Anthropologists have determined that the tarlike petroleum byproduct known as bitumen, defined as “a black, viscous mixture of hydrocarbons,” was first used as an engineering material sometime around 3000 B.C. Today, more than 5,000 years later, the use of what is now called asphalt, or “a mixture of dark, bituminous pitch with sand or gravel,” remains a foundational element in many of our societies’ most important industrial operations, from road construction to roofing to waterproofing. While bitumen and asphalt have been construction mainstays for five millennia, so have the challenges that must be overcome in their handling. Pumps play a prominent role throughout asphalt’s production and supply chains, meaning that identifying and implementing a pumping technology that is able to meet the challenges of handling asphalt must be a top-of-mind consideration for the operator. To that end, this article will illustrate how internal gear pump technology can be the ideal choice for the most challenging bitumen- and asphalt-handling applications. Since pumping systems are ever-present in almost all industrial-manufacturing facilities and are crucial to the operation of many production applications across a wide array of industries, they are also ripe for operational improvements that can improve reliability and decrease equipment and operating costs.
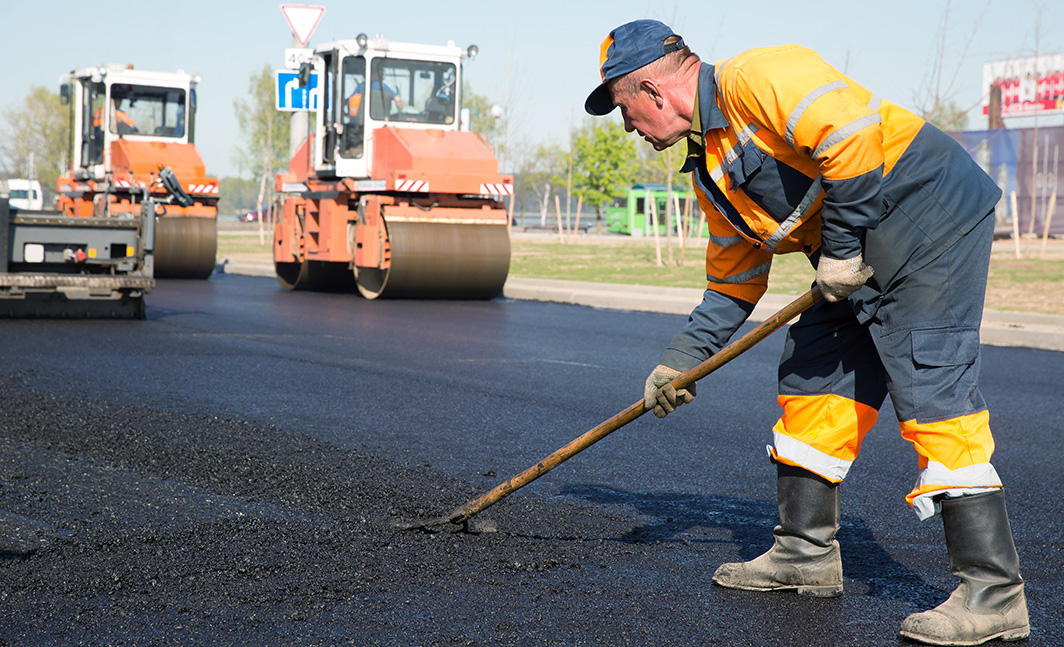
The Challenge
Asphalt pumps are required all along asphalt’s production and supply chains. They can be found at refineries where raw asphaltic products are produced, terminals where various asphaltic products are stored, hot-mix plants where paving products are produced and roofing material manufacturing plants where shingles and other roofing materials are manufactured. Specially configured asphalt pumps are at the heart of these and other systems that rely on asphaltic products as their base for production. The main challenge in these operations is the most obvious one: as asphalt changes temperature, it can range from a solid to a liquid with a wide variety of fluid characteristics depending on the chemical makeup, which makes it extremely difficult to pump with standard pumping technology. To offer safe and reliable operation, a pump designed for asphalt service must follow these special considerations. Pump Externals. A pump’s external metal parts are defined as those that come into contact with the pumped medium on the inside while being exposed to ambient conditions on the outside. Pumps designed for asphalt applications must be able to insulate the asphalt from the outside ambient conditions. An effective heating jacket that maximizes the surface area between the heat-transfer media (steam or hot oil) and the pumped medium (asphaltic products) is critical to reliable performance. Pump Internals. Due to the wide range of temperatures and viscosities of asphalt products, special consideration always needs to be taken when selecting the proper internal clearances. Oversight can lead to bushing, gear or shaft failure. Furthermore, internal components can be placed under significant stress when pumping asphalt products. Viscosity changes due to temperature swings can cause the asphalt product to solidify in the pump or piping system, leading to potential rotor gear-tooth failure. Sealing. Shaft sealing is by far one of the most significant challenges to overcome in an asphalt application, in particular when a leak-free condition is desired. Packing is the most widely used shaft sealing solution in all asphalt applications due to its reliability, simplicity and ability to operate in all viscosity and temperature ranges. However, packing must leak in order to operate reliably for long periods of time. In clean asphalt applications where there are little to no solids and leakage is not acceptable, cartridge triple-lip seals or mechanical seals can be used. In filled asphalt applications where solids are present and leakage is not acceptable, mechanical seals with hard faces can be used. Whenever using cartridge triple-lip seals or cartridge mechanical seals, it is always recommended to use a quench in order to heat the seal, keep air out and avoid coking of the asphalt near the seal faces. In some instances, sealless mag drive pumps can be used for a leak-free asphalt operation as long as strict precautions are taken during the startup. With the wide range of asphalt products in the market, all with different fluid characteristics, special considerations also need to be taken from application to application. Often a single plant operation can feature clean asphalt with moderate viscosity in one process, and a viscous, filled asphalt with heavy abrasives in another process. Emulsified asphalt is made up of a mixture of asphalt cement, an emulsifying agent (surfactant) and water. It is sensitive to shearing, which requires the pump to be built with extra internal clearances, operate with a reduced pump speed and in some cases be fitted with special idler-bushing lubrication methods. Sometimes referred to as coating asphalt, filled asphalts can have limestone or other abrasive particle concentrations of 60 to 70 percent, making them heavily abrasive. Pumps in these applications generally require hardened cast-iron or tungsten-carbide bushing sets and hardened case, head, rotor gear and idler gear. Like all pumps used in abrasive applications, the pump speed should be reduced significantly to maximize the life of its components.The Solution
The ultimate—and necessary—solution for pumping asphalt is to use a pump that features a heating jacket, robust gear materials, a wide range of internal component material options and flexible sealing configurations.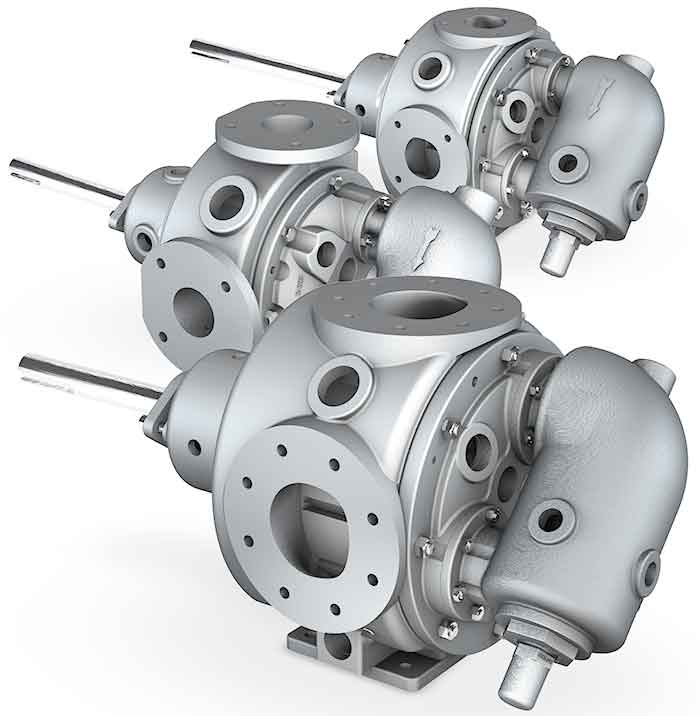