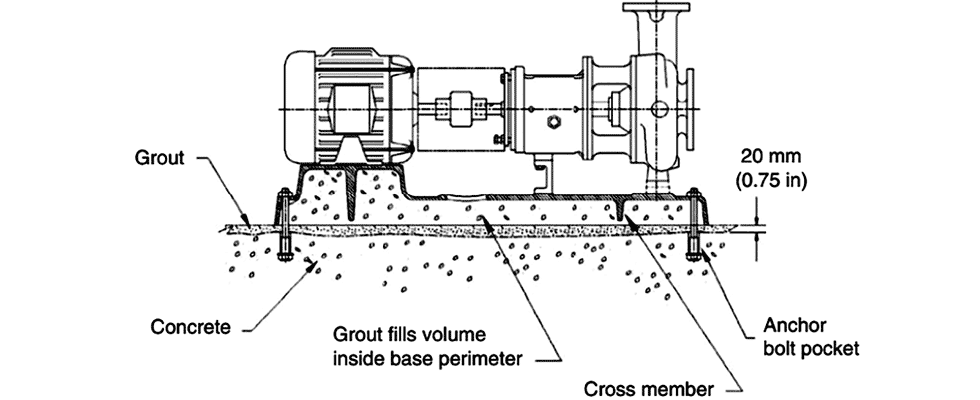
Like most industrial and manufacturing industries, the pumping and fluid handling industry is facing workforce challenges. This includes a challenge to attract young professionals to the manufacturing, construction and municipal industries. These industries have experienced workforces that are moving toward retirement and taking years of industry knowledge with them.
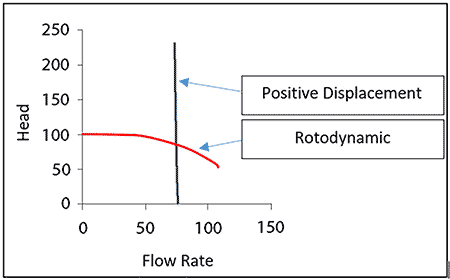
This challenge requires the industry to communicate the importance of fluid handling to everyday life and how a career provides an opportunity to work in a secure industry—while impacting society by providing equipment and services that are integral to so much of what we enjoy.
This is no small task, and it is only the first step. Once new talent is attracted, companies have the daunting task of educating and training employees on their processes, products they manufacture or services they deliver. However, first, the fundamentals must be covered. This article takes a first crack at fundamental knowledge topics that cut across the fluid handling industry, while understanding there will be differing specifics and knowledge levels needed for varying positions. The end goal is to design and build reliable and efficient systems that meet their intended purpose. To achieve this goal, the manufacturers, system designers, construction contractors and owners must have a common and fundamental understanding of the topics listed within this article.
Pump Systems
Understanding the type of pump system and its needs is important because it defines the hydraulic needs and the design of the pumping equipment. Systems could be open to atmospheric pressure or not, be friction or static head dominated, have variable or constant demand, be clean or contain solids, and could be water based or have some other physical properties. Each of these fundamental considerations will be important to the pump system design, installation, control and selection of the pump(s).
Pump Types, Design & Application Fundamentals
Pumps come in many shapes and sizes to meet all different system and fluid demands. It is important to understand the commonality and differences in the technologies.
The most fundamental division is rotodynamic versus positive displacement. Rotodynamic pumps have a rotating impeller/propeller/rotor that rotates in a casing/collector. Positive displacement pumps can be rotary type, which have meshing components (for example gears and screws) or reciprocating types, which have pistons, plungers or diaphragms that displace the liquid. The rotodynamic types increase the velocity of the liquid from the inlet to the outlet of the impeller, and positive displacement pumps trap and move a specific volume of liquid with every rotation of the pump shaft. This technology difference results in rotodynamic pumps operating at some maximum pressure that is related to the rotational velocity and positive displacement pumps operating at almost any pressure to deliver the liquid (Image 1).
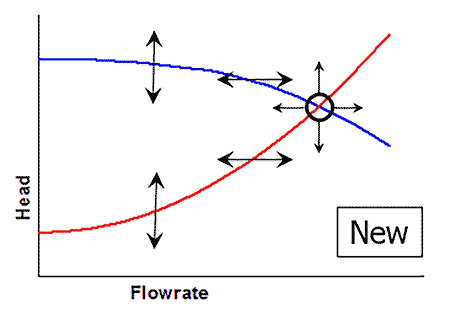
This fundamental difference needs to be understood because it will affect the applications where each is best suited. Beyond this broad technology difference, there are countless variations in design, orientation and installation that are applied to meet specific market and application needs. A basic understanding of the design variations, benefits and limitations of the design variation, as well as general application considerations, are important for all.
Inlet Pressure & Liquid Vapor Pressure
Head and pressure have a known relationship based on the liquid density. For water at standard density, one pound per square inch (psi) is equivalent to 2.31 feet (ft). For pump systems to operate as designed, a certain amount of head (pressure) must be supplied to the pump inlet. If not, the pressure can drop below the liquid vapor pressure and vaporize in the pump.
If severe enough, this can lead to performance reductions and premature failure. Manufacturers test pumps and publish a term called net positive suction head required (NPSHr), and the pump system must have net positive suction head available (NPSHa) with some recommended margin above the NPSHr.
Head, Flow Rate & Power Consumption (Pump Curve)
For people new to the industry, the term head may not be well known. The performance of pumps is generally represented by plotting pump total head as a function of flow rate, based on water testing. Rotodynamic pumps generally have a wide flow range that is inversely related to head (higher head at lower flow and lower head at higher flow), but positive displacement pumps have a narrower flow range as a function of head (Image 1). Head is plotted on rotodynamic pump curves instead of pressure because it is not dependent on the fluid properties.
The total head, flow rate, liquid density and pumping equipment efficiency will govern the system power draw. Since testing is generally done on water, it is important to have a general understanding of how the viscosity of the liquid will change a pump’s performance. For rotodynamic pumps, viscosity can reduce the flow rate, head and efficiency, but for positive displacement pumps, the same relationship will not exist and to a limit could increase the efficiency.
Pump & System Interaction
Pump systems also have curves. The system head as a function of flow rate (system curve) will dictate the pump hydraulic selection and actual system operating flow and head (Image 2). This means that a pump designed to operate at 100 gallons per minute (gpm) at 100 ft of head will only operate at that point if the system head curve is also 100 ft at 100 gpm.
In the potential new system in Image 2, the operating point could move in any direction if the pump curve or system curve is changed. Understanding the system head curve and how it can vary is perhaps the most important item to understand for proper pump selection, control and operation.
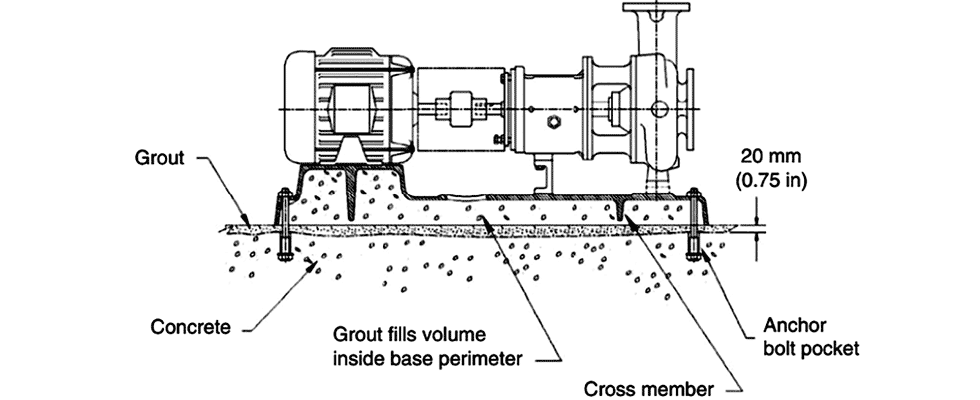
Varying System Operation
Most pump systems will have variable operating conditions that the pump and controls will need to account for.
Strategies can include:
on/off operation
throttling flow (increasing pressure at the pump)
bypassing flow before entering the system
varying pump speed
operating multiple pumps in parallel or series
Understanding system requirements and how system variables are interdependent enables reliable and efficient operation.
Pump Accessories
Initially when we think of pumps, it may just be the parts that move the liquid, but there are many other important components that designers and owners should understand. Pumps often include:
- static and dynamic seals
- bearings and bushings
- drive train components (such as couplings and gears)
- lubrication and other support systems
- baseplates
- drivers (such as electric motors and engines)
- variable speed drives
- instrumentation
All accessories need to be considered in the design and application. If any component is not designed, installed, operated or maintained properly, the entire system can fail.
Pump Selection
Pump selection is dependent on everything listed in this article. It requires considering the system curve, the system variability and operating range, design flow and head, NPSHa, fluid properties, methods to vary the system operation and other market/application specific needs. Pump selection is often a tradeoff of considerations, but the driving factor should be lowest life cycle cost. Energy consumption and maintenance costs are often the largest components of the life cycle cost and should be given proper consideration.
Installation, Commissioning & Maintenance
There are many individual components that comprise the pump. Understanding the installation requirements for all the components and how they can affect reliable and efficient operation is important (Image 3). For example, performance, efficiency and reliability will not be as expected if the inlet piping or intake is not designed to provide uniform flow to the pump inlet. Reliability can be compromised due to many installation-related items of the components or pump itself.
Some items to consider and understand are pump nozzle loads, alignment, foundation integrity, anchors and bolting, support systems for seals and bearings, and lubrication. Following the installation, it is important to follow proper startup procedures and verify the support systems and pump system operation. This can include varying system operation and the number of pumps operating, as well as documenting flows, pressures, powers, temperatures or other important system parameters. It may also include adjusting the system to operate as designed.
Pump System Analysis of Common Operating Problems
Most people in the industry have been faced with questions such as:
- Why is the flow rate too high/low?
- Why is the pressure too high/low?
- Why is the bearing failing?
- Why is the seal leaking?
- Why is the pump vibrating?
The answers to these questions can range from simple to complex, but in most cases, considering the fundamentals will lead users in the right direction. The installation, operation and maintenance manual will often include a table that lists a common problem and potential causes. For example, if we want to understand why flow is too low, it could be related to:
- clogged inlet
- system inlet design
- insufficient NPSHa
- system head is higher than expected
- viscosity is higher than expected
- the pump parts are worn
- internal gaps are set incorrectly
- the pump speed is lower than expected
- the motor is turning wrong direction
- too few pumps are running
- a control valve clogged or not opening
And, there are likely additional causes. The point of this list is to illustrate that a typical problem can be due to many reasons with them all being related—the system design, pump design, pump accessories, pump and system interaction, control, installation, operation or maintenance. To get to the root of a problem, reviewing the fundamentals is important to answer why it is occurring.
A pump design engineer, test stand manager, facility maintenance manager and system operator will all need to have different and more detailed training and knowledge related to their positions. The areas outlined within this article are identified as providing value across most positions within the pump and fluid handling industry. A core body of knowledge and training program that covers these areas can then be leveraged by the industry so that employers can focus on building on the core knowledge.