Pump manufacturers should prepare for the changes that the impending DOE pump efficiency regulations will bring, including possible design improvements.
03/12/2014
This is the last part of a three-part series that discusses the upcoming U.S. Department of Energy (DOE) pump efficiency regulations and how the Hydraulic Institute (HI) is working with HI members, the DOE and other groups to reduce the burden on U.S. pump manufacturers, while supporting DOE efforts to achieve energy savings and efficiency improvements in the marketplace. Click here to view the first article of the series.
Extended Product Approach
Europump, HI’s sister organization in the EU, first developed the term extended product (EP) to define the packaging of a pump, motor, driver and control technologies. Efforts continue on both sides of the Atlantic to develop the standards, data and labeling schemes that will guide the market-based adoption of this approach. Meetings between Europump, HI and other organizations continue in this regard. Potential energy savings achieved through optimized pumping systems exceed what can be achieved by redesigning and modestly improving pump efficiency. As documented in the DOE studies and pump system energy audits, pumps rarely operate at their best efficiency point for the specified head and flow. Figure 2 illustrates the concept of an EP with the pump, motor, driver and feedback/controls as a product package.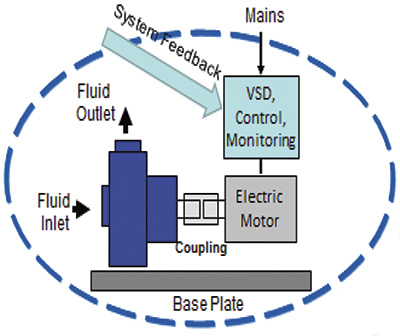
Pump Efficiency Improvements
Pump companies tracking this process since its inception have begun to identify the range of their products that may be subject to DOE rulemaking and are evaluating where they stand versus their competitors in the marketplace. Legacy lines are being evaluated for opportunities to improve efficiency. Work is underway on product redesigns by manufacturers who anticipate that some of their product lines may not meet a certain MEI value, assuming that this is the approach that the DOE ultimately adopts. Pump companies that have not been tracking this issue closely must become familiar with the potential regulatory impact of the DOE rulemaking. All pump original equipment manufacturers (OEMs) affected by these new regulations should decide the impact that the regulations will have on their product lines. While HI has consistently offered its best technical input and advocated for a sensible U.S. pump efficiency rulemaking, the outcome is far from certain. If the regulations in the EU are any indication of U.S. regulations, the EU government has effectively eliminated 10 percent of covered products (an MEI = 0.1) effective Jan. 1, 2013, and will eliminate 40 percent of covered products (an MEI = 0.4) effective Jan. 1, 2015. Will the U.S. DOE act in a similar manner? In a presentation to HI members on Oct. 25, 2013, during the HI fall meeting in Baltimore, the top two DOE officials made it clear that the DOE is not authorized to approve a staged implementation of efficiency levels. Therefore, if the DOE follows an MEI approach, what outcome should the pump industry anticipate? Until either the traditional rulemaking is finalized or the negotiated rulemaking reaches a successful conclusion in 2014, no one knows for sure. The traditional and negotiated rulemaking approaches were detailed in Part One, and regular updates from HI are provided at HI meetings and made available at: www.pumps.org/DOERulemaking.HI Committees: Working on Critical Deliverables
In addition to this group, a number of HI committees were formed during the past two years to work on different aspects of the DOE rulemaking. Experts from HI member companies have collaborated, beginning with the HI Pump Efficiency Expert Team (PEET), to advance work that will be fundamental to the DOE rulemaking and end-user understanding of optimizing pumping systems. The committees met in person during the HI annual meeting in Phoenix, Ariz., in early February 2014. The following is a brief summary of the different committees’ work:- HI Pump Test Standard: HI 40.6: While HI pump test standards, particularly ANSI/HI 14.6, are well-known among pump end users, engineering consulting firms, pump OEMs and distributors, the DOE would have to reference its own specific pump test procedure as the foundation of its rulemaking. HI offered to write that standard for the DOE and invited DOE experts as part of the standards-writing team. Unlike the 14.6 standard, the standard that the DOE will adopt will be based on only one test tolerance known as 2B. Documentation created by the HI committee was submitted to the DOE for introduction into its test procedure rulemaking process. A formal public hearing is scheduled for summer 2014, according to the latest schedule published by the DOE.
- MEI Standard: The purpose of the MEI Standard is to develop a method for reducing the energy consumption of pumping systems. The MEI concept takes certain factors into account—including pump type, size (flow rate at BEP), head and specific speed to predict the efficiency cut-off level. The MEI Standard provides a decimal index value (1) indicating an efficiency class.
- Pump Test Lab Approval Program: This committee is developing a pump test laboratory audit and inspection program to approve a pump test laboratory’s ability to test the performance of certain products to applicable HI and other performance test standards. This program will also adhere to the requirements of an international test lab accreditation standard (International Organization for Standardization—ISO—17025). The scope of the committee’s work encompasses all pump test laboratories testing pumps and extended products.
- EP Standard: The EP committee is working on a publication to identify and verify optimized energy usage of extended products, defined as the pump-motor-drive assembly and control. Working collaboratively with its European counterpart, Europump, HI intends to create a standard for the pump/motor assembly and motor control from the perspective of a sub-systems approach (European Extended Product Approach). Focusing on optimizing energy efficiency use of the EP, the standard will likely recommend metrics and minimum standards. Such a standard will help support HI and the pump industry’s advocacy for optimizing pumping system EPs to achieve higher energy savings, rather than by addressing pump-end efficiency alone. Improving the efficiency of EPs can significantly benefit end-user economics and the environment. The HI EP document will address rotodynamic pump systems EPs that only cover designs for clean water, and most likely, will be consistent with the anticipated DOE rulemaking.
- Pump Systems Energy Optimization Standard: This committee is creating a standard for the evaluation of energy usage in pump systems that provide the user or system designer with a collection of tools and metrics for the development of energy efficient pump systems. This standard is intended to facilitate the optimization of pumping systems to achieve higher energy savings rather than address pump efficiency alone. The scope of the standard is intended to be used as a tool in the design and retrofitting of pump systems to optimize energy efficiency and reduce life cycle costs.
- EP & Pump Labeling Initiatives: HI recently joined a collaborative effort on EP labeling, organized by the ACEEE, to work with electric power utilities, energy efficiency advocates and other trade allies to develop new concepts for pump and extended product labeling to recognize higher efficiency products or EPs.