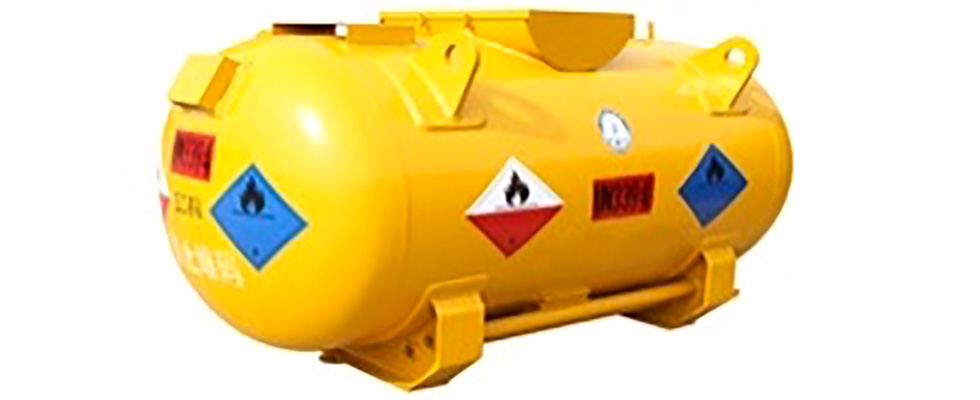
Many people have never heard of triethylaluminium (TEAL), but it plays a key role in the manufacturing of products that people see and touch every day. TEAL is an organoaluminium (carbon and aluminum) compound that is used to make the polymers needed for high and low density plastics, rubber, pharmaceuticals, semiconductors and the “fatty-alcohols” found in detergents and hand sanitizers.
Polymers work by combining individual molecules (or monomers) into larger chains that can be used to make products. In organic polymers, the backbone of these chains are carbon and organometallic compounds, such as TEAL. These compounds provide the carbon needed for the polymerization reaction. In the manufacturing of some of the most common plastics, TEAL is combined with titanium tetrachloride to create the Ziegler-Natta catalyst. This is the catalyst needed to initiate the chemical reactions that lead to the polymerization of olefins with high linearity, which yields both polyethylene and polypropylene.

Any plant storing or processing TEAL is mindful of the chemical’s volatile nature. TEAL is pyrophoric, which means it ignites upon exposure to air. In fact, the chemical’s powerful reaction with cryogenic liquid oxygen is one of the reasons it is used as a first-stage rocket ignitor for the SpaceX program. Suffice it to say: Extreme caution must be exercised when handling this substance. For the plastics manufacturers pumping this chemical every day, only a pump specifically designed for this application will do. Great care must be taken in order to ensure that it is never exposed to air during the catalyst process.

Accuracy matters when it comes to selecting pumps for TEAL applications. Each chemical process follows a specific recipe. Injecting too much or too little of the key ingredients fails to produce the desired result. Metering pumps that can specifically inject the required amount of chemical (within +/- 0.5 percent accuracy) are a preferred choice for TEAL applications by chemical manufacturers.

With respect to flow and pressure, TEAL is typically dosed at volumes less than 50 gallons per hour (gph), and at pressures less than 500 pounds per square inch gauge (psig), which is within the ranges of most metering pumps. A critical part of the polymerization process is full American Petroleum Institute (API) 675 compliance, accuracy and reliability. Pumps constructed with a 316 stainless liquid end, 316 LSS ball valves and valve seats, and a polytetrafluoroethylene (PTFE) diaphragm are preferred for TEAL to provide longevity with this hazardous chemical.
Safety & Reliability
Hydraulically actuated diaphragm (HAD) metering pumps can run reliably for decades with long mean time between repair (MTBR) intervals. This is primarily due to the pump’s design. Inside the liquid end, the volume and pressure of the hydraulic fluid on one side of the diaphragm equals the pressure of the process fluid on the other side, keeping the diaphragm equally balanced between the two fluids. The pump’s piston never touches the diaphragm—it moves hydraulic fluid into the diaphragm, which flexes it enough to move the required volume of process fluid. This design eliminates stress on the diaphragm and can last longer.
While longevity is important, leak-free reliability must also be prioritized. Metering pumps for TEAL applications should feature monoblock check valves that minimize potential leak paths. External 4-bolt tie-bars offer stronger and more reliable connections to piping. Over a long time period, external vibrations from piping connections can cause leaks and major problems for pumps.
PTFE diaphragms have a proven track record in pumping TEAL. These pumps should feature double diaphragms with leak detection capabilities, such as a pressure gauge or a combination of a pressure gauge and a switch to warn of a potential issue.
As a third layer of defense, nitrogen blanketing in the hydraulic housing and in the gear box will prevent pyrophoric liquids from exposure to air.
Maintenance
The check valves on a metering pump working 365 days a year at 150 strokes per minute will open and close more than 70 million times per year. The parts needed to replace a pump’s check valves are provided in standard maintenance or KOP (Keep on Pumping) kits, which also include diaphragms, O-rings and seals. Changing the pump’s hydraulic fluid should also be included as part of preventative maintenance.

Demand for plastics for personal protective equipment (PPE), combined with low oil prices reducing feedstock costs, means increased production and the need to meter volatile catalysts such as TEAL.