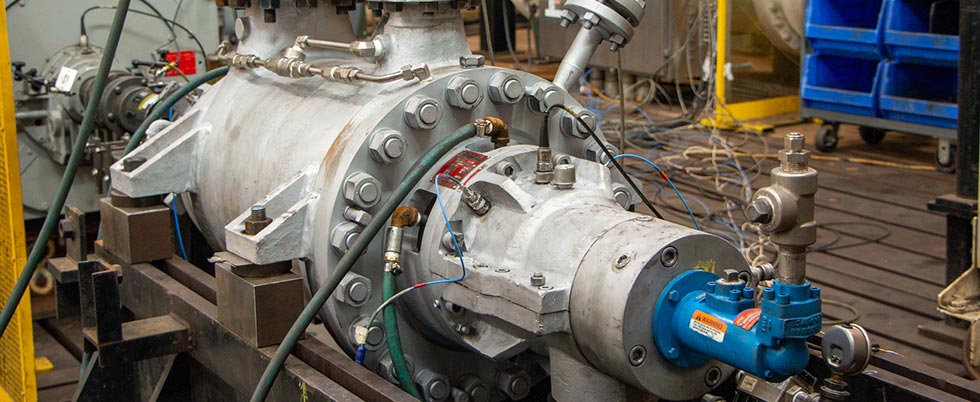
A Midwestern oil refinery sent a recently repaired multistage, between bearings barrel pump (BB5) to an aftermarket-focused pump performance test lab for testing and evaluation. The goal of the test was to verify post-repair performance on a refurbishment that had been carried out by the OEM.
Lead times at the OEM test lab would have extended the project completion date beyond what was acceptable for the refinery. Accepting the refurbishment without testing put the equipment at risk, as the repair included hydraulic modifications. An independent test lab was an ideal solution; not only would it provide an unbiased analysis, but it could provide a fast turnaround and could meet the refinery’s schedule.
The performance test indicated the expected performance supplied by the OEM did not match the actual performance delivered by the pump. More problematic, test preparation revealed a clearance error that would have decreased the life of the bearing. By choosing to use a third-party test lab to verify equipment operation, the end user was able to avoid unpleasant surprises when returning the pump to service.
Why Performance Test?
Testing can be applied to new pumps, refurbished pumps or reengineered pumps and focuses on verifying the performance characteristics of the equipment, as well as ensuring safe, reliable operation. The result of a certified performance test is a certified performance curve showing the differential head versus flow capacity, input power versus flow capacity and efficiency versus flow capacity curves over the total range of flow capacity for a given pump.
In the aftermarket, performance testing has several additional functions to assess changes in pump behavior and provide extra assurance during refurbishment. When changes are made to the pump hydraulics, the actual changes in performance can be measured and compared to the theoretical performance calculated during the modification. Similarly, when hydraulic components, such as casings or impellers, have
had substantial rework during a refurbishment, testing can verify the work completed did not inadvertently affect equipment performance.
In cases where a pump has been returned to service and is not behaving as expected, lab testing can map the actual performance of the equipment in a controlled environment. When discrepancies between the tested performance and the original curve are detected, the changes between the two curves can be analyzed to understand what components are affecting current performance.
Aftermarket pump testing can also be a useful resource when troubleshooting bad actor pumps. Test facilities have the capability to measure more than just flow and head, such as vibration, motor power, net positive suction head (NPSH) and other parameters that can be used in advanced diagnosis. Test labs have the additional capability of performing motor current signature analysis, which correlates motor current readings recorded in the frequency domain with different equipment failure mechanisms. All these tools can be used to identify problems and isolate design issues, which are detectable in the lab, from system issues, which are present only when measured in the field.
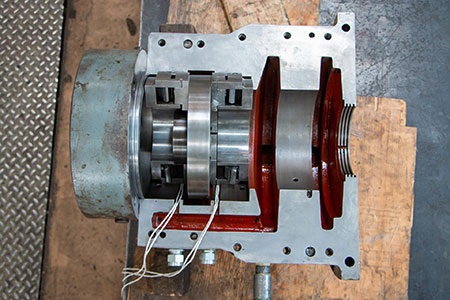
Quality Processes: Maximizing Test Efficiency & Minimizing Risk
Consistently providing a competitive testing time frame has required the aftermarket test lab to invest in both talent and rigorous processes. These processes maximize test efficiency and minimize risk to the equipment being tested. When a pump arrives at the testing facility, it undergoes a rigorous pretest evaluation to determine if the unit is mechanically sound to handle the test. In addition to ensuring a safe testing process, the evaluation has the added benefit of providing users with a quality inspection of their equipment.
In the case of the refinery’s BB5 pump, mechanics and engineers performed numerous checks on the pump components, including the thrust bearing. This inspection revealed a clearance between the thrust bearing and the bearing housing of 0.04 inches, which was larger than what the OEM specified in their repair documentation. Maintaining the design thrust bearing end play is important in establishing the optimal working environment for the bearing. Too little end play will limit allowance for misalignment or thermal expansion. Too much end play can inhibit the formation of the oil film on the unloaded side of the bearing and can affect the axial centralization of the rotor. It can also cause oil to build up in the clearance, which can overheat and damage the bearing and other components.
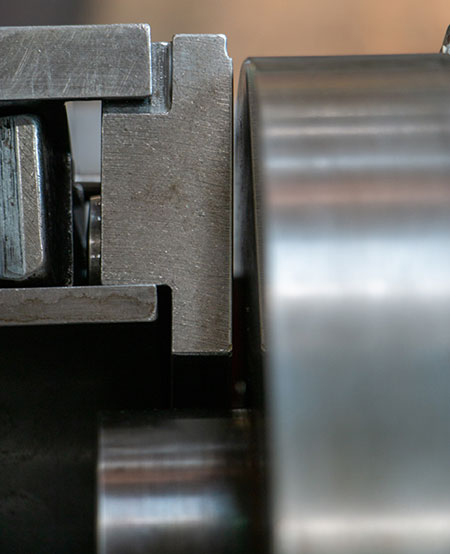
The inspection revealed a clearance between the thrust bearing and the bearing housing of 0.04 inches, which was larger than
OEM specifications.
When the thrust bearing clearance discrepancy was discovered, the test lab was able to take advantage of their co-location with the company’s service center to resolve the issue. The thrust bearing housing was machined to establish the bearing end play within the limits recommended by the manufacturer.
Results
When the pump is tested, test points are taken throughout the performance curve, including at low efficiency points where hydraulic instability and high bearing loads can be expected. Had the pump been tested as received, it is likely that it would have experienced high bearing temperatures and vibration, possibly damaging the bearing. The modified pump ran smoothly, exhibiting stable bearing temperatures and low vibration. The test proved its value beyond the discovery of the incorrect thrust bearing clearance when the performance data was analyzed. The actual performance of the equipment diverged significantly from the performance values provided by the OEM to the end user (Image 4). This will allow the end user to consider the best path forward to maximize the reliability and maintainability of their system.
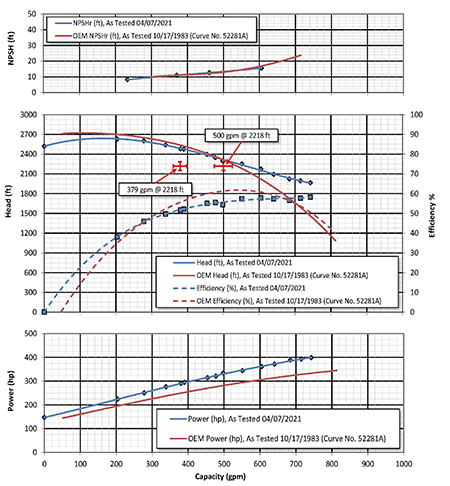
The actual performance of the equipment diverged from the performance values provided by the OEM to the end user.
Understanding the critical nature of the project delivery schedule, the test lab was able to meet its promised lead time despite the need to remediate the incorrect thrust bearing clearance prior to testing. The pump was inspected, repaired, tested and returned to the end user within seven days of arriving at the performance test lab, exceeding expectations. In this case, the precheck caught a potentially hazardous situation with a critical unit that, if left unaddressed, could have caused a catastrophic pump failure.