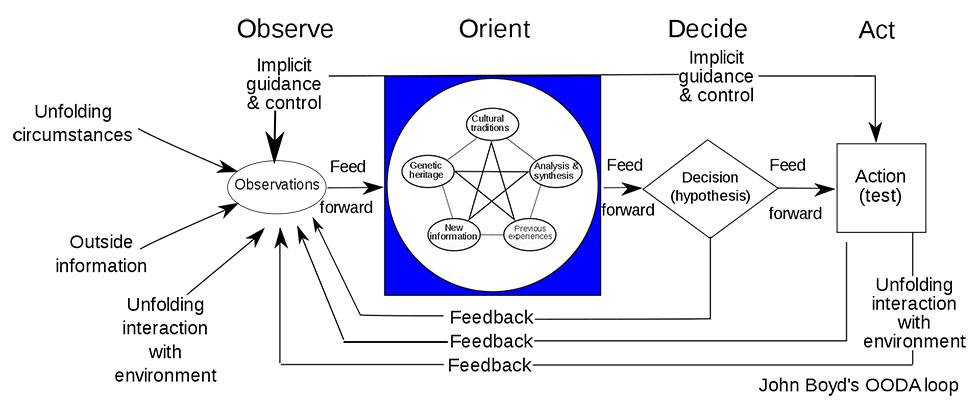
Colonel John Boyd was an endearing eccentric and strategic genius. Over his career, he created the Air Force Aerial Attack Study, invented the energy-maneuverability (E-M) theory, was the father of the F-15 and F-16 fighter jets and created a decision-making framework called the OODA loop. His thinking about strategy spread across the United States armed forces, including his Patterns of Conflict briefing which provided the basis for the U.S. military’s strategy in the first Gulf War, leading to their 100-hour victory. It still underpins the U.S. Marine Corps fighting doctrine to this day.

Boyd’s OODA loop is a four-step decision-making process of observe, orient, decide and attack. This cycle can be a terribly destructive force, virtually unstoppable in causing panic and confusion, and as Boyd stated, “unravel the competition.” This is true whether the loop is applied to combat, in business practices, in sports or even flange sealing reliability. With the OODA loop, the losing side rarely understands what happened.
One main point about the OODA loop is constantly striving for perfection and reevaluating. One example of this work is at a fertilizer plant in Woodward, Oklahoma, where the plant rallied after a near miss of a failed flange and created a flange sealing program.
In October 2015, the plant had a flange blow apart in the synthesis loop area, which is the highest pressure throughout the facility, and created a hydrogen fire. Operators were 15 to 20 yards from the area eating lunch right next to the control room doors that rattled from the explosion.
Employees realized while in the observe phase that one issue they needed to address was that most of their flange assemblies are tightened using “tool tight,” a term for using a mechanic’s feel or judgment to tension flanges at the facility. There have been many studies that this type of method has excessive error and results in many issues of under compressed gaskets. In their act phase, they went back and rewrote their policy that would require them to torque or tension all their flanged joints at the plant, creating a culture of bolt tensioning. They then went around the OODA loop again and modified the procedure and training to include torquing. After about a year into the process, the team took a step back and again, did a continuous improvement loop looking holistically at what they were doing with flange closures.
They noticed failures across multiple levels that were torqued where the studs could not actually handle the torque that was put on them to keep the gasket crushed. Also, they saw that sometimes the gasket was reused in certain applications. Once again, with this information they acted by updating the procedure and instituting more training.
Another observation was the condition of the gaskets; some being used were 20 years old hanging on a wall of dust. They decided to keep them in a climate-controlled environment to ensure there are no defects from the gasket that can cause a failure. Soon the group realized this incident had spurred them to update their closure form package to include a detailed list of things that must be looked at every time for every specific application including:
- the gasket needed
- the bolts and nuts needed
- proper torque specifications
This one sheet for reliability gives the technician all the information they would need. The next loop was working with the manufacturers of the gaskets and creating standardized torque loads for standard and nonstandard flanges and using the resources of the manufacturer for each piece of equipment to ensure the calculated gasket crush is achieved with the
torque required. The guiding principle for the team was to ensure the closure form was simple in listing all the steps in a way that even the most inexperienced person would be able to assemble the flange.
In the end, the plant shifted their philosophy of flange sealing by focusing on doing it right from start to finish and looking at all individual components and making sure it is right the first time. This holistic approach to flange sealing challenges created a culture change that kept the long-term interests of the plant in mind.
Winning Begets Winning
After the plant’s success got around to other facilities, another team started to create their own program to ensure any seal is tightened to precisely the right amount, or as they say at the plant, “all leaks tight, done right.”
The plan started with the goal of running between turnarounds with no outages or failures. They wanted a consistent reliable joint for all flanges. The integrity of the joint and maintaining a leak tight seal to achieve zero leaks they believed was attainable to drive for continued improvement.
A few of the different areas the team focused on included:
- expensive temporary leak repair of flanges
- performing a root cause analysis on failed flanges
- misalignment on a flange
- star tightening pattern
We invite your suggestions for article topics as well as questions on sealing issues so we can better respond to the needs of the industry. Please direct your suggestions and questions to sealingsensequestions@fluidsealing.com.