Process scaling affects numerous industries, causing varying degrees of unwanted costs and downtime. The oil industry, for instance, spends up to 0.25 percent of the global gross domestic product (GDP) per year eradicating and treating paraffin wax deposits in piping systems. The mining industry can be negatively affected by scale in process water, cyanide leaching and tailings. Alumina and bauxite refining operations face scale in digesters and transfer piping, which often creates a significant bottleneck in production. The pulp and paper industry experiences scaling in pulp digester screens and white, green and black liquor processing. Other industries that are affected by scale include steelmaking, wastewater treatment, chemical production and power generation. In most cases, the scaling is calcium carbonate or similar culprits. A type of nontraditional scaling is zebra mussels in the Great Lakes region. While not generally classified as scale, they can completely clog large-diameter pipeline in a short amount of time. Struvite scaling is a culprit often seen on exit lines of digesters in wastewater treatment facilities.
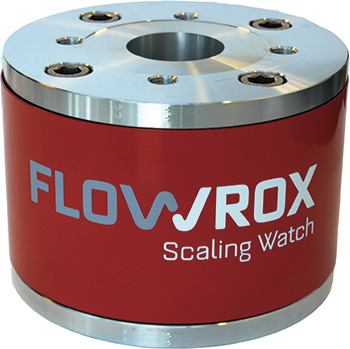
Detection Tools
New scale-detecting instrumentation uses electrical capacitance tomography (ECT) to create a visual display of pipeline scaling without having to physically open the pipeline. This instrument can monitor hard and soft scaling in numerous industries and enables plants to reduce anti-scaling chemical usage and associated costs. Typically, a plant adds more chemicals than necessary to prevent a production shutdown or slowdown. With this instrumentation, plants can know when scale is present and in what thickness so they can use chemicals only when necessary. They can also monitor the effectiveness of the chemicals they are using, and anti-scaling chemical manufacturers can fine-tune their anti-scaling chemicals and validate the success of new formulations. ECT can provide a new level of intelligence regarding what type of scaling is occurring as well as multiphase flow visualization. In a piping system where a vortex effect is present, the instrument can provide clear imagery of this phenomenon. A pipeline that has two or three different chemicals or solids can be imaged to show a video of the flowing process. Even if there is a significant amount of scaling on the inside of the instrument, it will not affect the multiphase flow capabilities.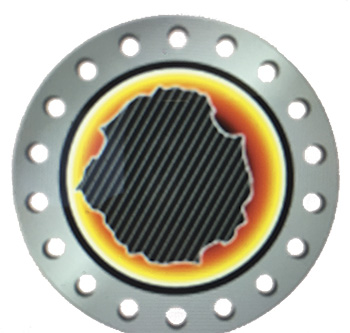