The self-priming pump systems offer flow rates up to 9,770 gallons per minute and can handle solids up to 4.9 inches in diameter.
03/07/2016
In 2007, the Authority of the Panama Canal (ACP) embarked on the ambitious Panama Canal Expansion Program, the largest development project since the canal’s original construction. Scheduled for completion in the second quarter of 2016, the expansion project will result in the addition of a new traffic lane and two new lock complexes, one on the Atlantic Ocean and the other on the Pacific. The program is expected to have a direct, positive impact on international maritime trade. The end result will double the canal’s capacity and allow the passage of larger post-Panamax ships, which are mainly used for longer routes.
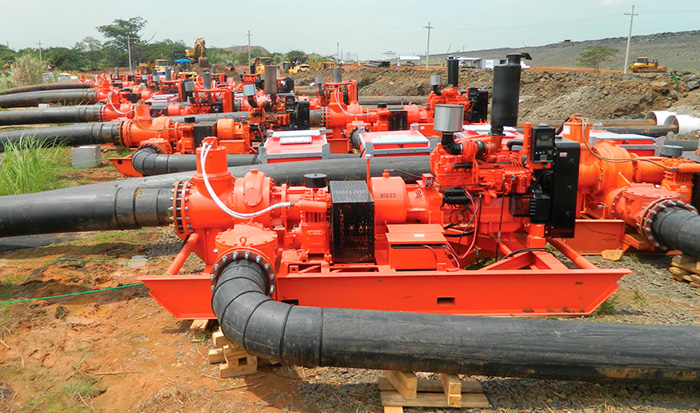
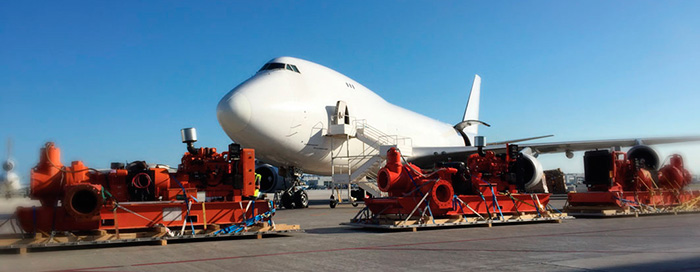