Pumps are the heart of fluid-transfer operations. Unexpected failure can devastate production and profits. Operators in the industrial-manufacturing realm have been looking for ways to see into the future, to know when, how and why a pump will need to be serviced before a catastrophic breakdown will bring the production process to a halt. Over the years, manufacturers have worked to improve pump reliability and have developed tools to monitor pump performance and health. Sometimes these tools result in little more than a “check engine light” scenario. There is a problem, so what is the next step? Evolving technology allows the pump and driving motor to be monitored around the clock via continuous cloud connectivity. This article illustrates how the technology works and how it can optimize pump performance, reliability, and cost of operation and maintenance.
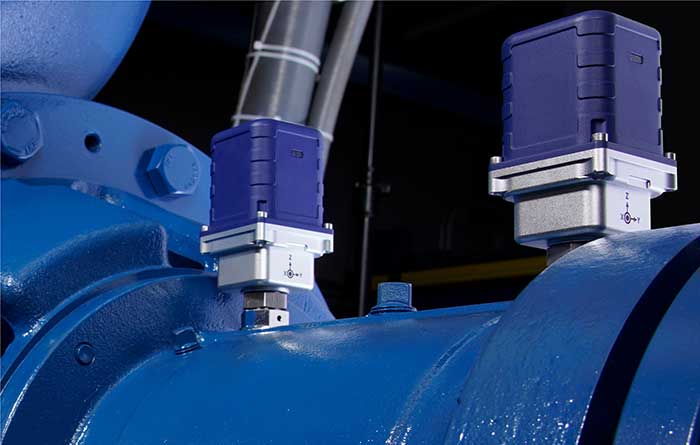
The Challenge
In most industrial production and processing plants, unexpected failures can be devastating to the production schedule and, by extension, the operator’s bottom line. There are many negatives associated with pump failures:- disrupted production
- batch failures
- excessive downtime
- costly repairs
- costs for new parts and shipping
- costs for service calls, which can include overtime
- lost or compromised revenue
Current Industry Solutions
Facilities have focused on deploying predictive maintenance (PdM) techniques as a solution to increasing production reliability since the 1990s. In the pump industry, PdM uses techniques such as vibration and temperature monitoring to observe a pump’s performance and health during operation. Early on, PdM was a manual process where measurements were taken by hand-held devices, then documented and analyzed. This process relied on vibration experts to interpret the data.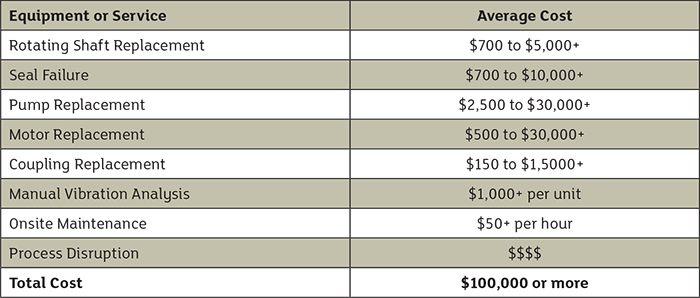
- Complete machine monitoring. Most technologies are designed to monitor the pump only, even though the pump is only part of the machine.
- Not true remote monitoring. The majority of “remote” monitoring technologies require technicians to be within Bluetooth range of the pump with a mobile device to accurately gather the data.
- No real-time data. Due to the remote-monitoring restrictions, this eliminates real-time data, as well as 24/7 monitoring.
- Alarm only. The data collected by other diagnostic technologies is equivalent to an alert only with no clear level of urgency.
- No repair guidance. While there is an alert to signify a problem, the root cause is not identified nor any repair guidance offered.
- No single-source data collection. It is cumbersome to collect the data on all machines within the plant in one easy-to-reference and accessible location.
The Solution
There are predictive monitoring systems that can identify failure modes and provide actionable repair guidance, monitoring the pump and motor around the clock with Wi-Fi or cellular access. Two sensors are installed on the pump, and two are installed on the motor. The sensors work in unison to predict the health of the pump and motor. This capability allows a diagnostic reading and analysis of a number of performance parameters for the pump, motor, coupling and foundation, including:- Tri-axial vibration reading: The equipment’s vibration signature produces details regarding its health and can be used to identify impending bearing failure, misalignment, cavitation levels, pipe strain and more.
- Temperature reading: Elevated operational temperatures are a sure indication of upcoming bearing failure, inadequate bearing lubrication and other causes of issues. Studying temperature trends can help the operator detect thermal-fault signatures, which will provide additional insight into when potential breakdowns may occur.
- Electromagnetic reading: Sensors are able to monitor the motor’s true revolutions per minute (rpm) and proactively diagnose electrical faults through the electromagnetic tools.