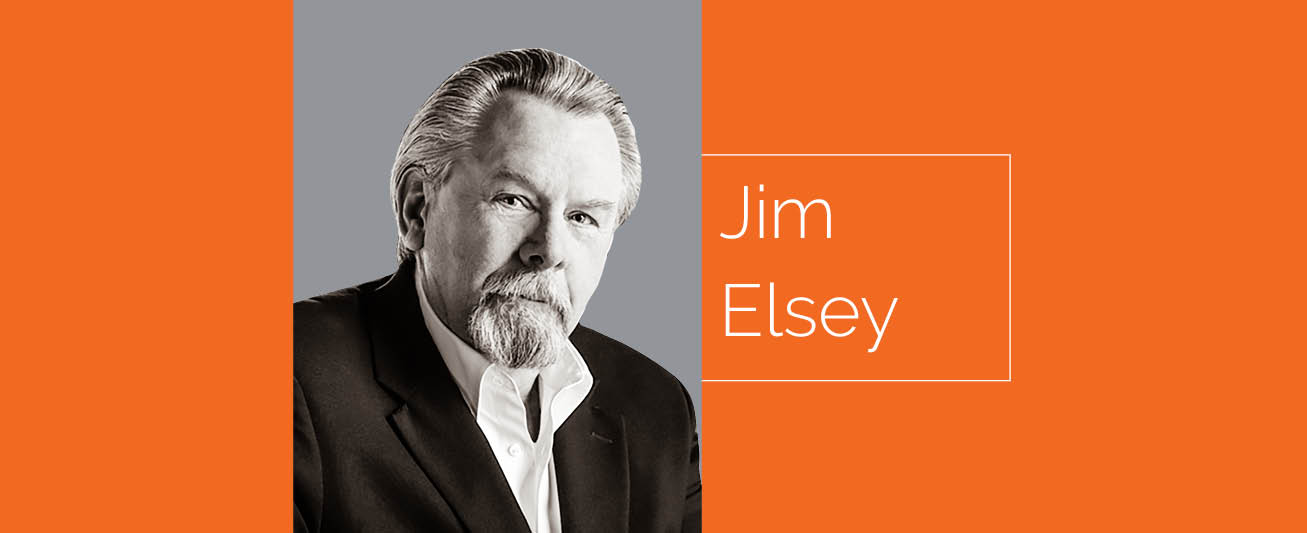
I, like Richard III in Shakespeare’s classic of the same name, sit here looking out of my (castle) window at the falling snow and brooding over things that make me unhappy. What is it that is so bothersome, you ask? In the last 12 months I have read at least 10 different articles, media posts and white papers on various platforms that are incorrect, or at the very least misleading, because they conflate the pump problems of air entrainment bubbles with those of vapor bubbles due to cavitation. When I was a young farm kid and things didn’t line up the way I thought they should, my grandma used to say that “cats ain’t dogs,” and now here I am saying “air bubbles ain’t vapor bubbles.” They are related but not the same thing. This winter, I feel compelled to use my columnist pulpit and attempt to correct this pervasive wrong.
For this column, we will assume the pumped liquid is water at ambient temperature, the water is incompressible and air bubbles are synonymous with gas bubbles. Also a warning that some statements will be repeated for effect.
Air Entrainment Cause & Effect
I have written several columns regarding air entrainment—how it happens, the deleterious effects it has on pump performance and how to avoid the issue. Please see the reference list at the end of the column for more information. Air and non-condensable gas bubbles are both technically gas bubbles, but they are not vapor bubbles. Dissolved air, air bubbles and/or air entrainment will cause a measurable drop in pump performance and at a certain percentage level will cause pump performance issues and damage due to the associated vibrations and mechanical shocks.
Cavitation will also cause an increase in pump noise and vibration, but more importantly a drop in performance, efficiency and impeller erosion—especially as you move right on the pump curve. Not all of the damage from cavitation is metal loss or metal damage. More often the issue is shortened bearing and mechanical seal life due to the unsteady flows and mechanical shock from the resultant surging.
Air Entrainment Disguised
Often, operators believe that a pump problem is cavitation when the real culprit is air entrainment. The opposite problem can also happen. Like diagnosing some diseases in the medical field, the process of eliminating all the other reasons that could be the answer is how the conclusion is formed. If you look at the components that make up the formula for net positive suction head available (NPSHa), you can determine action steps to potentially reduce the effects. For example, if you raise the static suction head or cool the liquid it should reduce the effects, or if you slow the pump down and/or throttle back on the discharge, the symptoms should be reduced. But with air entrainment, all of these checking for cavitation tricks will have almost no effect at all. Refer to my November 2021 column “12 Ways to Mitigate the Cavitation Blues” for more details.
Boiling Water 101
If you boil a pan of water on the stove and observe the initial formation of bubbles, know that these are most likely air bubbles coming out of solution and are comprised of nitrogen, oxygen and perhaps a trace of argon and carbon dioxide. As you continue boiling the water more aggressively, most of those bubbles will be vapor bubbles. A common mistake is to think that vapor bubbles are made of separate hydrogen and oxygen atoms. When water boils, it changes phase, but the bonds between the atoms don’t break, so the vapor is water vapor (H2O in the gas state). There may be some oxygen in the bubbles, but it comes from dissolved air that was trapped in the water. There is no oxygen or hydrogen gas produced by splitting water molecules because that process does not occur in this example.
Where Do the Air Bubbles Come From?
The air bubbles are introduced, not created. Air bubbles in the water stream come from the surrounding air introduced further upstream in the suction side of the system/process and are dissolved, entrained and trapped in the liquid (see references for details). The air/gas bubbles were not created within the boundaries of the system; they were externally introduced—granted, some high velocity pipe induced agitation or impeller action may assist in the process. Regardless, the presence of air bubbles is not due to cavitation, and they are not due to a change of state in the liquid (phase change).
I will state that some processes actually introduce air on purpose, but the problems experienced in the field are often from accidental and unintended introduction. Some closed loop systems by their nature will have air/gas come out of solution, and sometimes chemical additives in the water will exacerbate the issue. For the technical-minded reader, please note it is not my intent to delve into dual phase liquids and subsequent causes of liquid to gas separation. Remember and understand that centrifugal pumps are not designed to be compressors.
Water
Water is a distinctive compound with some unique properties. For example, name another liquid that expands when it freezes and explain why ice will float. The chemical bonds that hold the molecule together are technically covalent but could appear as ionic to the casual observer. To add another complex variable to the energy equation, you can add in the hydrogen bonds and the separate bonds that hold the entire molecule with the others (water molecules often form pairs of four). I mention these bonds that hold the hydrogen and oxygen atoms and molecules together because they are very strong and it takes a lot of energy to break them apart. If you could break the water bonds apart by simply pumping the liquid (you cannot), the commercial costs of producing oxygen and hydrogen gases would be world changing for the gas producers (note the tone of sarcasm).
How Do I Know There Is Air?
Testing for air entrainment is a simple and straightforward process that requires an entrained air gas tester (EGT) and basic sampling procedures. The EGT relies on the basic pressure-volume gas (PV) relationship (Boyle’s law) and operator supplied compression to make the calculation. These tests are fairly accurate.
A simple check (go-no-go test) for the presence of air or other non-condensable gases is to use a clear beaker to collect the sample and simply observe for air bubbles. This test will not reveal the actual quantitative percentage of air/gases.
Classic Cavitation
From the perspective of centrifugal pumps, classic cavitation simply defined is the formation of vapor bubbles in the pump inlet, near the eye of the impeller. The vapor bubbles form because the local pressure has dropped below the vapor pressure of the fluid. Less than a fractional second later, as the bubbles transit along the low-pressure side of the impeller vanes, they enter a region of higher pressure and collapse as a result. I refer to this as classic cavitation to differentiate it from other causes of cavitation, such as suction or discharge recirculation that manifests on the other side of the impeller vane. Note there were no air bubbles present; this process is a phase change (liquid to gas).
The Difference In Energy Levels
When an air bubble collapses, there is little to no energy required or released in the process. Cavitation bubbles collapse with a high amount of energy. Cavitation bubbles that break down in the middle of the impeller passageway collapse symmetrically (equally from all directions), and so there is less cause for concern other than potential noise and perhaps some vibration.
However, when the vapor bubbles in a pump impeller collapse adjacent to the metal surface of the vane, there is a much higher potential for damage and concern due to metal loss from the substrate. When the bubble collapses near the vane surface, it will collapse asymmetrically. Because of its proximity to the vane surface, the bubble geometry changes and makes the action more lethal. When the bubble collapses, it is not just the surrounding fluid that rushes in to fill that void.
More importantly, it is that the vapor is changing state from a vapor (back) to a liquid. I repeat for emphasis that the amount of energy transferred for a change of state is very high. You can calculate the energy using enthalpy equations (refer to the heat of vaporization or the enthalpy of vaporization equations). The collapse of a vapor bubble is exponentially more impactful than if it was an air bubble.
I repeat that with vapor bubbles there is a change of state from liquid to vapor and back while an air bubble creation or dissipation does not involve a change of state. Further, when the vapor bubble collapses asymmetrically there is a resulting reentrant micro jet burst that on a local nanoscale level is very powerful (the local scale is 1 x 10-9, that’s 10 to the negative nine exponent or a billionth). Local pressure forces involved in the micro jet burst can have resultant shockwaves higher than 10,000 pounds per square inch gauge (psig). The bubble collapse phenomenon can occur with a high periodicity of 300 times per second, and all of this action happens at the speed of sound. The resultant microburst jet almost always directs itself at the adjacent surface in lieu of the fluid stream. The substrate of the vane material is subjected to a localized surface fatigue failure. The average life span of a vapor bubble from creation to collapse is about 2 to 3 milliseconds.
Not everyone agrees if it is the shockwave or the reentrant micro jet burst that creates the damage—likely it is the combination. Hopefully with this perspective you begin to understand how cavitation can damage an impeller in short order. On a scientific level, besides the enthalpy equation mentioned earlier, the energy of the bubble collapse is simply a kinetic energy calculation and is a function of the mass and velocity (kinetic energy = 0.5 X mv2) where m is the mass and v is the velocity.
Vapor bubbles formed in water at ambient temperature are of a much larger size (mass) than if the water temperature was close to and approaching 212 F. The larger the bubble the more energy involved and the more damage incurred. The summary result is that cold water cavitation is much more dangerous than hot water cavitation. Water at 70 F will increase in volume by approximately 54,000 times when vaporized.
Sometimes overlooked in cavitation discussions is the root cause for the vapor bubble evolution, in that pumps do not so much generate heat to make the water flash to vapor, but instead it is the drop in pressure near the impeller eye. Remember you can boil water at 33 F if you can reduce the pressure low enough.
Final Note
Be careful with your choice of words when describing the noise or performance drop of a pump in trouble. Air or gas coming out of solution is totally different than the formation and collapse of vapor bubbles. And cats ain’t dogs.
References
“Vapor Bubbles” Annual Review of Fluid Mechanics (2017). 49:221–48, Andrea Prosperetti
“Growth and Collapse of a Vapour Bubble” Journal of Fluid Mech. (2009), vol. 632, pp. 5–16.
‘Cavitation and Bubble Dynamics”, Cal Tech. ISBN 0-19-509409-3, Dr. Christopher Earls Brenne
“Cavitation vs. Air Entrainment”, Pumps & Systems, Jan 2016, Dr. Lev Nelik,
“How to Reduce or Eliminate Air Entrainment” Pumps & Systems, Dec 2017, Jim Elsey,
“Guidelines for Submergence & Air Entrainment” Pumps & Systems, April 2016, Jim Elsey
“Why Cavitation Occurs & Ways to Treat it” Pumps & Systems, May 2019, Jim Elsey
“12 Ways to Mitigate the Cavitation Blues” Pumps & Systems, Nov 2021, Jim Elsey
NRC Report NRC-DR-09 -0270, November 2009 Allan R. Budris