When facilities—whether paper mills, refineries, or chemical or waste treatment plants—decide to implement pump system improvements, the first question is always the same: Where to begin? This month’s column looks at the pre-screening process, when plant management teams decide which system to tackle first. The pre-screening process quickly identifies which pump system has a high probability of improving plant operations, reducing total cost and increasing system uptime. A pump system assessment takes an average of one week. Some system assessments will be profitable and have a short payback, but some may not meet the assessment goals established by a plant’s financial management team (see “A Financial Justification for Pump System Improvements,” Pumps & Systems, March 2014). To improve the chance for success, the plant management team needs to start with systems that have high savings potential. That is the purpose of plant pre-screening. The following suggestions are outlined in the American Society of Mechanical Engineers (ASME) Energy Assessment for Pumping Systems standard:1
- Focus on energy use and annual hours of operation. The greater the power consumption is, the greater the potential savings.
- Concentrate on systems with centrifugal pumps operated at fixed speeds. Because pumps have a tendency to be oversized, they offer a great savings potential.
- Pump systems that are controlled by throttle valves, bypass flow, recirculation or that are not controlled should be candidates for improvement.
- Identify systems that have had major changes in design or operation since installation.
- After discussions with the operation and maintenance staffs, identify systems that are difficult to control or experience high maintenance frequency or cost.
Pre-Screening Worksheet Development
A pre-screening worksheet is the best way to collect the required information. Once the data is collected, the operational management team can prioritize the worksheet to develop an action plan and start assigning resources. The pre-screening worksheet presents collected data and identifies systems with a high probability of success. Exact data is not required during the pre-screening process. Facility managers should concentrate on identifying energy saving patterns that prioritize their plants’ needs. The key to pre-screening is to collect easily accessible plant data first. Design documents, equipment data sheets and plant instrumentation have most of the information used during pre-screening. Conversations with a plant’s operating and maintenance personnel are also valuable resources. Reference 1 has a sample pre-screening data sheet. Once the data is collected in an electronic spreadsheet, a weighting factor can be assigned for the data to meet the plant’s pump assessment program objectives. The set of weighting factors will differ depending on the program objectives. The factors for reducing energy consumption will not be the same as those for reducing operating and maintenance costs. The group assigning the priorities should have a clear picture of the assessment program’s goals. In this example, the weighting factors will be for system usage—how many hours per year the pump system’s operation is required. Table 1 shows typical ranges for system use with a weighting factor. The system usage weighting factor identifies systems based on their annual hours of operation.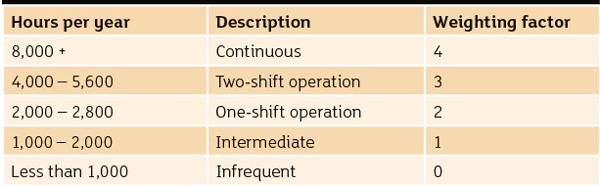
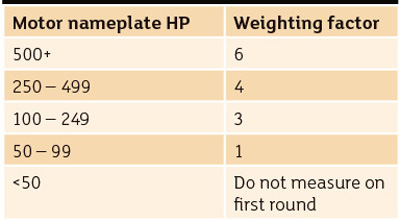
Using the Pre-Screening Worksheet
The example in this section shows how the pre-screening worksheet prioritizes three systems:- System A has a single pump driven by a 500-HP motor. The system operates for 600 hours per year.
- System B has a single pump driven by a 300-HP motor that runs 8,000 hours per year. During the pre-screening, maintenance personnel said these two pumps seemed to require more maintenance.
- System C has two pumps running during operation. Each pump is driven by a 200-HP motor, and the system operates for two shifts. During the pre-screening, operations personnel said both pumps run constantly to minimize pump starts.
- System A receives six points because it has a 500-HP motor and zero system unit points for a total of six points.
- System B receives four points for its 300-HP motor and four points because of its continuous operation, for a total of eight points.
- System C receives six points—three points for each 200-HP motor and three points for its continuous operation during two shifts, for a total of nine points.