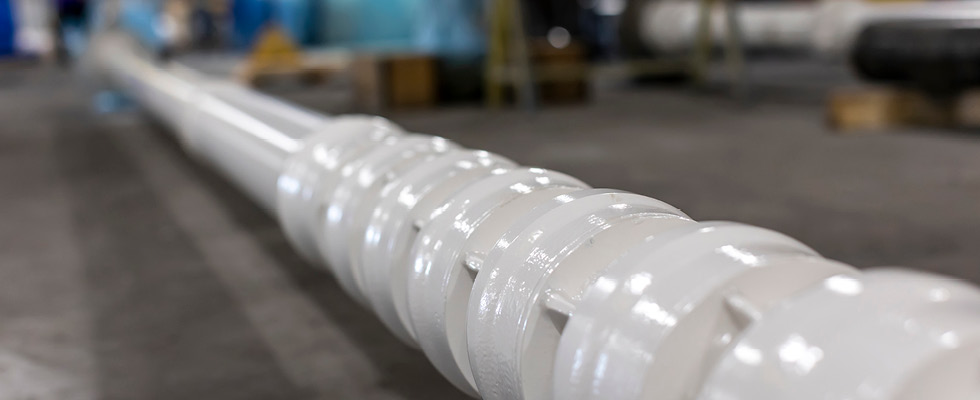
The mining and mineral processing industry operates within an environment characterized by rigorous demands on equipment performance, reliability and durability. Critical equipment failures, such as with pumps, have the potential to bring about the complete shutdown of a plant, leading to substantial financial implications for operators in terms of downtime, repairs and lost productivity. Consequently, plant operators proactively seek supplier partners who can deliver robust solutions that not only enhance overall productivity and profitability, but also ensure the uninterrupted and efficient operations of their facilities.
Dewatering plays a crucial role in mining and mineral processing. In mining, it is vital to minimize the risks of flooding, erosion, collapses and toxicity to ensure safe and efficient operations.
The optimal mine dewatering methods vary depending on operating conditions, but generally, they involve a combination of sump pumping, where water is collected in pits and pumped out, and wellpoint systems to lower groundwater levels. In some cases, horizontal drainage systems are also effective.
Pump manufacturers face several challenges when it comes to dewatering. These include adjusting to the volume
and rate of the water inflow, as well as dealing with variations in water quality along with debris and/or acidic fluids’ content. For mine dewatering, the layout and depth of the mine itself also affect the complexity of the process and the required pumping solutions.
Centrifugal vertical turbine pumps are widely used for mine and mineral process dewatering due to their flexibility, ability to operate in an open pit, compact footprint, capacity to handle large volumes of water and durability in harsh mining environments. Submersible vertical pumps are also used and often have lower installation costs with a trade-off against operating and maintenance costs.
Recent technological advancements in dewatering pumps include the development of more energy-efficient solutions, remote monitoring systems for real-time data analysis and predictive maintenance and improvements in coatings and materials, such as titanium, to enhance durability in corrosive environments. Composite wear parts can also help in contaminated services.
One OEM’s user developed a new copper leaching process designed to increase yield from ore using an acidic solution with a pH of approximately 1.2 and a high level of chlorides. The user reached out to the OEM for vertical turbine pumps with durable wear and corrosion resistance for the project. The combination of low pH and high chloride levels necessitated the use of titanium for pump construction.
The OEM conducted research and development studies on material characteristics to balance the cost and suitability of different titanium grades. It sourced and qualified new suppliers and tested and inspected first-article castings before production. It also worked with the user to ensure proper design and material grade selection for various pump components and created discharge heads to fit existing motors.
Efficiency drove the selection of the hydraulics. Additionally, managing tip speed was a critical concern to extend the service life of the units, which operate in highly demanding conditions. The OEM worked closely with the user to evaluate various design concepts and find the right balance between costs and long-term reliability. This process involved considering the pumps’ life cycle costs as well as installation and groundwork expenses.
At the end of the production stage, the multistage pumps underwent rigorous performance testing according to industry standards using calibrated lab drivers.
The same OEM also recently provided vertical turbine pump solutions for mineral processing in a copper mine in South America. The mine concentrator plant’s tonnage increase had led to premature damage and shortened the life of the vertical turbine pump units installed on intake structures in a process water application of the reclaimed pond system, causing operational disruptions and increased maintenance costs. The OEM replaced the vertical turbine pumps with vertical turbine solids pumps engineered to pump fluids with solid concentrations up to 10% by weight without changing the original motor and with minimal piping or foundation modifications. This pump replacement extended the pumps’ wear life from an average of 300 hours to over 1,000 hours and tripled the mean time between failures (MTBF).
The mining and mineral processing industry operates in a challenging environment characterized by demanding conditions and complex processes. This underscores the increasing significance of fostering collaborative, partnership-type relationships between plant operators and their equipment and service suppliers, such as pump manufacturers. Establishing such expert collaborations has become essential for operators to effectively address project challenges and attain plant efficiency, reliability and sustainability goals, including the management of water.