Control system upgrades increase safety and reliability.
07/10/2015
Pearl Harbor Naval Station and Hickam Air Force Base have both grown around the historic port, known as Wai’Momi to native Hawaiians, adjacent to Honolulu on Oahu's south shore. Pearl Harbor Naval Shipyard (PHNSY), at Joint Base Pearl Harbor-Hickam, is a regional maintenance center for the Navy's surface ships and submarines. It is the only intermediate maintenance facility for submarines in the Middle Pacific.
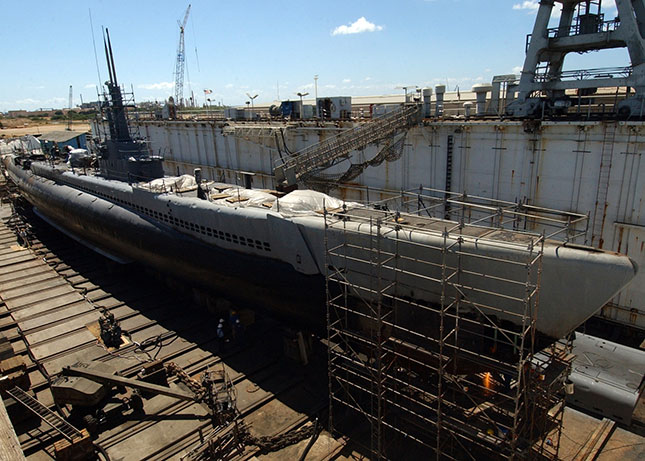