08/30/2016
Q. What are the key considerations for upstream (suction) piping for single and multiple control-volume metering pumps? A. Because of the characteristic pulsating flow of metering pumps (see Figure 7.8.7.1), where peak flow rates can reach three times the average flow, operators must carefully consider suction piping to ensure that it can deliver adequate fluid to the pump inlet.
- The piping must accommodate the peak demands of the pump throughout its full range of operation, as well as prevent offgassing of liquids with high vapor pressure or dissolved gases. This can be accomplished by appropriately increasing the diameter of the suction piping and connections or by adding accessories to increase the flow of liquid to the pump inlet.
- Long lengths of pipe, elbows, tees, strainers, valves and other accessories installed in the suction piping can decrease the net positive inlet pressure available (NPIPA) to an unacceptable level.
- The pulsating flow in the system suction piping creates a pulse pressure that typically subtracts from system suction pressure. For example, a pump operating at 150 strokes per minute and 71 gallons per hour drawing water from 10 feet of half-inch schedule 40 pipe could subtract 10 pounds per square inch from the pump supply pressure. For shorter runs of pipe with minimum restrictions, a rule of thumb is to increase one pipe size above the discharge piping, or two pipe sizes above the pump’s suction connection. Long piping runs with multiple bends, elbows, restrictions and/or higher-viscosity liquids require larger-size piping.
- The most frequent reason for technical support calls to pump manufacturers regarding problems with pump performance is suction piping that cannot supply the demands of the pump. To ensure adequate flow to the inlet of the pump, refer to NPIPA calculations outlined in ANSI/HI 7.8-2016.
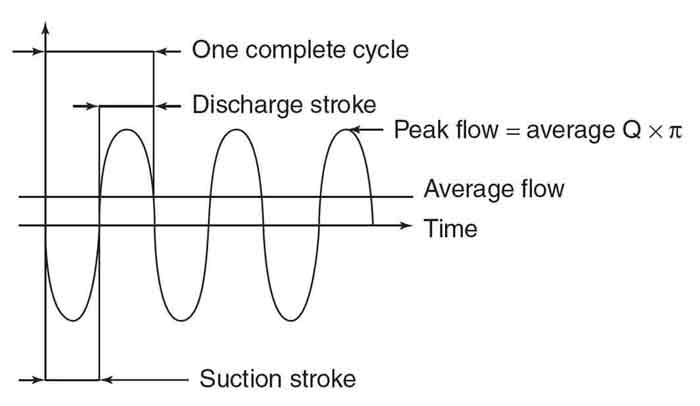
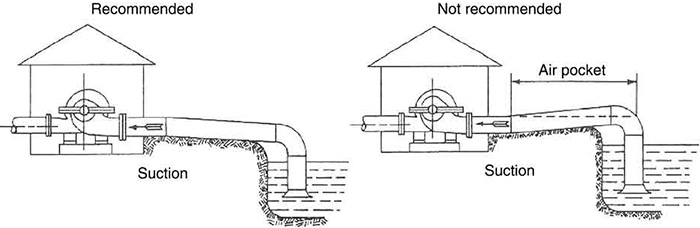
See other HI Pump FAQs articles here.