A fact of life is that equipment operators spend more time with pumps than mechanics do. Leveraging this familiarity with equipment, operator-driven reliability (ODR) programs focus on maximizing plant reliability by enhancing the techniques operators use to monitor the equipment for which they are responsible. ODR is not a new concept, and many companies around the world have deployed ODR programs to various levels of success. One benefit of ODR is the ability to improve seal mean time between failures (MTBF). The first step toward improved seal MTBF through ODR is understanding why a seal fails. It is often for reasons other than reaching the end of its life span, such as lubrication problems, vibration or installation errors. During their routine rounds, operators are often asked to document only if the seal is leaking and if the seal pot level is acceptable. While this may seem reasonable, plant management may not be getting value from the tasks they have asked the operator to perform. For example, the operator can log that the seal is leaking, but does he or she know enough about the different seal flush plans used in their area to identify where the leak is coming from? Is the leak coming from between the shaft and the seal sleeve, between the seal sleeve and the seal gland, the seal gland and the head, or from a leaking piece of tubing, piping or union? Depending on the source, the operator may have an opportunity to mitigate the leak before creating a work order that could lead to costly misdirected pump maintenance. If the operator only has the option to answer yes or no to whether the seal pot level is in the acceptable range, plant management can miss critical information. In many cases, knowing if the seal pot level is low, normal or high could be a sign of a primary seal face leak, a secondary seal face leak or even a seal flush cooler leak, depending on the specific seal flush plan. Some equipment—such as coolers, purges, vent lines, quenches, reservoirs and collection vessels—is often ignored during inspection. To ensure that operators are monitoring the seal flush system properly, plant management should optimize inspection techniques, provide training on the new techniques with visual aides both in the control room and in the field, and provide operators with the right tools to properly execute the inspections.
Suggested Tasks for Operators to Improve Seal MTBF
Because some leaks can be mitigated without maintenance, operators should routinely monitor seals for leakage and identify the source of the leaks.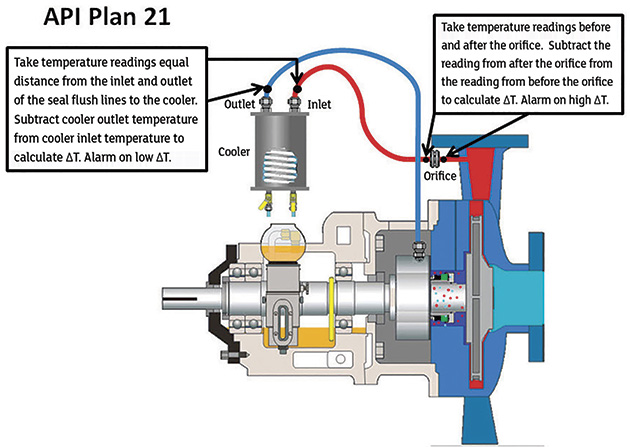
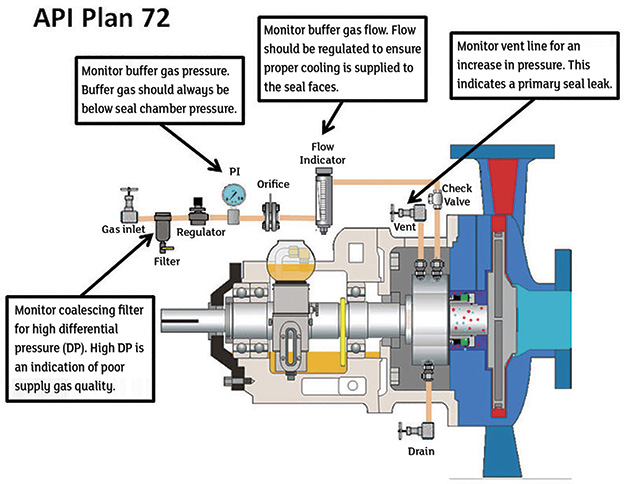