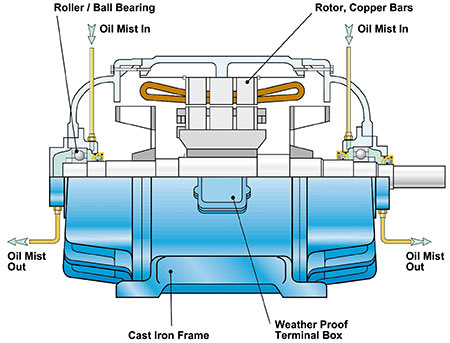
The issue of oil mist lubrication for electric motors in sizes up to 3,000 kilowatts (kW), and equipped with rolling element bearings, should not be an issue at all. If someone has kept track of articles on the subject, they may have found the answers to relevant questions in the March 1977 issue of Hydrocarbon Processing. An enlightened manager-technical expert encouraged the author (43 years old at the time) to share what was known: Oil mist was a superior lubrication method since the mid-1960s, when best-in-class users began to apply oil mist with great success on process pumps and electric motors.
Installations using pure oil mist allowed us to permanently dispense with troublesome oil rings, constant level lubricators, periodic oil changes and replenishing grease in electric motor bearings. Even ascertaining oil cleanliness became a non-issue because bearing housings were dry, oil mist floated to the top take-off “branches” of the large pipes that were called “headers,” and dust particles were left behind. Oil mist was soon recognized as the ultimate filter, and open oil containers were no longer defacing the well-scrubbed walkways in the company’s clean process units.
The 1977 article was candid in confirming that with the then available elastomeric V-rings between bearings and motor interiors, small amounts of oil mist traveled into the motor windings. However, two important facts were established:
- The lubricants used in pumps and motors did not attack or degrade epoxy insulations on motors manufactured since about 1953.
- The temperature rise measured on oil-coated windings remained well within allowable limits.
But 1977 is a long time ago, and two key developments1 should by now satisfy anyone contemplating the use of oil mist on electric motors. The more recent developments are described in two or three findings:
- Oil mist inlet and outlet ports should be arranged for through-flow, per Image 1, and small collector pots should be installed at the edge of the base plate. Coalesced mist is removed one per month from these pots; the coalesced oil can also be pumped back into the oil mist header from where it flows back (by gravity) into the oil mist generator reservoir.
- The purpose-designed magnetic face seal in Image 2 will prevent oil mist migration into the motor windings.2
- Electric motors should have an open weep hole for automatic moisture drain off.
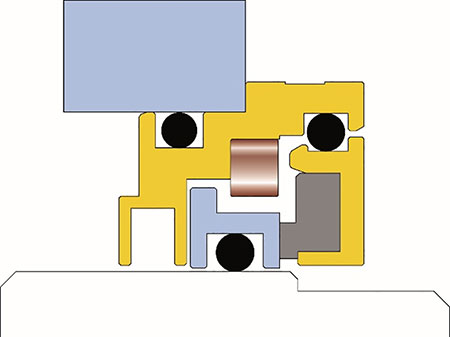
The bearing protector seal in Image 2 is designed with an advantageous closing pressure of only 0.5 pounds per square inch (psi); its face temperature increase is five to eight degrees C (9 to 14 degrees F) below that of its nearest competitor. Some of the products shown here have been in service for three years without discernable leakage, while similar products from other sources have been observed to leak after a few months of operation.
The cost justifications for plant-wide oil mist lubrication and for pump component upgrading are described in Refs. 2 and 3. Facilities that include electric motors in their plant-wide oil mist systems obtain rapid payback for their incremental investment. In the past 40 or more years, oil mist has yielded the additional benefit of protecting both running and standby equipment against the intrusion of dust and moisture. The frictional energy normally expended by bearings using liquid oil and grease is measurably reduced. By using the beast available engineered product, even the unsightly occasional leakage will no longer be a concern.
References:
- “Petrochemical Machinery Insights,” (2016), ISBN 978-0-12-809272-9
- “Optimized Equipment Lubrication, Oil Mist Technology and Storage Preservation,” (2020), ISBN 978-1-941872-98-7
- “Fluid Machinery Improvement: Life Extension for Pumps, Compressors and Steam Turbines,” (2020), ISBN 978-3-11-067413-2