The offshore industry faces two main challenges: maximizing production within the limits of the reservoir and minimizing operational costs while maintaining the safety of the platform. Pumps form one of the main groups of equipment that influence the outcome of both challenges, and they require expert knowledge to ensure continued reliability and performance. Some experts argue that in each case, industry engineering expertise and commercial innovation are required to deliver these goals. Furthermore, the capital expenditure to improve reliability is often far outweighed by the costs incurred by an unexpected failure and the subsequent costs of lost production. By taking a proactive approach and involving an expert maintenance provider, platform operators can deliver significant benefits to the business in the long term.
Improving Performance
In the years following commissioning, the actual duty requirements of production pumps are likely to change. Production rates may start to decline after the initial plateau period, or the connection of additional wells may mean that potential production is being limited by the processing trains that were designed for lower volumes.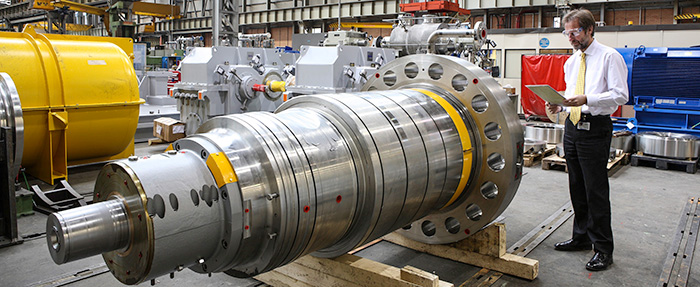
Proactive Maintenance
A proactive maintenance regime is crucial to identifying potential issues before they develop into problems. However, this requires knowledgeable and experienced personnel to carry out the in-situ platform maintenance, and these skills take time to perfect. The time required for this process can be greatly reduced by instigating a training program prepared by experts in equipment maintenance who can pass on their collective knowledge in a structured and efficient manner. In terms of through-life maintenance cost, preventative action is almost always less costly than corrective action. Two of the most prominent symptoms that occur prior to failure in mechanical and electrical equipment are increasing vibration and rising operational temperature. Regular trending and analysis of radial and axial vibration signatures and thermographic/visual inspections of bearings, coils and electrical connections can prove invaluable. The latest developments in operational monitoring can be applied to existing assets and then used to determine the optimal point at which planned maintenance should be conducted.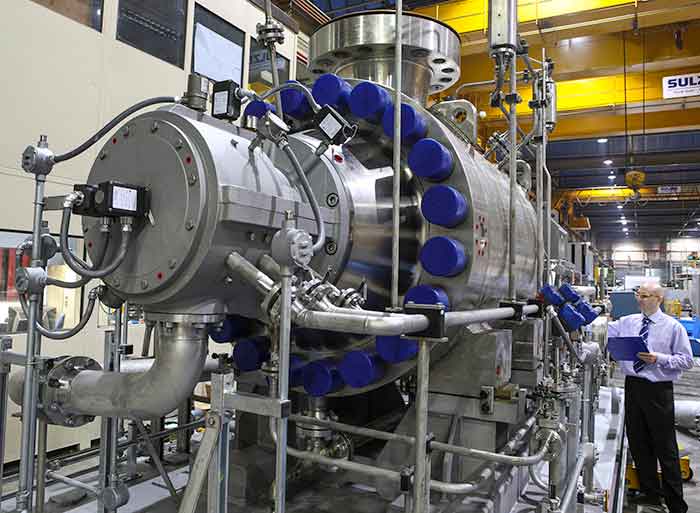