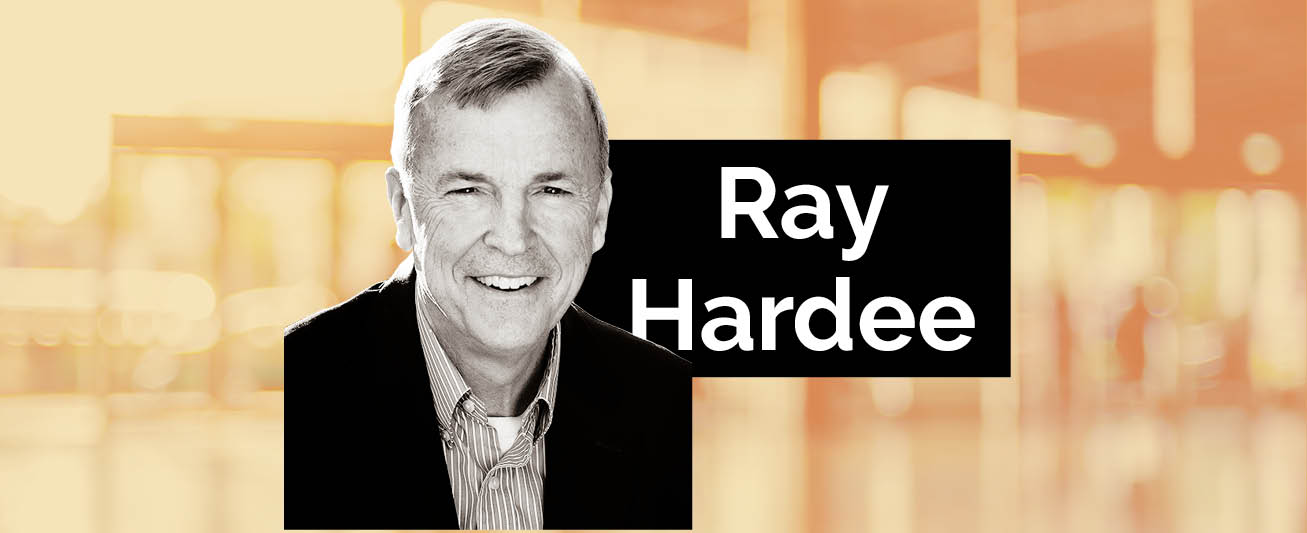
My June 2021 article talked about taking the first step of a digital twin journey for an existing fluid piping system. This month, we will look at a new project from its inception through the design and build stages until the project is turned over to the client. A major step in this task is the requirement to configure, procure and quote (CPQ) all the required project equipment. We will see how digital twin technology can be used to develop a smart CPQ process.
CPQ History
Back in the day, the entire purchasing process was done using paper documents and drawings. It was a manual process where the client and the engineering procurement and construction firm (EPC) would work together to develop project specifications for all equipment items. The next step was developing the bidders list of prospective suppliers satisfactory to the client and the EPC.
The equipment specification documents were sent to the manufacturers on the bidders list. Each supplier would take the EPC specification documents and, using
its equipment catalog data, determine which of its products would meet the user’s operational requirements. They would then apply special factors based on the user’s delivery requirements and other proprietary items. Then would come the price book, where they would develop a current price for the items under consideration. Using this information, the supplier would provide the recommended item and the price in its bid package back to the EPC.
The EPC and client would review each bid package and all discrepancies between the specification and bid documents were identified and rectified. Most of the review process focused on the initial purchase price of each item of equipment along with the manufacturer’s delivery schedule.
In the end, a winning supplier would be selected, and a purchase order would be developed and agreed to by the client/EPC and the equipment supplier. The specified equipment would then be built, the commercial requirements would be validated, and the equipment would be sent to the EPC for use in building the system.
Over the years, these documents were created using spreadsheets and word processing programs. With the wide-scale use of email, these documents often replaced the mailing of paper documentation.
In 2005, many manufacturers started automating their price books by using configuration software. Using the user’s specification document, the configuration software could select the items that met the user’s needs and develop a price for each item. This streamlined the supplier’s task, but it still required the purchaser to manually review each supplier’s bid.
The Smart CPQ Process With the Digital Twin
My February and April 2020 Pumps & Systems articles explained how front-end engineering design was improved by using digital twin technology to minimize oversizing pumps. In that article, we saw how the computerized modeling and analysis (CMA) applications for fluid hydraulics using existing rules provided a better understanding of how the pumps were going to be used in the final system.
The input data along with the sizing calculations can be performed in the CMA applications. Often the CMA application can export this information electronically using an application programming interface (API). This allows the specification data to be electronically passed on to the equipment manufacturers.
The equipment manufacturer can then import the user’s specification information directly into its CPQ application to streamline the creation of its bid document. Once the manufacturer’s bid documents are finalized in the CPQ application, the specific item of equipment is known along with all the supporting data.
Using the pump example, the manufacturer’s CPQ application provides the pump type, size, rotational speed, motor size and the manufacturer’s supplied pump curve, along with a host of supporting information. Since the manufacturer’s CPQ application was used to develop the bid package, that information can be shared with other applications.
The EPC Review
The EPC then reviews the bids from each of the equipment manufacturers on the bidders list. Many EPCs have implemented applications to help in their equipment review process. If the EPC’s review application has access to an API, the bid data from the manufacturer’s CPQ application can be imported further, streamlining the EPC’s review process.
In the past, the EPC’s review process focused on the capital costs, the recommended spare parts and delivery schedules for various equipment items. These commercial details are important when getting the best deal for the new purchase.
One should not forget that when looking at the total system’s life cycle cost, the equipment operating cost is typically 20 to 40 times greater than the initial capital cost. This is where smart CPQ can create notable savings.
Using the equipment operating data supplied by the equipment supplier, the CMA can simulate how each item of equipment will operate when placed into the total system. Using the system power cost feature of the piping CMA application, the annual operating cost of each pump can be determined, providing insight into the total system life cycle cost.
Another advantage of evaluating the pump with the CMA application is the user can determine where it is operating on the curve in relation to its best efficiency point (BEP).
The Future Value of the Digital Twin
Smart CPQ is based on seamless communications between the various applications. This can be done using API technology, but each application sending and receiving information must use the same data schema.
As the number of supporting applications increases, it makes it harder to use the API method of data transfer. Industry standards organizations are helping to define the various terms to describe equipment. If every application is using standard terminology, the data exchange is simplified.
But the holy grail of software applications is to define an interoperable standard for the secure and reliable exchange of data between applications. In computing, an open database connectivity (ODBC) standard provides an independent method and ensures the seamless flow of information among devices from multiple vendors. Using an ODBC standard will provide even more power to the digital twin, which I will cover in future Pumps & Systems columns.