A small percentage of bearings achieve their application design life, and in pump and motor applications, bearings are the most susceptible components to premature failure. The cost of a failed pump or motor add up quickly, but end users can take several precautions that help maximize bearing life. In most cases, the cost of the equipment repair is less than 8 percent of the overall expense of the failure—while downtime costs usually account for an estimated 90 percent. Pump users frequently ask how long certain bearings should last. The answer depends on the amount of information that can be provided at the time the question is posed. Life calculations can be run based on furnished application data, but it is difficult to accurately predict bearing fatigue. Bearing life is commonly measured using an L10 or L10h calculation, which is a statistical variation of individual bearing life that is most often communicated as life in hours or revolutions. A bearing's L10 life, loosely interpreted from International Standards Organization (ISO) and American Bearing Manufacturers Association (ABMA) standards, is based on the lifespan of 90 percent of a group of identical bearings in a given application. In a nutshell, it is a calculation of how long 90 percent of the bearings will last in that given application. What makes this equation impractical for determining definite bearing life is that it is based on the load capacity of the selected bearing, the actual application loads, the bearing type (ball or roller) and the rotational speed (in revolutions per minute [rpm]) of the application. The L10 life calculation does not consider temperature, lubrication and other key factors related to pre-service damage that are crucial to achieving the designed application bearing life. Proper storage, treatment, handling, installation and maintenance are simply assumed. Predicting bearing fatigue without consideration of these variables is problematic. As a result, an estimated 10 percent of bearings meet or exceed their calculated fatigue life.
Limit Pre-Service Damage
Proper storage and handling can limit pre-service damage to bearings. Standard bearings are predominantly produced from 52100 steel, a highly refined steel material that can be prone to oxidation. If end users do not handle bearings like they do other precision equipment, the longevity of the bearing can be compromised. Bearings are typically packaged at the factory with a Ferrocote or a thin coat of preservative oil. Handling the bearings with bare hands or wiping off the preservative can reduce corrosion-resistance. If a thin coat of preservative or oil is not re-applied, damage can occur. Bearings should be kept in an area free from vibration to avoid false brinelling, which is a phenomenon characterized by localized material wear or damage that occurs as a result of frictional vibrating contact between surfaces.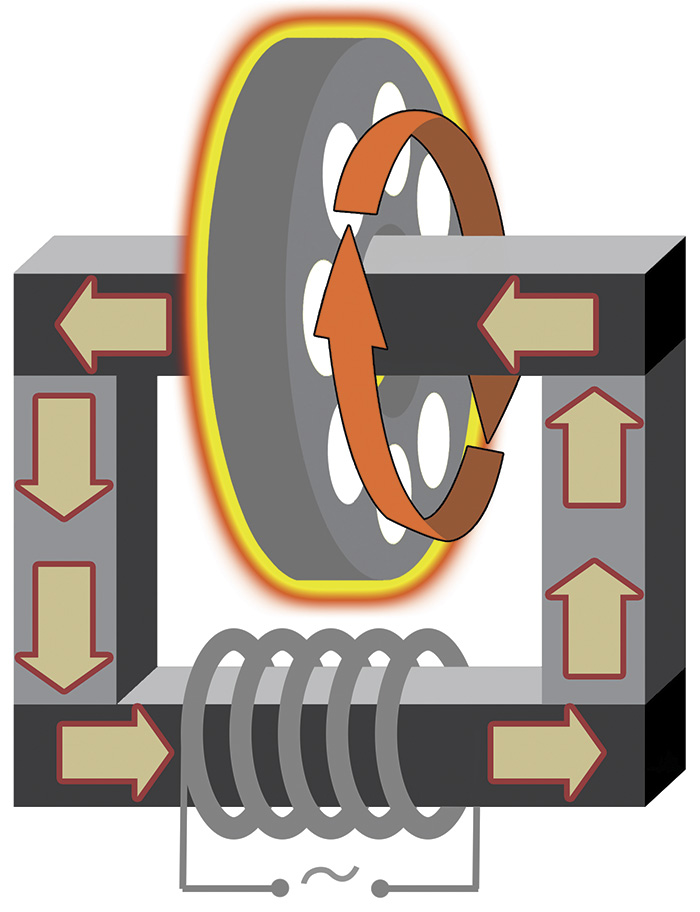
Apply Correct Lubrication
Lubrication issues account for up to half of all failed bearings. Failures may result from insufficient or excessive lubrication, improper lubrication methods, incompatible lubrication, incorrect viscosity and contamination. Lubrication separates contact surfaces, reduces friction and protects against corrosion. Proper lubrication can also seal equipment from the ingress of contaminants and, in the case of circulating oil, offer heat displacement.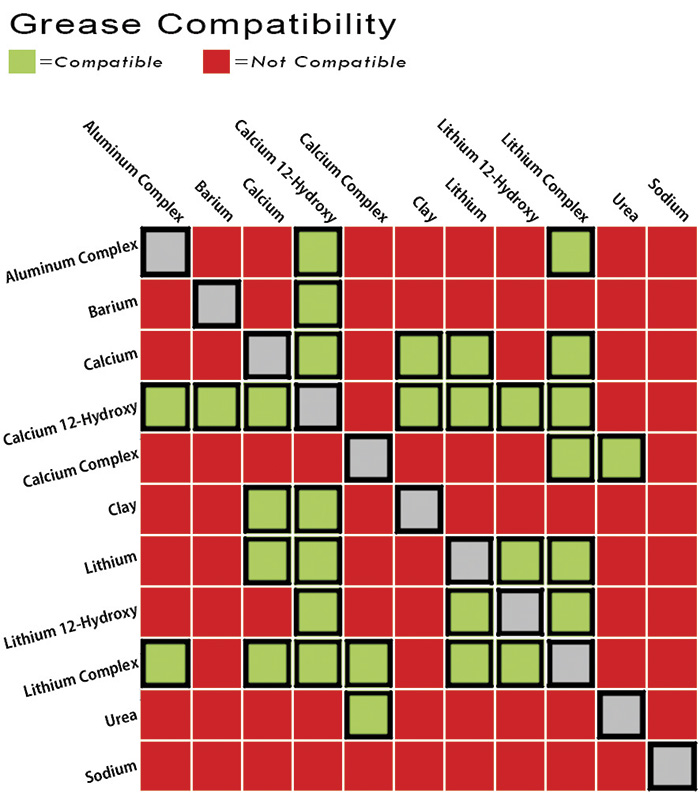