase of a major project. These changes may involve consultants and other engineers in costly redesigns, which points to another part of the value of design envelope technology. The broader range of operating efficiency means that a given selection of design envelope pumps can accommodate changes in cooling load. In many instances, although building specifications might change, redesign or re-selection of the design envelope pumps will not be required. Even after installation, the wider performance capabilities of integrated, design envelope technology can accommodate variations in cooling requirements. New or revised requirements may stem from increased occupant density, changes to building use or modifications in the shade conditions because of changes in the building’s surroundings—such as the construction of new buildings adjacent to the existing site. This operating flexibility is significant on large projects such as Masdar City, which is expected to require an additional 50,000 tons of district cooling during the next five years. For the city’s project managers, the broader operating range of the pump systems will provide greater adaptability without costly HVAC refurbishment, while ensuring continued optimization of pump efficiency. The imperatives that have driven the industry in recent years are in tune with the requirements of the city and its leadership goals. Although some of the systems used were the first of their kind in the region, the installation at Masdar City has led to three similar projects in Qatar and another in Abu Dhabi.Pump Stations Pre-Built Off-Site
Each pump package for Masdar was designed, built and tested off-site at a U.K. plant. Manufacturing of systems off-site ensures energy efficiency performance, reduces installation costs and eliminates project risks during installation. Where many large installations of cooling systems experience delays related to the coordination of labor and the sourcing of components, off-site manufacturing removes all these issues from the project plan. Project managers can stay abreast of the assembly process but do not have to worry about sourcing and labor issues. The integrated cooling systems for Masdar City were delivered to the site fully assembled and ready to be lifted into place by a crane.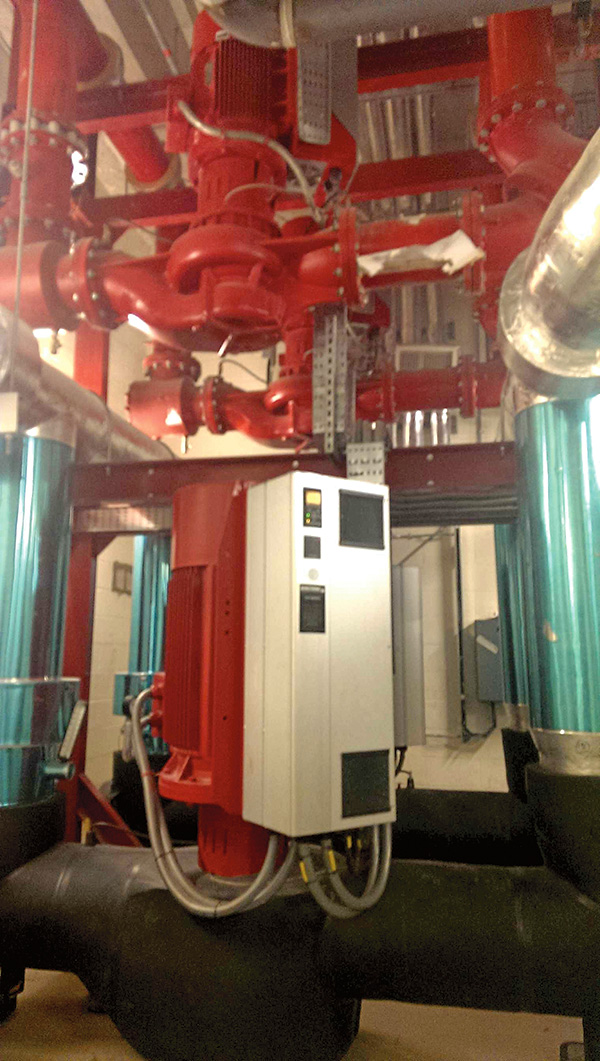
Suspended Vertically
One factor that affected cost efficiency was the way contemporary pumps are installed. In the days of noisy, vibrating equipment, engineers took comfort in mounting pumps squarely and horizontally on a concrete platform on the floor. At Masdar City, the pumps are suspended vertically, sometimes one above another (see Image 2). This saves space in the mechanical room, which leads to reduced capital cost. The cooling efficiencies achieved in one of the world’s hottest places are truly impressive. The integrated chilled water plant will consume 0.55 kilowatts per ton (kW/ton) (6.4 coefficient of performance—COP) or better on an annual average basis, which significantly exceeds today’s best-in-class levels of 0.75 kW/ton (4.7 COP) for water-cooled systems. Even in the more than 51 C peak heat of summer, the readings are between 0.73 to 0.85 kW/ton for the full plant. Thanks in part to advances in HVAC technology, inside the renewables mecca of the desert, it remains cool.References
- http://www.automatedbuildings.com/news/jul05/interviews/hartman.htm
- ASHRAE Journal, (Vol. 47, No. 7, July 2005). American Society of Heating, Refrigerating and Air-Conditioning Engineers, Inc., (www.ashrae.org).