Correct equipment selection and application saved an aluminum producer $36,000.
03/06/2015
The major focus of any industrial distributor should be maintenance. The distributor's personnel work daily with maintenance mechanics, plant engineers, maintenance managers and all those working to keep plants running. The work of these key people affects the overall efficiency, reliability and longevity of their liquid transfer process equipment and systems. These employees have often inherited the equipment, and their responsibility is to keep it working day in and day out. While this may seem simple, maintenance must be approached from the perspective of the plant floor—not just from the chair of the design engineer. The best designs are a combination of thoughts from the technician to the senior engineer.
Getting Started
The first step to achieving optimum efficiency is to define it. Is it simply energy savings? Or is it reliability, uptime, product longevity, reduced maintenance time and costs, and product standardization? Efficiency consists of all of these elements and more. To realize optimal performance from the plant floor, all personnel must understand five key factors affecting efficiency.1. The equipment must be correct for the application.
In the middle of the night during the stress of a breakdown, the maintenance employee will do what he must to get the equipment operational—including using something other than the original part. Changes of this nature are surprisingly common. Even though changes are made daily, they are not always recorded, and best paperwork practices are not always followed. Distributors must rely on a user's information to supply the correct product. If accurate records are not kept, the possibility of receiving the wrong product increases. For these reasons, keeping accurate records is critical. Many pumps are on their second or third application. They may be from a closed plant or a discontinued process, and they find their way to the boneyard to be used at a later time for another application. Repurposed pumps are used primarily because of their convenience; they are paid for and readily available. Before reusing a pump in this manner, however, users should question if it is, in fact, the correct product for that specific application. Misapplied pumps typically require a significant amount of replacement parts and related labor, time and costs and may result in downtime. To avoid this pitfall, users should find out if the requirements have changed since the initial installation. They can check items such as viscosity, pH factor, temperature, product being conveyed, available net positive suction head (NPSH), type of supply, discharge pressure requirements and piping changes.2. The efficiency of the pumping system is impacted by the piping design layout.
Answers to the following questions and subsequent corrective action will help ensure maximum efficiency from the unit.- Does the piping schematic allow for the best efficiency?
- Are the velocities within the recommended standards?
- Has the number of Ls (elbows), Ts, Ys and miscellaneous fittings been minimized?
- Are the valves correctly applied and kept to a minimum?
- Are the correct fittings being used (e.g., eccentric versus concentric reducers)?
- Is the piping in good condition? Buildup of corrosion and wear can result in higher resistance to flow.
- Are the fittings, valves, etc., mounted no closer than the minimum distance from the pump as required?
- Is the pump located in the best location to minimize the runs and all twists and turns?
- Are valves being used to control flow instead of sizing the pump for the duty points?
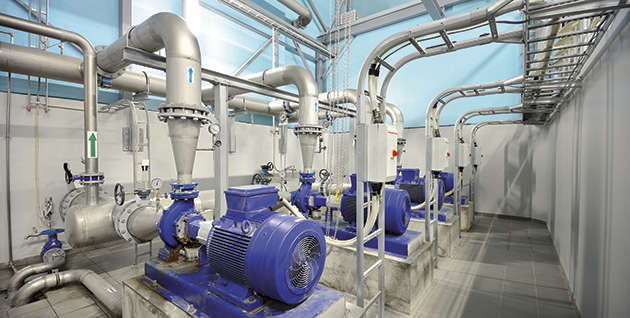