Any drilling operations site that wants to optimize its process and preserve its equipment is well aware of its mud. Drilling fluid (what the layperson calls mud) is a vital part of the drilling process. Drilling mud is important for downhole drilling; cooling and lubricating the bit, removing debris from the well, controlling formation pressures and maintaining wellbore stability. If a project is going to succeed, the drilling fluid system must be monitored, maintained and maximized. Go to any drilling site and someone there is keeping an eye on the mud. There is no shortage of equipment, instruments and technologies that are used to maintain the drilling fluid process. Depending on site needs, drilling professionals might opt for flow meters, shakers, additives, centrifuges, degassers and any number of other technologies to monitor mud movement. The process can be further maximized for efficiency by using process instrumentation in the different phases of the mud system.
Radiometric Sensors
Radiometric sensors are a popular choice for pipeline mud flow. Maintaining the correct density profile of the mud traveling through the pipeline and ending down hole is important in maintaining stability and controlling formation pressures. The fluid also needs to be the correct density to both travel back up the annulus and carry away drilling debris. As a well is drilled, underground land formations change. That is just one of many factors that may affect the internal well pressure. Continuous monitoring of the conditions inside the wellbore and the characteristics of the drilling fluid must be maintained to ensure well integrity. For an accurate account of those characteristics, users often trust radiometric density detectors. The chief advantage of radiometric systems is that they operate without contacting the measured product. In a pipeline application, a secure source holder is mounted on one side of the pipe, and a detector is mounted on the other. The detector measures radioactive energy; the more energy it reads, the lower the inferred mud density. This noncontact design prevents the wear suffered by contact instruments abused by pipeline fluid. Additionally, because the system measures energy and not mud, the instruments do not need recalibration or adjustment to measure changing product. Radiometric sensors also offer durability in extreme heat and other adverse conditions. These instruments are rugged. Radiometric systems do have their challenges. Efforts to meet the standards of regulatory bodies can prolong the buying cycle, and radiometric instruments are more expensive than other density devices.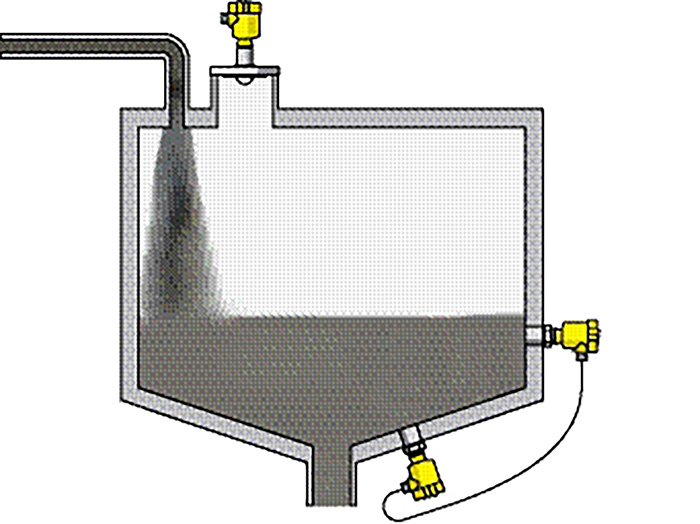
Through-Air Radar
Let us move from the pipeline to the drilling fluid storage tank. Accurate level measurement of drilling fluid inventory level and the level of additives and other materials ensures drilling sites maintain adequate mixtures. When it comes to liquid level measurement, through-air radar is the leading technology. Through-air radar is noncontact and free from damage inflicted by corrosive products. These instruments are durable in challenging conditions and many models are sensitive enough to measure products of any chemical composition. Dielectric constant does not matter anymore. These sensors can measure virtually anything. If users considered through-air radar for level measurement and passed, now is the time to reevaluate radar, since the technology has advanced significantly in the last two years. Several process instrumentation providers now offer radar sensors that operate with a transmission frequency of 80 gigahertz (GHz), an increase from earlier 26 GHz models. Higher transmission frequency allows for a narrower, more focused microwave beam. This focus is helpful in drilling fluid storage because the beam misses internal obstructions inside the tank that created false signals for previous-generation radar sensors. Plus, even when a tank has an odd shape, there is always a good place to mount an 80 GHz radar sensor because of focus. Through-air radar can also be used for level measurement in the shaker. If a user is interested in installing a radar detector for liquid level, he or she should keep this in mind: in applications where foaming is prevalent, guided wave radar (GWR) is preferable to through-air radar. GWR sensors emit highly concentrated radar pulses that give a more precise reading through foam. Guided wave detectors are also recommended for applications that use a stilling well because GWR signals travel a defined path and will not contact the well walls.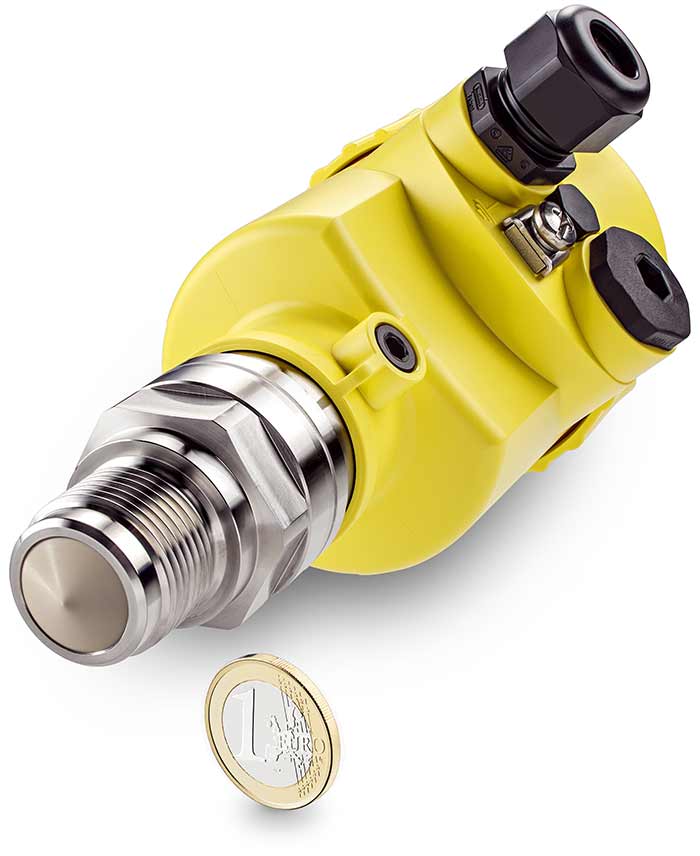