The requirements of heating, ventilation and air conditioning (HVAC) and plumbing piping systems can be very different from the process industry. HVAC systems use piping to convey fluids for the transfer of energy between different areas of a building. Plumbing piping brings in fresh water while removing the waste from a building. This energy transfer and water movement must all happen efficiently and quietly without disturbing the people living and working in a building. It can be a challenge for the system designers. The heat transfer fluid (usually water) and fresh water are pumped throughout the building. Pumps vibrate and create noise as they move water. Pumps are also located in a central mechanical room. Architects are notorious for locating these rooms in the worst possible place in a building, usually adjacent to the office of someone important. Even if the equipment room is in a remote location, noise and vibration may be transmitted through the pipes and annoy someone in a different area of the building. These problems can be most infuriating to HVAC or plumbing consulting engineers because when the building is nearly finished and may even be occupied, changes at this point in a project are generally expensive and result in very unhappy owners. The key to effectively minimizing pump noise and vibration is to properly isolate the equipment in the design stage of a project, as shown in Image 1.
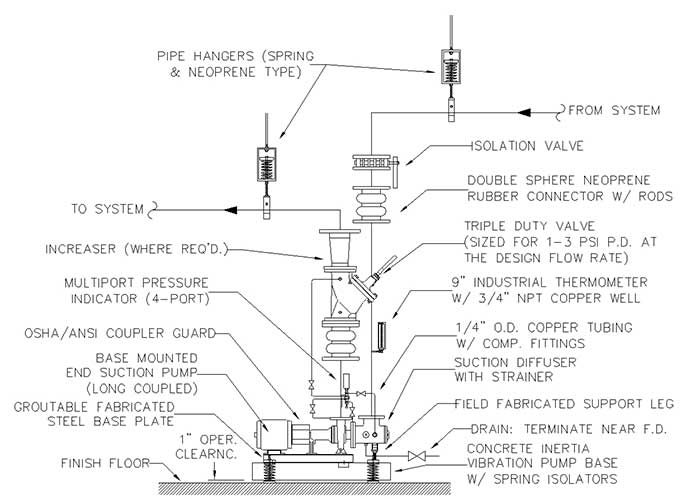
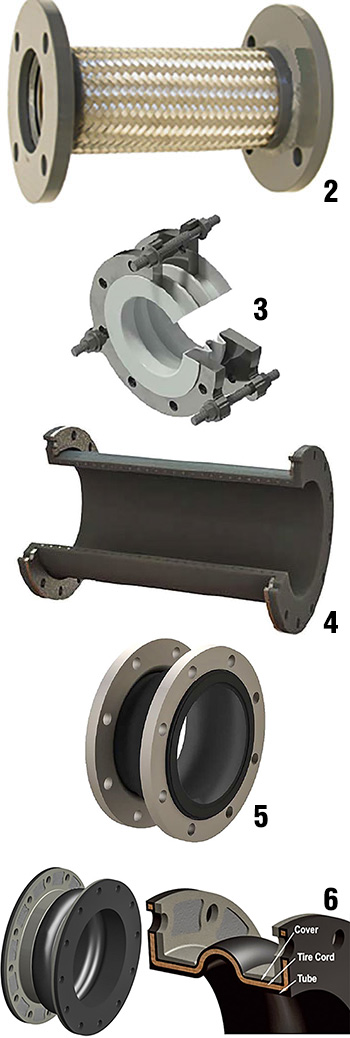
Hose & Braid
Hose-and-braid connectors consist of stainless steel or bronze corrugated hose with stainless or bronze braid (see Image 2). These connectors can have various end fittings (flange, weld, threaded, grooved or a combination) and can handle higher temperatures and pressures. Hose-and-braid connectors do not subject the mating pipe ends to hydrostatic end loads. Stainless or bronze connectors are intended to be a life-of-system product, meaning that no periodic inspection or maintenance is required. These connectors are designed for lateral movement only and cannot handle axial movement unless they are combined into a loop assembly. Also, manufacturers require minimum lengths for effective vibration isolation.PTFE Couplings
PTFE couplings are occasionally used for vibration isolation (see Image 3). PTFE is a fluoropolymer capable of higher temperatures and pressures and can be used with many corrosive fluids that would be unsuitable for metal or other elastomers. These connectors are flanged, with integral control rods to limit the movement.Elastomeric Couplings
Elastomeric couplings are usually flanged, with either spool or spherical-type bodies (see Images 4 through 6). Several types of elastomer compounds are available, with neoprene and ethylene propylene diene monomer (EPDM) the most common material for HVAC or plumbing systems. Standard construction consists of three main layers: the tube, reinforcing plies and cover. Spool-type bodies have full-face flanges with internal wire reinforcement or specially designed reinforcing flanges. Spherical joints have a bead seal and are constructed without additional reinforcement. Control rods are usually installed with this type of connector, and the mating flanges can be subject to considerable pressure thrust loads. Elastomeric couplings are generally not life-of-building products and must be periodically inspected and replaced.Noise Characterization in Building Piping Systems
HVAC and plumbing noise may originate from the large components (chillers, boilers, cooling towers, pumps, air handlers) or any of the smaller components (fans, valves, terminal units, diffusers or grilles). The test results presented will strictly focus on the water moving systems and associated piping. There are no standard piping configurations, so the results will reflect a somewhat arbitrary piping arrangement. Equipment produces sound and vibration in a wide range of frequencies. Examples may include large air handling systems producing low-frequency rumbles (16 to 125 Hertz [Hz]), through fan and pump noise at the middle frequencies (63 to 1,000 Hz). Moving air-generated noise can go up to 8,000 Hz and be perceived as a whistle or hiss. The frequencies of most concern in piping systems are in the middle frequencies from 63 Hz to around 1,000 Hz (see Table 1).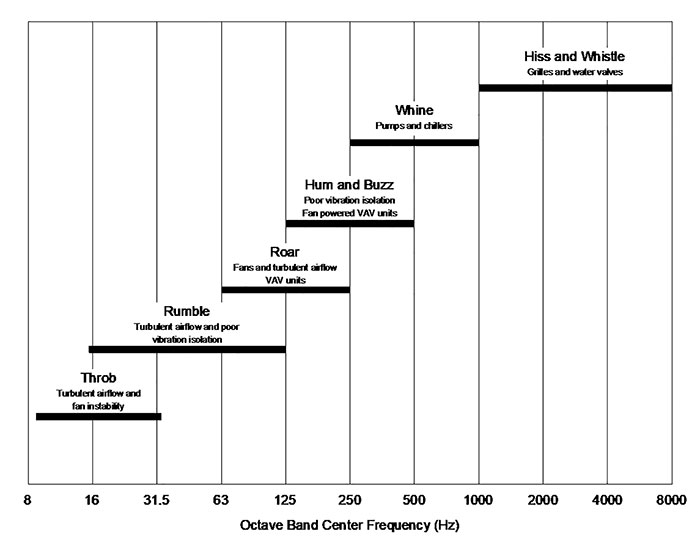
Comparison of Expansion Joint Performance
Transmitted noise and vibration will be affected by several variables, including the characteristics of the connected equipment; the number, type and location of pipe supports; the pipe material, pressure and pipe geometry. It is important to consider the entire pipe assembly as a system, with changes in any one component affecting the noise and vibration characteristics of the entire pipe run. Laboratory and field testing has revealed several useful results that may be applied to most installations. Here is a summary of the test results that FSA member companies have conducted over several years. How is noise and vibration transmitted? Is it through the pipe wall or through the fluid medium? The answer is both, but more through the pipe wall depending on the equipment. Chillers and boilers tend to transmit greater vibration through the pipe walls, while pumps may transmit more through the fluid. Vibration is transmitted through the pipe wall as a bending wave, and through the fluid medium as a pressure wave. All types of flexible couplings provide isolation by decreasing the pipe wall stiffness. The elastomeric connectors further decrease fluid-transmitted vibration by absorbing the pressure variations. Rubber walls can expand circumferentially to accommodate these disturbances; metal connector walls cannot. Be aware that there will be temperature and pressure combinations that only metal connectors can accommodate. Which works better for noise and vibration reduction, metal or rubber? Rubber, but although this result may seem evident, there are applications that still require metal connectors and it is important to quantify the vibration reduction difference between the two materials. Also, although there are several types of rubber, there is not an elastomer that performs better than the others. All elastomers and polymer tested (EPDM or neoprene or PTFE) have similar vibration isolating characteristics for water-filled pipe. All did markedly better than hose-and-braid isolators when tested in a 30-foot pipe assembly with two bends, as shown in Table 2.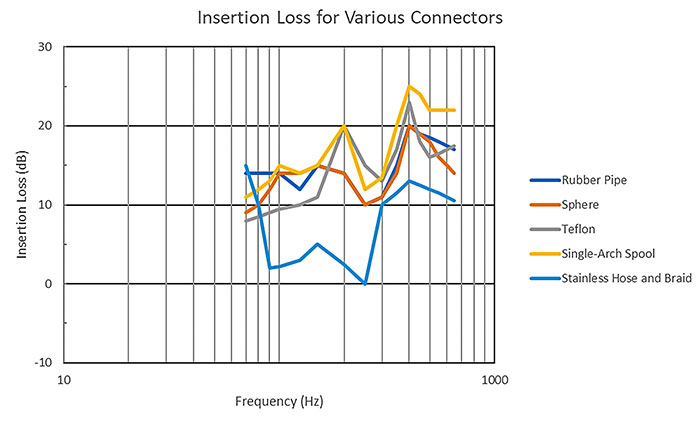
- Flange effects: Flanges and other heavy components like valves and rigid supports reflect pipe wall vibration and form standing waves. They essentially act as nodes in the piping system, making it possible to roughly predict the resonant frequencies of the pipe assembly.
- Pipe support effects: Pipe supports will not affect vibration transmission unless they are very stiff, which would essentially make them part of the building structure. Testing showed that the stiffness must be at least 2,000 pounds per inch. Clevis hangers typically are about this value. Spring hangers are significantly lower and have almost no affect on vibration transmission to the structure.
- Pipe bend effects: Pipe elbows transform pipe wall bending waves into torsional waves, and vice-versa. Tests have shown that flexible connectors perform well in bending wave reduction, but not as well in torsional vibration isolation. Locating any type of connector immediately downstream from an elbow may not be effective in reducing vibration if the waves are torsional.
- Pressure effects: Increasing the pressure of the fluid medium has a small effect, generally increasing the vibration isolation characteristics of the connector. The effects were negligible over 50 psi.
- Control rod effects: A common concern raised by specifying engineers is that the control rods can “short circuit” the vibration isolation of the rubber joint. Tests have shown that the control rods have almost no affect on the vibration isolation characteristics of the connector. Since the flanges act as nodes in the system, vibration within the connector is reduced by reflection through the connector wall. The rubber face/steel flange interface is critical here, and the opposite occurs: the connector is short-circuiting the control rods.