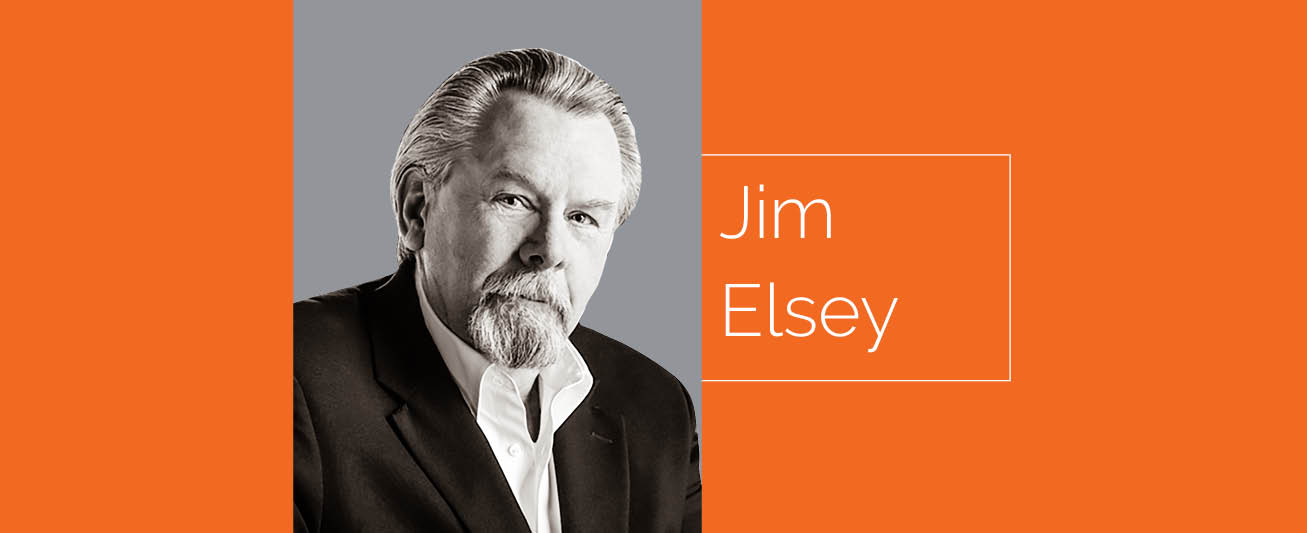
We often think of metals as forever materials, but that notion is not always true. Steps must be taken to protect the metal surface from corroding. The direct cost of corrosion damage in the United States is in excess of $280 billion per year (per ASM International). From the moment a metal surface is laid shiny and bare in the machining process, thermodynamic and kinetic factors will work persistently to destroy it. Water and oxygen, while essential to human life, are not your friends when it comes to the corrosion of metal. Acids, caustics and suspended solids will also join in and dance at the deathwatch.
Preservation 101 for Units Not in Service
Preservation and storage procedures for any type of equipment are required to protect the investment. The corporate policy, discipline and culture required to integrate the procedures and store the items properly is paramount. In my November 2016 column, I outlined the proper preservation steps for pumps and spare parts in storage. For more detailed information, please consult the referenced 2016 column and/or the pump and seal manufacturers.
Protecting Pumps in Service
First note the distinction that rust is a type of corrosion, but not all corrosion is rust. There are at least 10 basic types of corrosion and at least seven types of pitting corrosion alone that will attack metal pump surfaces. In general, corrosion falls into two distinct types: generalized and localized. General corrosion issues are typically easy to figure out and correct, but localized ones can prove more difficult to diagnose and rectify.
The simplest action you can take for external pump protection is to ensure it was painted/coated correctly. Paint or other technical coating systems are a relatively inexpensive, yet efficient, protection system. Painted surfaces that are damaged during shipment, installation or maintenance must be touched up prior to placing the pump in service. Imperfections in the paint system will never get better by themselves and will inevitably lead to corrosion damage. There are special paints for high temperature applications as well as hazardous chemical and marine environments. There are many companies that do not paint metal surfaces on equipment made from alloyed steels.
Keep in mind that the attacking element can come in contact with the pump surface in many ways, including mist/fog/dew/vapors, drips and spray. Understand that water does not have to be present in visible or droplet form; humidity can supply all the water required for corrosion to take place.
Material Selection
An initial and critical decision is determining which material is best for the application. This includes both the wetted parts (impeller, stuffing box and casing) and the remaining components. Keep in mind that even the non-wetted parts will be subjected to a harsh environment.
There are few instructional courses on the subject of proper material selection for industry, but there are several material reference books. I regret that this column is not the proper forum for expansion on the subject because of the specific and unique details required for each in the vast matrix of possible applications, not to mention the liability. I offer references at the column’s end. Other sources for relevant information would include the pump manufacturer and formal networks of other pump users with similar and successful applications such as the Hydraulic Institute or the annual Texas A&M Turbomachinery & Pump Symposium. The Cameron Hydraulic Data Book includes some basic material information. The Pump Handbook has an entire chapter devoted to the subject.
Even the best textbook cannot make the final decision for you. A pump of material choice “X” will work well pumping cool seawater in continuous service but will fail quickly pumping warm seawater in intermittent service. Another pump material “Y” will operate satisfactorily in acid service for many years, but when the liquid velocity is increased or the solution percentage changes even slightly the pump will fail in short order. Some 300 series austenitic stainless steels perform well until chlorides and material stress are present. Other materials work great until subjected to neutron radiation exposure, which sees them become embrittled. In the oil and gas markets, stainless steel will hold up in most applications until the level of H2S (hydrogen sulfide is a colorless chalcogen-hydride gas that smells like rotten eggs) reaches a certain percentage.
Beyond the application issues, there are operational reasons for material failure, such as operating the pump on either extreme of the curve or with insufficient net positive suction head. Finally, there is the rheology of slurry classifications/applications and Newtonian properties which would require a volume of books and many years of experience to explain and predict material wear.
Experienced companies that embrace industry best practices will have a formal material review process where the expected conditions are well defined and the choice of material is considered and evaluated.
Corrosion Allowance & Measurement
Most all pump manufacturers provide a corrosion allowance in the casing thickness. For the American National Standards Institute (ANSI) pumps, the minimum standard is three millimeters (.118 inches).
Corrosion is typically measured in microinches or micrometers per year or in weight loss with units of grams per square meter. For example, the corrosion rate of carbon steel is typically around
20 micrometers per year in an outdoor rural environment away from city and industrial pollution, but the rate increases to more than 100 micrometers per year near the ocean because of the salt atmosphere.
Common Materials for Pump Construction
What follows is a list of common materials used in metallic pump construction. I chose to stay with the most ubiquitous choices. So, we will skip Monel, titanium and nickel aluminum bronze. Not discussed in this column are pumps manufactured with nonmetallic/composite materials.
Cast iron will begin to rust the moment it is exposed to air (oxygen) and water where the chemical process forms iron oxide. The bad news is that the produced iron oxide layer forms a loose flake like structure and does not possess the ability to generate a protective oxide layer or adhere like stainless steel or aluminum does. Yet cast iron can be used in many general applications and will perform well. Cast iron is frequently a low-cost material selection based on the full knowledge that it will be sacrificed in the process.
Bronze casings and impellers were the “stainless steels” of long ago, but even today remain viable in many applications including water, low concentrations of acids (less than 5%) at temperatures below 68 F (20 C), some solvents, most fuels and hydrocarbons.
Carbon steel can often be a next step up from cast iron, especially when looking for added strength, but it also has limited corrosion resistance. Normally the question is not if the steel will corrode, but how fast. The corrosion rate is a function of many factors, but the main ones are temperature and the presence of water and oxygen. It is the lack of chromium in carbon steel that prevents the oxidation layer formed in the corrosion process from being fully functional.
One unique exception is “weathering steel” where the addition of copper, chromium, nickel and other elements in small amounts will produce significant reductions in the corrosion rate. As an example, if you are not familiar with U.S. Steel’s Cor-Ten steel, you should take a few minutes and read up on the product. If you live in western Pennsylvania, you probably already know about this material. The U.S. Steel building in Pittsburgh is clad in Cor-Ten steel. The locals have given the building the affectionate nickname of the Rusty Nail.
Stainless steels in the austenitic 300 series (304, 316 and 317 are the most common) offer a great overall level of corrosion insurance in a multitude of applications. Stainless steel by definition must contain chromium in amounts of more than 10.5%. The chrome reacts with oxygen to form a thin but strong protective layer. The combination of chromium and nickel found in 304 and 316 stainless steel provides a strong resistance to heat, abrasion and corrosion. Unlike iron oxide layers, the chromium oxide layer does not flake and clings uniformly to the steel. The protective layer can fail if the liquid velocity is too high or selective attacking substances are present. As one example, chlorides at certain levels and in some applications will attack the stainless passivation layer. Further, uniform corrosion on stainless steel occurs when exposed to strong acids. Inorganic acids are usually more aggressive than organic acids. Hot alkaline environments will also attack stainless steels.
Duplex and super duplex steels are hybrid steels combine the corrosion resistant characteristics of 300 series stainless with the strength of 400 series steels (austenitic with martensitic). If you require both corrosion resistance and toughness (e.g. suspended solids), a duplex steel like CD4MCu is often a wise choice.
Alloy 20, also known as Carpenter 20 and Incoloy 20, is an austenitic stainless alloy that has high corrosion resistance to sulfuric acid and other aggressive liquids that are too destructive for typical austenitic grades. Alloy 20 contains nickel, chrome, copper and molybdenum similar to 300 series steels, but one key factor is the presence of niobium that precludes or mitigates intergranular corrosion.
Hastelloy comes in various grades and offers extreme corrosion resistance. Selected grades of this alloy offer excellent resistance to HCl (hydrochloric acid) at most ranges of concentrations (percentage) and temperatures. Hastelloy also stands up well to sulfuric, chloride, hydrogen, acetic and phosphoric acids. Several Hastelloy grades, if solution-annealed, can work efficiently in high level hydrogen sulfide environments. In the selection process, you must match the best material grade to the product you are pumping.
Your pumps are constantly subjected to corrosion both internally and externally, whether they are operating or not. Protect your investment via wise material choices at the beginning and receive years and even decades of reliable service.
A wise and practical step is to utilize stainless steel or higher alloys materials where applicable. This decision will yield a significant return on investment.
References
- Chemical Resistance Guide for Metals and Alloys…Compass Publications
- Material Selection for the Chemical Process Industries… C.P. Dillon
- ASM Handbook volume 13A Corrosion Fundamentals Testing and Protection Corrosion Basics by Pierre R. Roberge
- EN380 Naval Materials Science and Engineering Course, U.S. Naval Academy
Technical library resources:
- NACE (National Association of Corrosion Engineers) recently reorganized as AMPP (The Association for Materials Protection and Performance) ampp.org/home
- ASM International (formerly known as The American Society for Metals) asminternational.org