Identifying inefficient units is one thing, but fixing them can be time-consuming and expensive.
JoGar Energy Services
10/28/2016
Editor’s note: Peter Gaydon, Director of Technical Affairs at the Hydraulic Institute, wrote a response to this article in an attempt to clarify points raised by the author. Gaydon’s response appears in the January 2007 issue of Pumps & Systems.
The U.S. Department of Energy (DOE) earlier this year published a request to industry for assistance in developing new efficiency standards for pump systems. The federal notice (81 FR 5658) will lead to new federal regulations aimed at improving reliability and further reducing energy consumption nationwide in pumps, including circulator pumps.
Similar to the recent U.S. Environmental Protection Agency’s rule for boiler maximum achievable control technology (MACT), known as 40 CFR Part 63, this new program is a major challenge to the pump industry.
From an energy perspective, pump systems account for nearly 30 percent of power consumption in large industry. Pumps are the second-most utilized mechanism in American industry, next to electric motors. Life-cycle cost data for most pump systems indicates that energy usage accounts for 75 percent. The DOE has estimated that pump system energy usage accounts for more than $80 billion annually. Moreover, the average overall efficiency of many pump systems is about 50 percent. More than $10 billion per year of electrical power savings should be easily achieved in the U.S. with the new federal regulations. Power costs continue to rise, while thermal energy costs are expected to stabilize for several years with oil prices at or below $50 per barrel.
Historical Perspective
After nearly 45 years of working as a plant engineer and energy consultant in industrial manufacturing, I have experienced thousands of pump system anomalies, repairs and replacements. Many of those units had been in service for 30 or 40 years. Robust centrifugal pumps (and their induction motors) will keep running—and in the worst operating conditions. Municipal water pumps and process water system pumps in commercial and industrial facilities were high-quality, state-of-the-art installations in the 1950s through the ’80s. The large number of pumps that I recall involving refitting casing and impeller wear rings, spacing, and bearings would be shocking to manyyounger engineers. The equipment was designed to be robust, reparable and generally “spared” to ensure process reliability. Energy was cheap. Efficiency was a low priority. Today, however, many of those mature industrial and commercial facilities have closed. Most of those “experienced” teams of hydraulic-systems maintenance craftsmen and engineers have been downsized or retired. New installations are often not as robust, and many facilities generally are not as well-staffed as in the past. There are not enough utilities personnel to conduct routine preventive maintenance activities, let alone conduct a site-wide efficiency assessment of their pump systems—probably what the new DOE program rules will require. The new rules will assuredly focus primarily on system energy efficiency, but they may not necessarily be in tune with process operational reliability. Much technical review may be required in order to comply. Many newer pump installations have electronic diagnostic devices installed to monitor operating data such as pressure and temperature, flow rate and speed, motor amps, vibration, and even seal leakage. Alarm set points can alert staff of an anomaly. However, alarms do not readily alleviate an issue, nor do they identify system inefficiency directly. Some human response is usually required to resolve the problem.Pump Efficiency
The first (and obvious) requirement for affected facilities will be to develop (or update) their list of pumps. The old “80-20” rule should be used—yes, 20 percent of your pump systems will be using 80 percent of the energy. Prioritize those units that have a frequent repair history or that operate over a wide range of process conditions. Some pumps may have good efficiency, yet many may surprise you, especially those with changing load conditions or that have new variable speed drives (VSDs). Be careful: VSDs can produce better efficiency and reduce costs, but make sure that your support staff has expertise in electronics and controls. Not many VSDs will last 30 to 40 years like those induction-motor-driven pumps of yesteryear. In fact, VSDs have life expectancies similar to direct expansion (DX) air-conditioning systems—10 to 12 years at best—not to mention process downtime from harmonics, overheating, control device failure, etc. Pump performance curves and system operating data will be required to conduct a technical assessment (see Figure 1).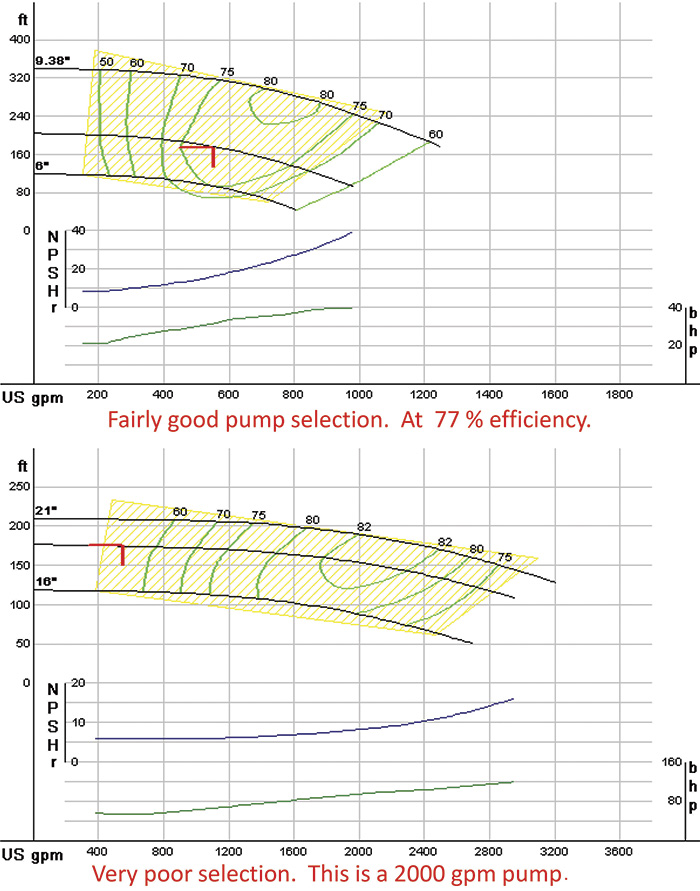
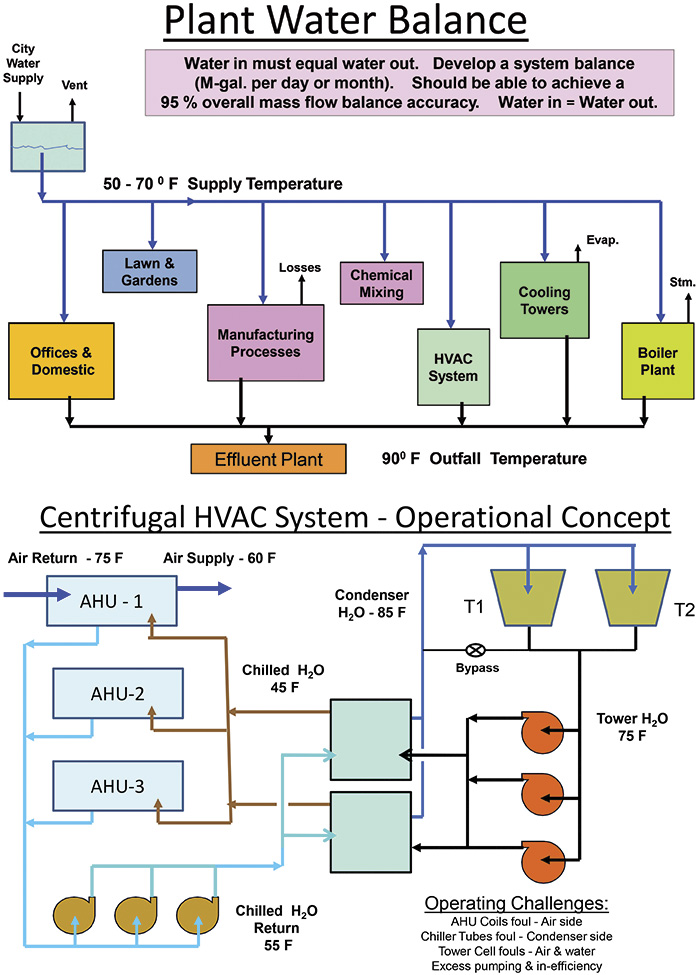