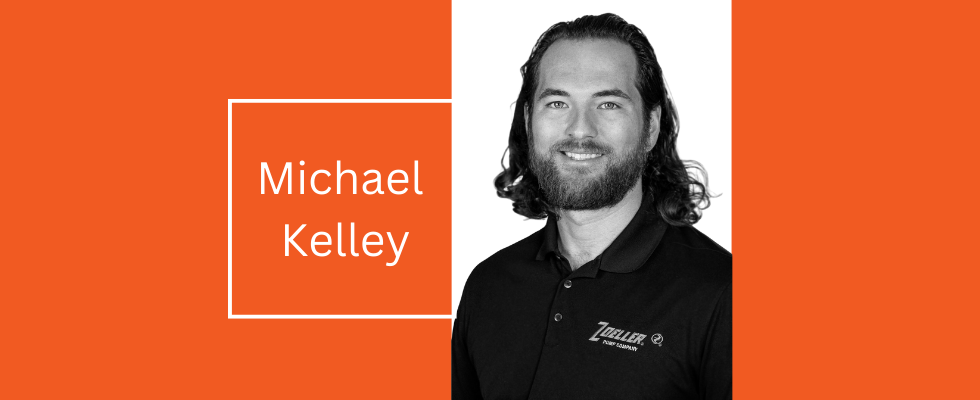
In Part 3, we covered prepackaged, submersible pump stations for commercial and municipal sewage applications. Moving into Part 4, this article will continue to leave each flush a mystery. The same data needs to be gathered for larger applications as is needed for residential applications. However, as I said previously, municipal regulations vary from state to state and city to city. This article is to serve as a guide to get you in the right line of thinking. Be sure to familiarize yourself with your local regulations to ensure your design is compliant and smooth over the course of the submittal process.
Controls
Catalog panels still hold their place in the commercial market and, in some cases, the municipal market due to their
cost-effectiveness and increased options for remote monitoring. Commercial markets tend to be more cost sensitive and will often opt for standard catalog panels. For municipalities, interfacing, communication and functionality tend to prevail and lean toward custom to simplify integration into their existing infrastructure. Municipalities will often have a standard specification written that is tweaked to fit the pump being controlled. When cutting and pasting an old or standard specification for a new job, be sure to review and ensure the features that were used in the past are applicable to the new application.
One key component of controlling a pump is level monitoring. There are several options for this, including floats, pressure switches, conductors, pressure transducers, ultrasonic sensors and more. The key is to understand how they monitor liquid level. Most control floats, pressure switches and conductors monitor a singular point within the wet well, requiring an independent sensor for each set point (off, on, lag, high water) with either an open or closed signal relayed to the control panel.
Open and closed signals are the simplest to interpret from a control perspective and are commonly used in standard catalog panels for their cost-effectiveness. Transducers and ultrasonic sensors can measure a range of water levels with a 4-20 milliamp (mA) output. This allows for a single device to monitor all set points, though a programmable logic controller (PLC) is typically needed to interpret the 4-20 mA signal and to establish and differentiate the various set points.
Sensors with 4-20 mA signals are common on systems with VFDs to speed up or slow down the pumps as the water level rises or falls. Many times, float backups are used to maintain basic operational function in case the single 4-20 mA sensor fails.
Communication and remote monitoring are things to consider and are often required by municipalities. Many metrics can be monitored within a control panel, such as pump status (off, on, fail), water level, power fail, seal leak, thermal overload, pump speed, current, run times, etc.
The bigger question is how to communicate that information. Buzzers, lights, displays and human machine interfaces (HMI) can communicate that locally. To provide that information to a remote location, custom features may be required. Some of the most common communication methods are via Wi-Fi, auto-dialers or supervisory control and data acquisition (SCADA) systems. Again, municipalities will typically have a specification on this.
To finalize the design, there should be some coordination between the owner and the panel manufacturer to ensure all needs are met. The minimum information needed is the site voltage, pump voltage, amps, horsepower, sensors, the panel environment/location and as much detail on the application and custom features that may be desired as possible.
Fittings, Valves & Accessories
In residential and light commercial applications, it is common to house all the valves inside the wet well to reduce the footprint and cost of the basin. However, on large commercial and municipal applications, valves should be placed in a separate valve box to provide access without shutting the system down or requiring Occupational Safety and Health Administration OSHA permits. The valve box can be attached or a separate vault next to the wet well. Image 3 depicts a fiberglass station with an attached valve box.
At a minimum, independent check valves and shut-off valves should be used for each pump. The check valve protects the pump from water recirculating in multipump configurations and backflow from the force main, which could lead to short cycling, overflows and impeller backspin. The shut-off valve allows service providers to isolate a pump from the
system to remove, service and replace the pump as needed while maintaining operation with the other pumps.
Other design features to consider are the covers and ensuring they are rated for the environment (e.g., traffic rated covers for roadways or parking lots). Netting or grates are a great option to consider for fall protection when the hatch is open. Also useful is a hoist for removing pumps without a service truck. Site access should also be considered in the event a service truck is needed to pull or haul a pump out.
Startup
A critical key in trouble-free operation and commissioning of a new station is a detailed plan and a knowledgeable person to oversee that it is done correctly. Startups are generally overseen by a manufacturer’s representatives, and this is often required for warranty claims. A startup procedure should inspect the installation and verify multiple check points before the pumps and panel are powered up. Manufacturers generally have a detailed startup procedure to ensure everything was installed to their standards. Verifying proper operation at startup will ensure the longest life of the system and provide the necessary documentation in the event a warranty claim is needed.
Most every municipal and large commercial application is going to be different than the last. The process remains the same, but the pump, basin and controls should be specific to each application. Start with gathering the correct data, and work closely with the manufacturer to ensure that all needs are considered and each flush is kept a mystery.