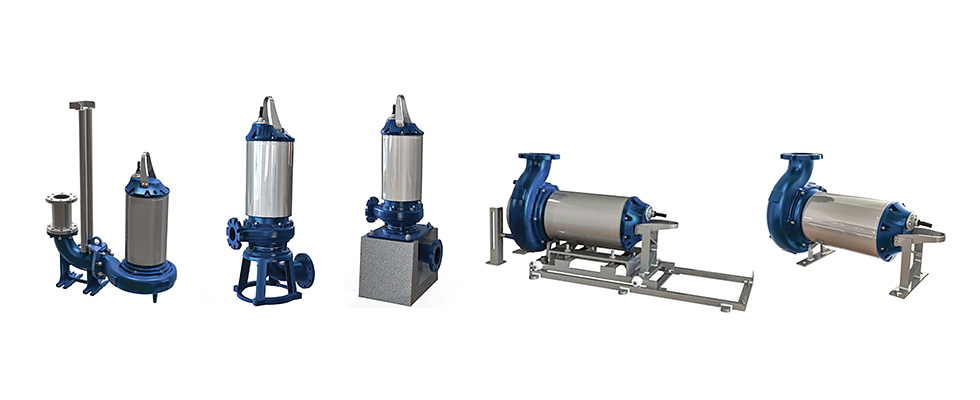
Submersible pumps are pumps that are meant to operate when submerged, either partially or completely, in the liquid they are pumping. In order to make submersible pumps possible, they need a submersible motor. Submersible motors are typically squirrel cage induction type motors that are housed in a hermetically sealed motor chamber. There are a few different technologies available, each with their own advantages and disadvantages.
The Basics of Submersible Motors
While the exact components and construction of the motor may vary between different pump designs, there are a few components that are consistent across all designs.
First, all motors have a rotor and a stator. The stator consists of a laminated steel core, which the motor windings (typically insulated copper or aluminum wire) are inserted in. The winding is also called magnet wire. The entire assembly is varnished with resin to hold the winding coils in place and to fill in the insulation. The stator is the stationary portion of the motor and is permanently attached to the motor housing. The stator can be pressed into the housing, pinned in or the housing can be heat shrunk onto the stator. The rotor is the rotating portion of the motor and includes steel laminations similar to the ones on the stator and the motor shaft. Typically in submersible pumps, the pump end is also built on the motor shaft, so the motor shaft is longer to accommodate. The rotor is suspended within the stator by the bearings. The bearings are often high capacity and can be oil lubricated or grease lubricated. These bearings center the rotor inside the stator, and they allow the rotor to spin inside the stator, which is what drives the pump.
One component that sets submersible motors apart from other electric motors is the mechanical seals. These seals not only seal the motor from the pumped liquid, but they also prevent any cooling fluids from leaking out of the motor. The type of mechanical seals used in submersible motors are varied, but some of the more common styles include O-ring style seals and cartridge seals.
Some manufacturers use commonly available seals, while others have their own proprietary designs. While submersible pumps can utilize one seal, most designs use two seals in tandem. These seals sit inside a seal chamber, which attaches to the motor housing and to the pump volute. Many manufacturers also place some sort of moisture sensor in either this seal chamber or the motor housing. This sensor checks for seal failures by sensing water, acting as a safety feature for the pumps.
Submersible motors also require one or two waterproof cables with a seal connection to transmit power to the pump and to connect any sensors to the control panel. Some manufacturers have a plug-in style with a compressed grommet for sealing, whereas others have a cable that feeds through an opening in the motor housing that is sealed with a form of liquid potting compound.
Finally, the motor has to be filled with some medium and cooled somehow. This is where the designs begin to vary.
Oil-Filled Motors
Submersible electric motors are filled with either oil or air. Oil-filled motors use a dielectric oil that acts primarily as a lubricant and assists with cooling. The majority of the heat transfer occurs between the stator and the motor housing, but the oil also conducts heat from the stator to the motor housing. Oil-filled motors typically need to be at least partially or completely submerged—because after the heat is conducted to the motor housing, it needs to be conducted from the motor housing to the pumped fluid. This means the average oil-filled motor is unable to run dry or be installed in a dry application, although there are ways around this.
Oil-filled motors do have advantages, including continuous bearing lubrication and effective heat dissipation. Because the oil is circulated around the motor, it is able to spread the heat out, removing hot spots. Oil-filled motors also often have a higher service factor, which allows a manufacturer to up-rate a motor, using smaller motor windings to deliver a higher output power. However, oil-filled motors are less efficient than an air-filled motor due to the drag, and they are unable to run unsubmerged for long periods of time without heat damage.
Air-Filled Motors With Cooling Jackets
The primary heat transfer in air-filled motors is between the stator and the motor housing, much like the oil-filled motors. The air in the motor also convects some heat from the stator to the housing, but much less so than the oil.
Air-filled motors often have fins to increase the convection, as more surface area means better heat transfer. Air-filled motors use grease lubricated bearings, as they do not have the benefit of being submerged in oil. The biggest difference between air- and oil-filled motors is that air-filled motors typically include a cooling jacket that convects heat away from the motor housing. This cooling jacket can contain different fluids to dissipate the heat. One style is a closed-loop cooling system that uses a glycol-water mix and a propeller, driven by the motor shaft, to circulate the liquid around the motor housing. A second is a water jacket that requires an external source of clean water, similar to a seal flush. This water circulates in the jacket, dissipating the heat from the motor housing. A third style is a jacket that circulates the pumped fluid through the jacket. This is uncommon, as the fluid circulated can deposit solids in the jacket, reducing its efficacy.
Air-filled motors also have their advantages. First, because the motor does not require the pumped fluid to cool the motor, it does not need to be submerged for operation. Thus, air-filled motors can be easily applied in submersible or dry pit applications, or even submersible applications where the water level stays low. Along with the added installation flexibility, air-filled motors are usually high efficiency, with International Efficiency (IE) 3 ratings or even higher.
Both oil-filled and air-filled motors are well known with submersible pumps, and both have their place in the water and wastewater world. Whether oil or air, both are an excellent choice for your application.
You can find this information and more in SWPA’s Submersible Sewage Pumping Systems Handbook, Fourth Edition. To get your own copy or to order more technical resources, please visit the SWPA website.
Submersible Solutions is produced by the Submersible Wastewater Pump Association to inform and educate in the design and operation of submersible wastewater pumping systems. For more information, click here.