Manufacturers use high-solids coatings across a multitude of finishing and painting applications in a variety of sectors. High- solids coatings are an ideal method to create consistent layers of coating, each with a precise thickness. Coating application systems are used to facilitate these applications, and at the heart of many systems is a piston pump. The piston pumps work with lines, regulators, filters, nozzles and other in-line components to apply high-solids coatings to the work area in shipbuilding, bridge building, automotive, aviation and general manufacturing. Because of the harshness of the materials in high-solids coatings, abrasion-resistance, pump speed and pump size are factors to evaluate when configuring the pump for the application system.
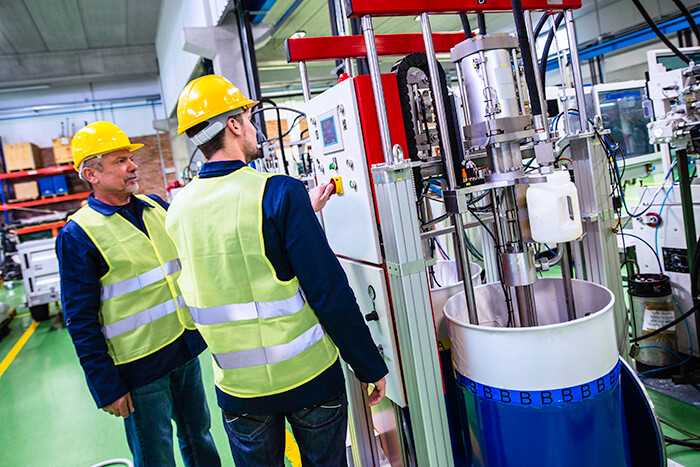