Last of Two Parts
05/30/2014
Last of two parts.
In my April 2014 column in Pumps & Systems, I quizzed readers, asking if the pump suction behavior depended on the discharge (system) side of a pump. This quiz also referenced a video that can be viewed at www.pump-magazine.com and go to Q&A, Question 120.
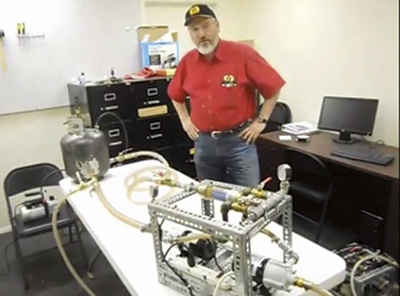
The Best Reader Answer
The best answer received was from Jim Gagnon, P.E., senior engineer, from CH2M HILL in Cincinnati, Ohio.Gagnon’s Response
I watched the YouTube video that you posted, and I think I have the solution. In the first experiment, the pumped flow rate decreased when you throttled the suction-side valve because closing the valve added dynamic head to the system. The result is that the operating point moved to the left on the pump curve, and the flow rate decreased.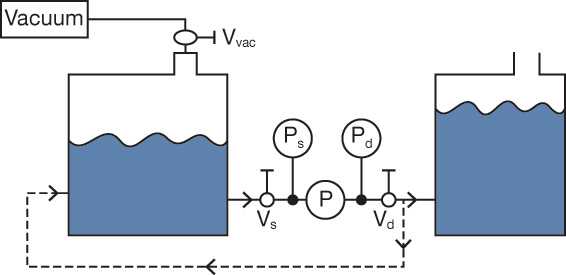
Nelik’s Response
You are correct, Jim! Normal flow control of the pump/system is accomplished by closing or opening the discharge side valve—almost never by its suction side. Closure of the valve increases the losses across the discharge valve, and its opening decreases the losses. New system curves are created that intersect the pump curve at new operating points (see Figure 2).
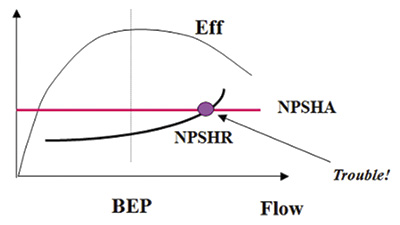
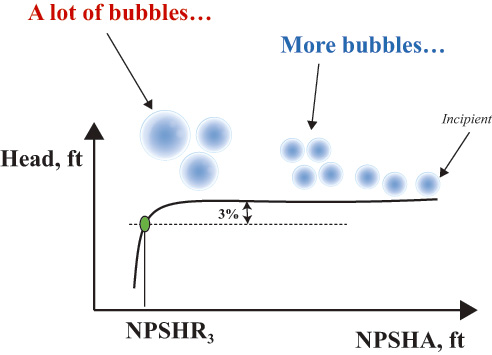