09/10/2015
Remote monitoring software as part of a complete preventive maintenance plan can provide the insight and data required to troubleshoot pump system problems and prevent total equipment failure. For many facilities, these tools have been instrumental in minimizing downtime and costly repairs while providing information necessary for preventing future issues.
Wiped Bearing on a Feedwater Pump
On July 14, a remote monitoring software solution detected changes in the mechanical profile of the outboard bearing of a feedwater pump at a combined-cycle power plant. Vibration on the outboard bearing increased to 7.55 millimeters per second (mm/s) from an expected value of 3.98 mm/s. At the same time, the temperature in this outboard bearing jumped to an actual value of 270 degrees F (132 C) before quickly dropping to values around 170 F (77 C). The temperature for this bearing was expected to remain around 190 F (88 C). The software provider sent a high-priority notification to the facility and started closely monitoring this issue.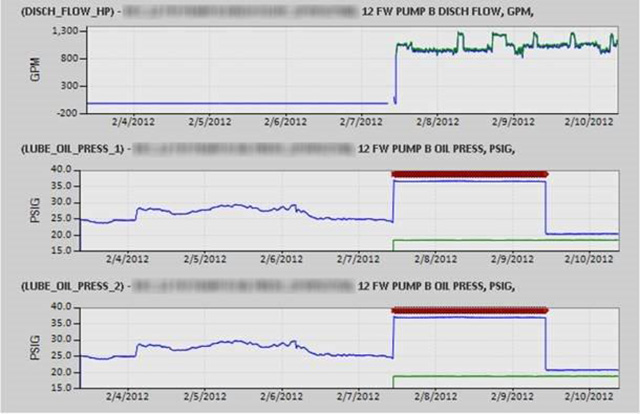
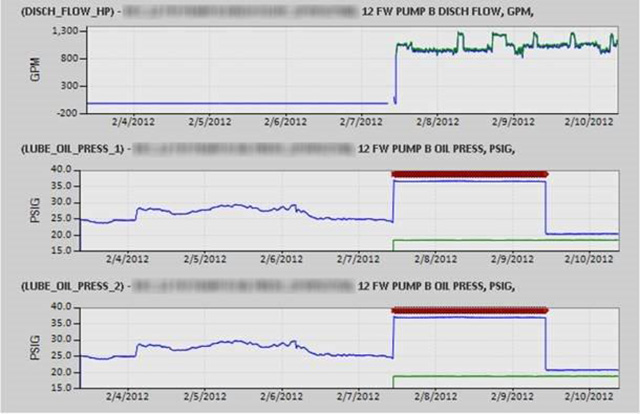