Material of construction, environmental conditions and IP ratings should be considered to maintain operating efficiency.
05/27/2014
Pressure sensors are used in pumps to measure water pressurization and as part of monitoring and control systems. Typically, an off-the-shelf pressure sensor will not survive application-specific operating conditions. Environmental conditions can also cause standard pressure sensors to fail. To ensure that pressure sensors maintain the operating efficiency of water pumps while minimizing service calls, several factors should be considered when specifying a sensor for pump systems in water service.
Media Compatible Materials
Pressure sensors used in pumps will contact water with varying pH levels and quality depending on water purification processes and added chemicals. Many new oil and gas fields also produce some levels of hydrogen sulfide (H2S) and salt water that must be pumped and stored in tanks prior to discharge. Pressure sensors must be able to work reliably in these elements without failure. Units constructed from standard materials using austenitic steels (including 304 and 316) and ferritic steels (such as 13-8PH, 15-4PH and 17-4PH) can handle all types of water. However, these materials may not be sufficient to prevent common corrosion—such as pitting, crevices, stress cracking, intergranular corrosion and galvanic corrosion.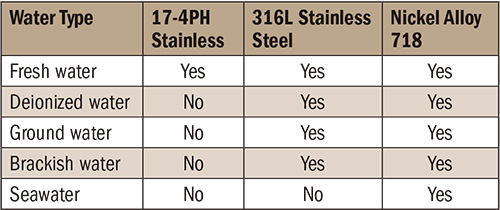
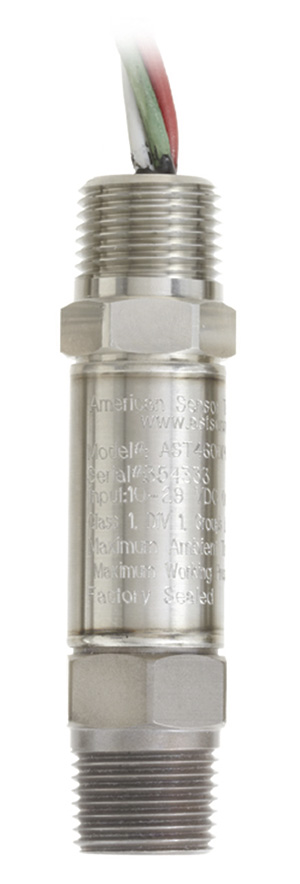
Operating Environment
Depending on the pump system’s location, pressure sensors may be exposed to climate extremes—such as in Canada and Alaska, where the temperature often falls to -60 F (-50 C), or in Texas, where they will experience extreme heat and humidity. Pressure sensor threads must seal the media from low to high temperatures with a dry seal—such as national pipe taper (NPT) or a metal-to-metal conical seal. NPT threads can be used up to 10,000 psi (700 bar). However, caution must be taken against incorrect installation torque. Beyond 10,000 psi, an NPT thread must be avoided, and the units must be specified with a metal-to-metal seal. Pressure transducers used on outdoor applications must withstand ambient temperature and rain, snow, icing and dirt. Corona discharge from lightning strikes and electromagnetic interference from electrical polluters—such as wireless radio systems, valves and variable drive motor systems—can cause stray voltages and leakage currents to be transmitted through pipes. This can often disrupt sensor operation. Pressure sensors with custom electronics and a sensing element to withstand 500 volts of direct current isolation work best in these extreme electrical conditions (see Image 1).Sealed Construction
Rain, ice, dust and pressure washers can cause water to seep into sensor housings, causing electronics to short. Sealed gauge reference pressure sensors protect electronics from these conditions. Ingress Protection (IP) ratings can help end users understand the environment in which the sensor will survive—including high pressure, washdown or submersion. In certain cases, a submersible pressure transducer will be specified. The area in which the sensor is threaded and installed could become flooded, requiring that the electronics be protected from submersion.Water Hammer
The opening and closing of system valves, such as solenoids, can cause a pressure transient within a water pump above the measurement range in a shockwave. An internal welded restrictor plug reduces the inside diameter of the sensor’s pressure port so that when the pressure spike hits the face of the plug, it feeds through the hole at a slower pace, dampening pressure spikes before reaching the sensor’s diaphragm. The restrictor plug, commonly called a snubber, also reduces the overall length, cost and potential leak points in the system. In this configuration, the liquid must be free of dirt, lint, iron filings, sand and grit to avoid clogging the plug. For some pressure sensing technologies—such as thin film, bonded metal foil strain gauge and capacitive with very low signal output—this is the only way to limit the diaphragm travel. Therefore, the user must install a mesh filter in front of the snubber.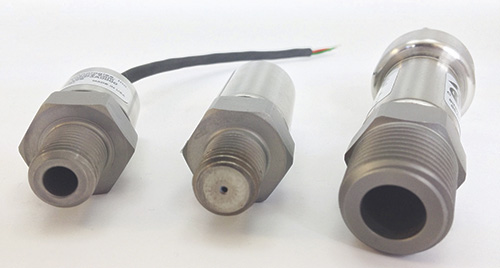