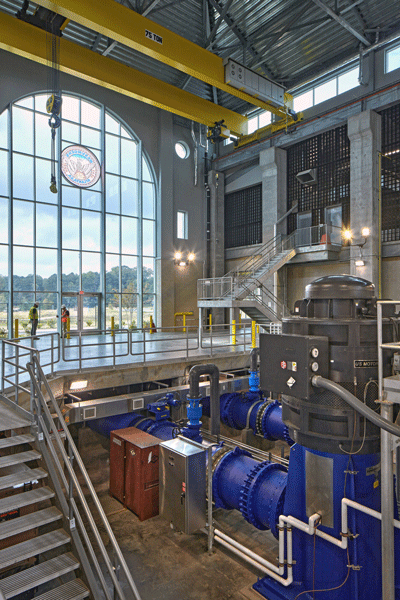
Large alternating current (AC) motors are the backbone of wastewater and water treatment plants, powering the critical equipment that keeps water supply clean and safe. These motors are subjected to harsh operating conditions, including exposure to moisture and chemical compounds, which can take a toll on their performance and life span. Regular maintenance is essential to keep these motors running smoothly and prevent costly breakdowns. This article will explore some key maintenance tips to help users extend the life of their plant’s AC motors.
The first and most important thing for motor maintenance is establishing a regular maintenance schedule and adhering to it. The inspection intervals and required maintenance actions should be determined by a few different factors:
- Recommendations from the motor manufacturer. Read maintenance manual for details on service intervals and suggested maintenance.
- Criticality of the equipment. If the equipment the motor is driving is a critical component to plant operation, then decreased intervals with more check points should be implemented in the maintenance schedule.
- Physical environment in which the motor operates.
Key components to consider during inspection and maintenance are:
Bearings: The support structure and lubrication of the rotor are key. The rotor is also one of the few wear points on a motor and needs to be replaced over time. Periodic vibration or ultrasonic inspections can alert users to changes in the bearings and can let users plan for a bearing replacement instead of an emergency repair.
Windings: They provide the magnetic force that turns the rotor to create the torque that drives the equipment. These windings can become damaged over time due to heat, moisture or chemical exposure. Windings are internal to the motor and are difficult to inspect in most cases. With the right equipment, users can perform a Megger test on windings over time to understand how the insulation of the windings are holding up to the environment. If the windings can be seen during a scheduled maintenance event, it is always good to visually inspect them as well.
There is now test equipment available that will perform complete electrical inspections on a motor and allow a user to build a history of the motor. This will let users see any changes in the motor’s health.
Cooling system: Motors generate heat, and heat above the designed requirement can cause shortened life of the bearings and the windings. It is important to keep them cool to prevent damage. Inspections should always include the cooling system whether it is making sure the fins of a totally enclosed, fan-cooled (TEFC) motor are clear, the cooling fans of the motor are functioning or that there are not outside factors increasing the ambient temperature. Always check to make sure the motor cooling system is operating correctly.
If there are air filters installed on the motor, check them regularly to make sure they are not clogged and blocking airflow to the motor. Clogged air filters can cause a motor to overheat.
Covering the key components in regularly scheduled maintenance is one thing, but to make sure the motor runs at peak performance, it is important to understand a few other parts of the system as well.
One of the key factors in long electric motor life is ensuring it is fed by high quality power. Small imbalances in the voltage or frequency could cause major damage to the windings. It is important to regularly check the voltage and frequency of the plant’s power supply to make sure it falls within the manufacturer’s specifications for the motor. Running a motor at the wrong voltage or frequency can cause damage and shorten its life span.
Another key factor is using the correct size of motor for the job. Overloading a motor can cause damage and shorten its life span. Make sure the motor being used is the correct size for the equipment it is driving. In addition to these specific components, it is also important to consider the overall environment in which the motor is operating. Factors such as temperature, humidity and exposure to chemicals can all take a toll on a motor’s performance and life span. It is important to keep the motor in a clean and dry environment and to protect it from exposure to chemicals and other harsh substances.
Vertical high thrust motors are often used in the water industry, and require some special considerations to protect the bearings. For example, certain motor enclosures have screens that must be cleaned. Also, accessory parts for these motors, such as lubrication systems and water cooling systems, should be included in maintenance as well.
Regularly scheduled maintenance can save money, production and resources. Considering all parts of the motor system and planning maintenance will ensure long life for the electric motors. By paying attention to key components such as bearings, windings and cooling system, as well as monitoring the operating environment, users can help ensure their motors continue to run smoothly and reliably for years to come.