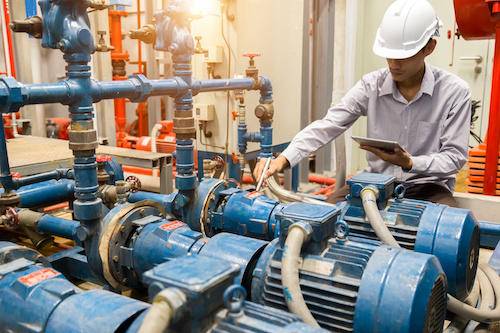
Traditionally, pump vibration and surface temperature have been the leading methods for determining the health and condition of pumps and rotating equipment in the industrial space. However, these signals of oncoming pump failure often present themselves close to the end of life for most pumps.
Fortunately, new types of predictive maintenance through internet of things (IoT) remote monitoring present the opportunity for early detection of future problems that can extend pump life span and minimize downtime and overall maintenance costs. It can also do so cost-effectively since a single pump loss can often pay for the IoT system many times over. A study done by a professional services network found that predictive maintenance may save companies $630 billion by 2025, with most of the cost savings coming from a reduction in unscheduled downtime.
Without the early detection monitoring provided to maintenance teams by IoT, companies can easily overlook early indicators of equipment changes. As such, complete monitoring of pumps and systems identifies issues early within the pump, limiting downtime and extensive costs from labor and replacement parts. Here is how to assess potential pump failure areas with an IoT-driven preventive maintenance strategy.
Bearings & Seals Present Risk for Pump Failure
The leading causes of pump failures and damage often occur within one of two component pieces: seals and bearings. Seals are often the first pump component to fail. This regularly happens when pressure changes affect the seal chamber pressure and temperature and, ultimately, the seal.
The second most common components to fail in pumps are the bearings. Bearing failures can arise because of corrosion from seal leakage, equipment unbalance, shaft misalignment and even a damaged impeller. However, according to a report by a Swiss bearing manufacturer, 80% of bearing failures are due to improper lubrication, which causes overheating.
Bearing failure demands immediate attention because it can cost as much as $25,000 to $50,000 per hour in lost productivity, unplanned outages and downtime. However, because seals and bearings are the leading components to fail, users can look at the leading failure indicators. In the mechanical seal, a pressure or temperature change would be a leading indicator of process changes that could lead to failure.
Users can use IoT to look at the pressure and temperature changes in the seal. When alerted to spikes and increases in trends, maintenance can be scheduled to prevent failures. For bearings, vibration is a leading indicator of bearing wear. That means users can also use IoT to constantly monitor the vibration of the bearings to determine when it is time to perform a change of the bearings before a catastrophic failure.
Causes of Pump Failures & Damage
Vibration monitoring is an effective way to detect and prevent premature and even catastrophic equipment failure. In addition to bearing wear, vibration often indicates faults such as imbalance, misalignment and looseness—all early warning signs of impending failure.
The sources of vibration in pumps are plentiful. However, the most typical causes include bent shafts, unbalances, misalignments, reaction forces and contact between components. If left unchecked, these occurrences can negatively impact the reliability and operation of rotating equipment.
But when looking at the bigger picture and analyzing why pumps fail, it is imperative to go beyond monitoring pump vibration and instead take a broader look at each component. This is because pump vibration and surface temperature are not always the initial signs of pump failure. For example, changes in pressure, fluid characteristics, rotation speed and direction, suction clogs, worn-out internal wet side components can cause changes in pump pressure—which ultimately translate to vibration.
How IoT Solves Problems
Implementing integrated IoT sensors to measure and predict changes within pump components is integral to preserving the life of pump systems and minimizing downtime costs. As such, early detection is a leading preventative measure for determining pump risk.
Condition-based monitoring maintenance programs with IoT deployed at the center are well-suited to analyze vibration and pressure, among other components, for manufacturing teams to prepare for any unplanned downtime due to system failure.
Unfortunately, today’s industry primarily operates on a simple model: if the asset is broken, then fix it; otherwise, check it periodically. This traditional practice is inefficient. Alternatively, using IoT to predict failures before they occur, while understanding what is needed to prevent a repeat failure, is the better approach.
Furthermore, modern and flexible IoT systems complement legacy systems by identifying failure modes that were never designed to be monitored. IoT is designed to alert maintenance teams to failures that may be buried within the equipment or inadvertently hidden by the customer or independent service representative. Predicting asset behavior requires knowledge of the equipment, the application and IoT technology.
In these types of seal scenarios, monitoring pressure, temperature and vibration can understand the pump’s condition by catching abnormal conditions to prevent failures and decrease downtime.
Monitoring Prevents Downtime & Damage
Complete monitoring enhances production line safety through independent monitoring of critical equipment, lowering the risk of downtime incidents and reducing maintenance costs. However, unplanned downtime affects every part of the manufacturing process, including productivity, information technology (IT) and customer service.
Early detection and predictive maintenance are integral for efficient production and help mitigate the costly effects of unplanned downtime. To put this into perspective, one study found that in 2008, the average cost of pump repair was $12,000. While unplanned downtime has a severe impact on many industries, the manufacturing industry especially can see some of the most considerable losses. For example, unplanned downtime costs factories between 5% and 20% of their annual productivity and $22,000 per minute in the automotive industry in 2016.
Therefore, manufacturers need to keep pump systems running as efficiently as possible with minimal downtime. Using IoT as part of preventive maintenance strategies with integrated sensors is one of the best ways to obtain preventative measurements for pump issues, regulatory maintenance and downtime events.