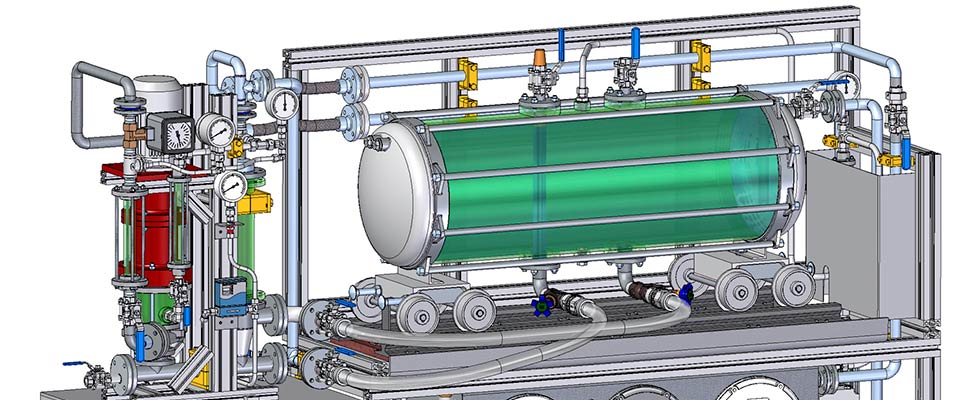
Pumps used for unloading railway tank wagons are nothing unusual. The unloading of rail wagons that are loaded with liquid tar, on the other hand, is less common. Due to its high viscosity, the raw material is difficult to handle. To optimize the unloading process, an end user who needed to unload raw tar from rail wagons was looking for a pump that could satisfy the following criteria:
- the complete emptying of residues without pressurizing the wagons
- meeting the highest safety levels
- the unloading process carried out with only one pump for economical reasons

In practice, this meant that four rail wagons containing raw tar had to be emptied with one pump. Generally, such requirements are difficult to implement. One important criterion was the dry-running safety, which is not typically provided by standard pumps.
Standard pumps are vented via an empty pressure line when they are at a standstill. The level of the liquid decreases as the pumping process progresses, with more and more gas being entrained. Gas bubbles develop, which reduce the performance and cause rough running. If the gas content is too high while the pump is running, the flow can stop completely. This stops the conveying process, and the pump has to be vented, resulting in downtime. Nowadays, unplanned downtimes are usually indicated by diagnostic and early warning systems.
The Solution
For a centrifugal pump manufacturer, this was one of many challenges that had to be overcome. The engineering team and the pump manufacturer provided advice and recommendations (Image 1), starting with the design of the pumps through to commissioning and beyond. Dry-running pumps with and without self-regulating pumping and sealing systems that have been adapted to the medium were available and, in this solution, the vertical pump was equipped with a magnetic coupling and liquid-lubricated slide bearings.
This design combined the properties of the self-regulating vertical pumps with those of the horizontal, dry-running, hermetically sealed pump. The pump is permanently dry-running and works without bearings in the pumped liquid. The grease-lubricated roller bearings are protected against the product vapors by a gas barrier.
The shaft gap sealing concept of this permanently dry-running type of pump consists of several components.This includes the hydrodynamic relief of the bearing and sealing unit from the pump delivery pressure. This is achieved by back vanes and the gas barrier, which prevent the penetration of product vapors into the bearing unit. The magnetic coupling, free of eddy currents, hermetically seals the pump with respect to the environment. Because of the vertical orientation of the pump, the bearing and sealing unit runs entirely without product contact, even in the event of a sealing gas failure. Roller bearings are typically in service for more than five years of continuous operation.
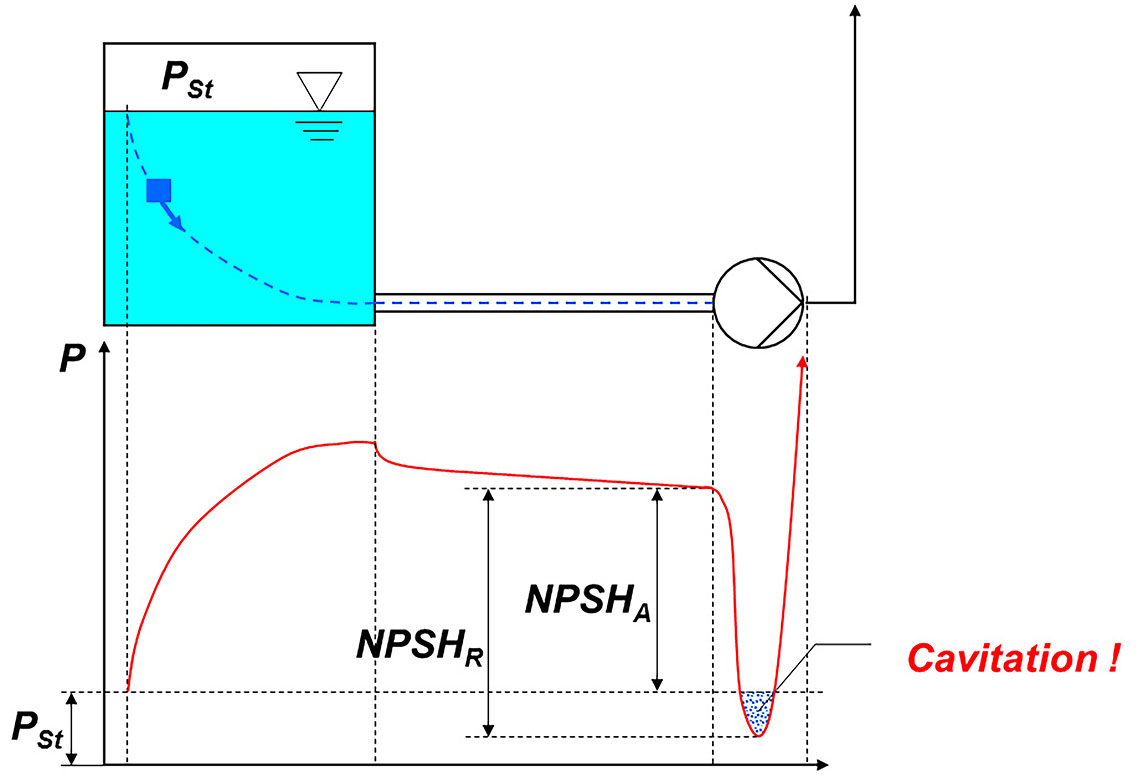
In addition to the economic and technical services, the solution offered maximum security in the event of leaks, ease of use and savings in construction costs. Intrinsically safe centrifugal pumps—pumps that, based on specific design principles that prevent unsafe conditions in the event of a malfunction—automatically adjust to varying feed rates.
The principle is based on pressure equalization between the pump impeller and the feed vessel: when a medium flows into a container, the liquid level rises until the inflow and outflow of the container are in equilibrium. These control characteristics work without any additional mechanical or electrical devices. These pumps convey in an inflow-dependent manner and automatically reduce the flow rate without any pressure reduction at the impeller.
As a result, the net positive suction head (NPSH) is close to zero. This pump type also has a self-venting function, which makes it insensitive to gas bubbles. The pumps generally operate without cavitation, are safe to run dry and are reliable in operation.
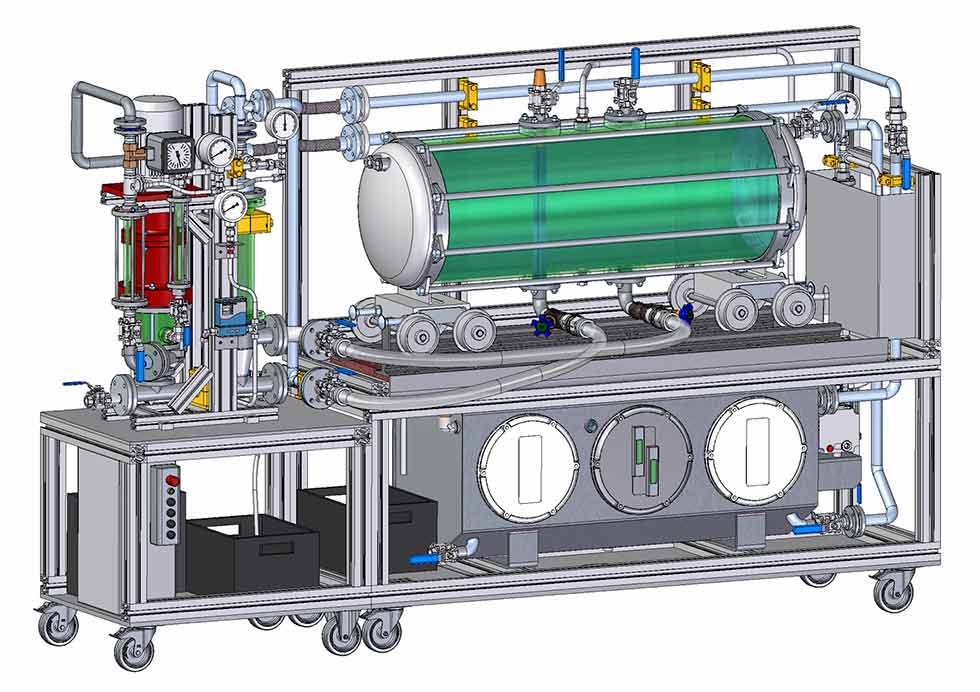
The low-pulsation pump keeps the product and bearing area separate, making it suitable for almost all media. The fields of application range from gas-laden, viscous, hot or boiling liquids to liquids containing solids. The typical media include toxic liquids with special shaft seal requirements: titanium tetrachloride, liquid tar or liquid gas. The pump can handle product temperatures of up to 400 C (752 F) without a cooling medium. The self-regulating conveying behavior does not require a minimum flow rate. Cavitation problems do not occur; the pump has an NPSH required (NPSHr) value of < 0.1 meters (m). Service lives can exceed 15 years.
In addition, costly planning and construction measures such as the construction of pits are not necessary. This makes this type of pump—which is installed at ground level—more simple to install, operate and monitor. The four rail wagons are emptied from below and the supply lines of the rail wagons have to be opened. At startup, the pump lowers to the level in the pipe template. The liquid flows out of the tank wagons under the force of gravity. The pump is only switched off when the minimum level in the pipe template has been reached and, therefore, all rail wagons have been emptied.
Definition of Dry-Running Safety
Many pumps use the medium to be pumped to sufficiently lubricate the slide bearings and cool the seal that is used. Dry-running safety is the ability of a pump to operate permanently without any medium. This is achieved by decoupling the bearing and sealing unit from the pumped liquid.