Pumps play a major role in the processes of power generation plants, so healthy boiler feed, condensate extraction and cooling water pumps are all essential to providing an efficient and reliable service. To keep this equipment in the best condition and operating at optimum levels, a considered and cost-effective approach to maintenance and renewal is required. Power generation plants have always relied on their pumping assets to provide reliable service, but as the equipment ages, it requires more attention in terms of maintenance. As the length of time in service increases, the magnitude of repairs can escalate. This leads to a decision of whether it is best to repair, retrofit or replace the asset. By looking at each option, it is possible to assess the most cost-effective solution for each situation.
Minimize Downtime
From the outset, the best policy is to implement a preventative maintenance strategy that will enable potential service issues to be identified and resolved within a proscribed time frame, such as an annual shutdown period. However, unexpected failures can still happen, so it is advisable to also have a contingency procedure in place for isolating and removing pumps as necessary.Repair & Replace
During the period that the pump is being repaired or serviced off-site, either a replacement must be installed, plant outage must be sustained or the remaining assets will have to cover the duty requirement until the pump is reinstalled. In almost every application associated with the thermal cycle, the pumps are process critical and will have to be swapped out for service. In a scheduled overhaul or nonemergency situation with proper planning, replacement wear parts should be in stock at the user’s site, pre-purchased for the planned maintenance. If the replacement wear parts are readily available or reproducible by the chosen repair partner, this allows the work to be completed within the planned maintenance time frame. This is important when a spare pump is not available and ready for exchange.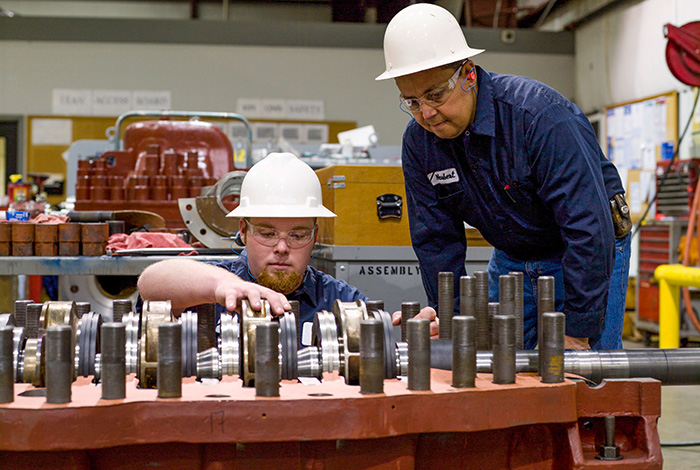
Retrofit to Maximize Performance
Proper planning is important in cases when the pump is of an age where a simple repair can become more difficult due to changes in design or poorly documented past repairs. Planning may require the assistance of a known or trusted repair partner. In most cases, employing one with pump design and manufacturing capabilities will be beneficial. Very often, it will be possible to engineer new components that incorporate modern design and manufacturing technology to create parts that are more effective and durable. Then the simple repair begins to look more like a retrofit, where additional benefits can be included with the replacement of a series of parts. Improved performance or longevity can be achieved by addressing a design issue or simply applying new materials and designs developed during the normal product life cycle. Many pumping assets have been in service for a considerable number of years. During that time, the technology used in designing and manufacturing components such as impellers has progressed a great deal. This means that plant owners can benefit from increased efficiency or make changes to duty cycles without having to replace complete pumps. Modern 3D design software and computational fluid dynamics (CFD) are now integral to creating an optimum hydraulic design. Companies that frequently repair pumps from other (sometimes obsolete) manufacturers will use these tools in tandem with reverse engineering techniques to manufacture new components when required.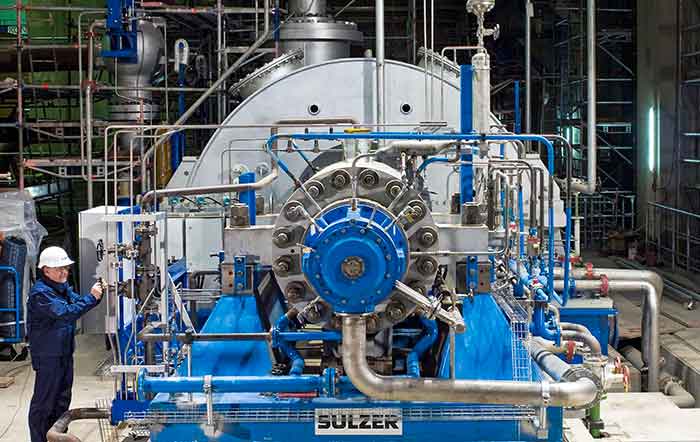
Replacement—Invest in the Future
All indicators suggest that power demand will continue to grow, so it is important for companies to invest in assets that will improve process efficiency and performance. While retrofits can take advantage of some new technologies, the full benefits can be limited by the original size and structure of the pump. Capacity limits will also be dictated by other equipment beyond just the pumping elements such as pipework, motors, drives and control infrastructure.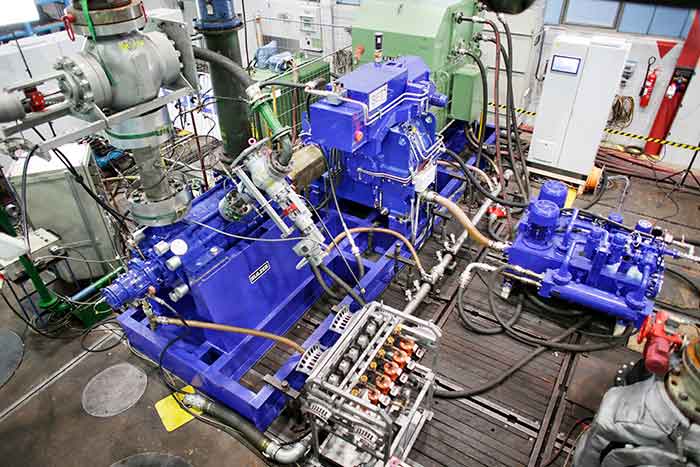