HI Pump FAQs
Hydraulic Institute
01/03/2017
Q. How are vertical pumps used in power generation applications? A. Vertical pumps offer design flexibility that is not usually available with other pump types. The Hydraulic Institute categorized 10 unique vertically suspended (VS) pump types as shown in Figure 2.1.3. With the exception of VS 8, all VS-type pumps are suspended with the pumping element below grade, submerged in the pumped liquid. Vertically suspended pumps provide unique utility that dictates how and when they are used.
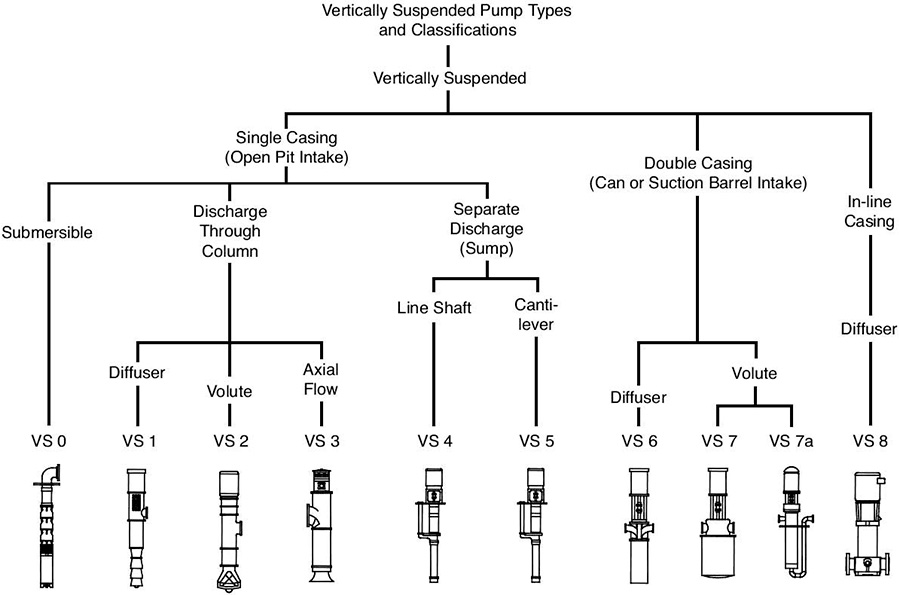
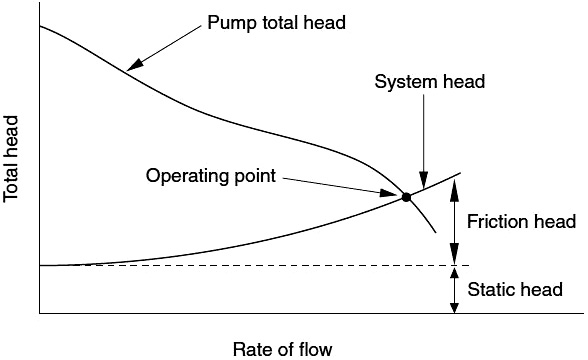

See other HI Pump FAQs articles here.